Un'analisi numerica di DDMRP
DDMRP sta per Demand Driven Material Requirements Planning. Negli ultimi anni, la popolarità di DDMRP è cresciuta in alcuni settori, occupando la nicchia che lean manufacturing o six sigma una volta occupavano. Eppure, cosa ci si può veramente aspettare da DDMRP e quanta novità porta per quanto riguarda l-ottimizzazione supply chain?
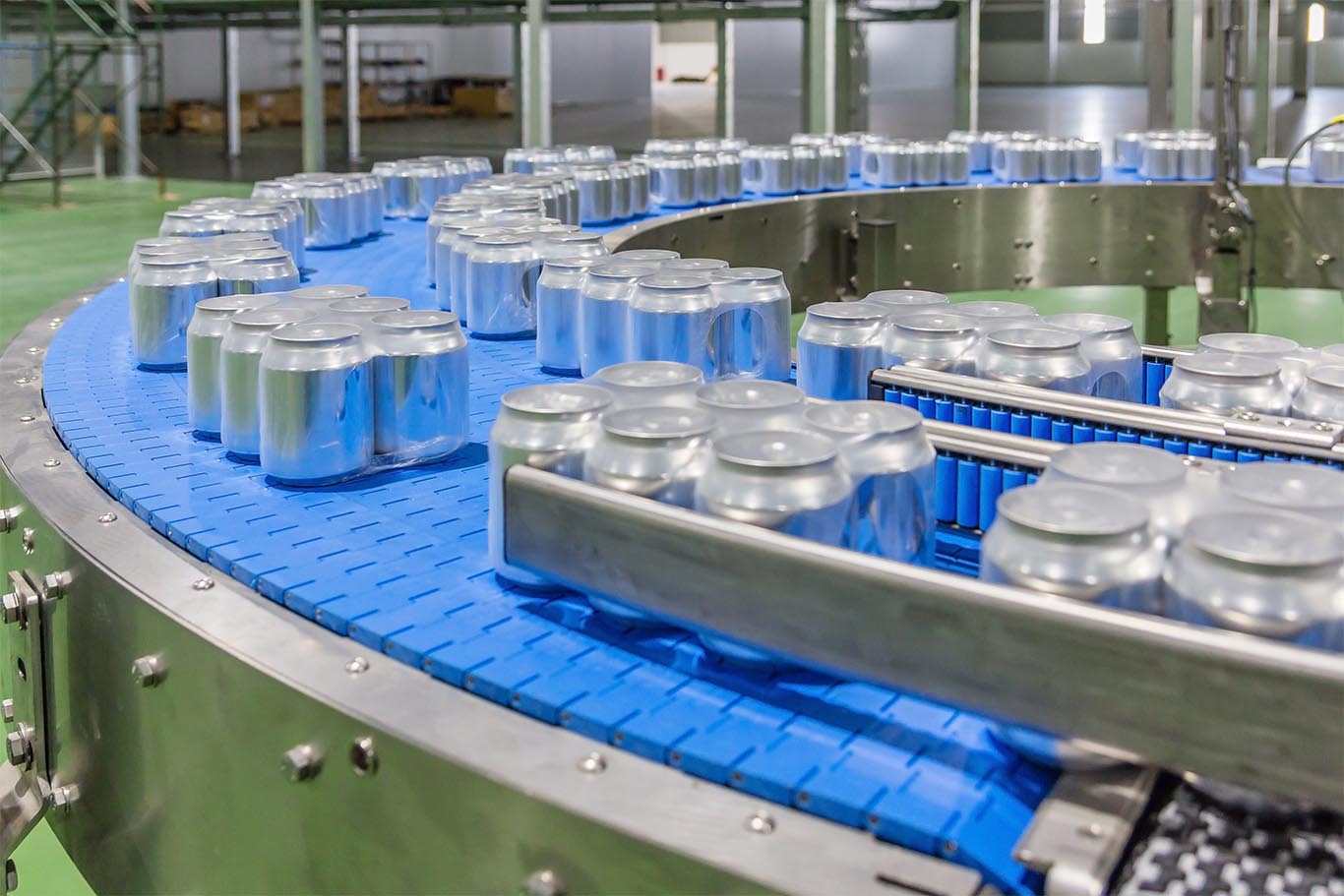
Per affrontare questa questione, esaminiamo DDMRP da una prospettiva numerica, cioè considerando DDMRP come un insieme di ricette numeriche1 per ottenere un’ottimizzazione delle prestazioni misurabile di una determinata supply chain. Infatti, dato che tutti i benefici enunciati dagli autori di DDMRP sono obiettivi quantificati (es: raggiungimento del 97-100% di performance in orario del fill rate2), sembra giusto adottare una prospettiva numerica per valutare i meriti di questo approccio.
Gli autori di DDMRP affermano che questo approccio apporta quattro innovazioni chiave all’ottimizzazione supply chain, a sapere:
- disaccoppiamento dei lead times3
- l’equazione del net flow4
- le esplosioni disaccoppiate5
- la priorità relativa6
Saltando alle conclusioni, l’attenta analisi di ciascuno di questi punti - approfondita nei dettagli di seguito - indica che c’è ben poco di sostanziale nelle audaci affermazioni di DDMRP. Le ricette numeriche proposte da DDMRP non sarebbero nemmeno state considerate all’avanguardia alla fine degli anni ‘50, dato che il nascente campo della ricerca operativa aveva già scoperto strategie di ottimizzazione numerica, indubbiamente più sofisticate e migliori, all’epoca.
I miglioramenti che si dice vengano ottenuti da DDMRP partono da una base errata: gli MRP - proprio come ERP - tipicamente non offrono alcuna capacità di ottimizzazione numerica7. I loro sistemi di database relazionali sottostanti non sono affatto adatti a gestire carichi di lavoro consistenti nell’elaborazione dei dati, anche se si considerano gli hardware di computing moderni. Pertanto, nonostante il discorso di molti fornitori di software aziendali - operanti sul lato transazionale del problema - è scorretto considerare gli MRP come base per l’ottimizzazione supply chain.
Disaccoppiamento dei lead times
Gli MRP, basati su database relazionali (SQL) e saldamente ancorati nel mondo dei software di asset management, hanno poche o nessuna capacità nell’elaborazione dei dati. Di conseguenza, non sorprende che l’analisi dei lead times non sia il punto forte di tali soluzioni. Considerando il grafico dei requisiti generato dalla Distinta Base, molti MRP offrirebbero solo due analisi dei lead times estremamente semplicistiche, a sapere:
- manufacturing lead time, che è eccessivamente ottimistico e presuppone che l’inventario sia sempre disponibile ovunque, sottostimando di gran lunga i lead times.
- cumulative lead times, che è eccessivamente pessimista e presuppone che l’inventario manchi ovunque, sovrastimando di gran lunga i lead times.
DDMRP propone di rimediare a questa situazione utilizzando uno schema di colorazione binaria del grafo, in cui certi nodi - ciascuno associato a un prodotto o a un componente - sono designati come punti di disaccoppiamento. Si assume quindi che tali nodi mantengano sempre un inventario utilizzabile; e la metodologia di DDMRP assicura che ciò avvenga effettivamente.
Una volta scelti i punti di disaccoppiamento, una scelta che viene effettuata manualmente dal praticante della supply chain, i calcoli dei lead times possono essere eseguiti con un metodo che alterna tra i due metodi di calcolo elencati sopra a seconda del colore di ciascun nodo. Con una selezione accurata dei punti di disaccoppiamento, i valori dei lead times possono essere notevolmente ridotti.
Ci sono tre critiche principali a questo approccio.
- la riduzione dei lead times è in primo luogo un artefatto dei calcoli causato da una definizione rivista. Il sistema supply chain - nel suo insieme - mantiene un’inerzia simile nel contesto di un mercato in continuo mutamento. Infatti, invece di avere l’inerzia del sistema direttamente riflessa nei lead times, essa è ora nascosta attraverso i buffer mantenuti nei punti di disaccoppiamento. I lead times possono essere stati ridotti, ma l’inerzia del sistema no.
- affidarsi agli input umani per affinare un processo di ottimizzazione numerica non è una proposta ragionevole considerando il costo delle risorse di calcolo moderne. L’ottimizzazione di meta-parametri potrebbe essere accettabile, ma non un intervento fine a ogni nodo del grafo. In particolare, la mia osservazione casuale delle supply chain moderne è che la necessità di input umani è uno dei maggiori fattori dietro l’inerzia dell’intero sistema. Aggiungere un ulteriore livello di taratura manuale - la scelta dei punti di disaccoppiamento - non rappresenta un miglioramento in tal senso.
- sebbene, si possa sostenere, le stime dei lead times di DDMRP possano essere migliori dei numeri grezzi forniti dagli MRP, la base di riferimento è incredibilmente ingenua. Persino i metodi base di Monte Carlo - introdotti da Nicholas Metropolis nel 1947 - superano tutti quei metodi per quanto riguarda la stima dei lead times, incluso DDMRP.
In conclusione, i lead times disaccoppiati difficilmente possono essere considerati innovativi e offrono una falsa percezione di compressione dei lead times, nascondendo al contempo l’inerzia del sistema supply chain sotto uno schema di colorazione del grafo.
L’equazione del net flow
Per affrontare il problema della generazione degli ordini di approvvigionamento, DDMRP ha introdotto un concetto fondamentale di net flow. L’equazione del net flow viene introdotta in DDMRP come segue:
On-Hand + On-Order – Qualified Sales Order Demand = Net Flow Position.
Questa quantità può essere interpretata come la quantità di scorte disponibile per far fronte alla parte incerta della domanda. Attraverso i net flows, DDMRP sottolinea che solo la porzione incerta della domanda richiede effettivamente un qualsiasi tipo di analisi statistica. Gestire la domanda futura già nota è una questione puramente di adesione a un piano esecutivo deterministico.
Il calcolo del net flow è una semplice combinazione di tre variabili SKU non banali ma ampiamente utilizzate. Gran parte della complessità effettiva è nascosta in queste variabili, che possono essere meno innocue di quanto sembri:
- lo stock disponibile è soggetto a inaccuratezze di inventario
- lo stock in ordine è soggetto a lead times variabili
- molte sfumature di grigio nel distinguere gli ordini di vendita qualificati da quelli non qualificati
In ogni caso, è difficile affermare una notevole novità introducendo quella che è forse una combinazione banale di variabili ampiamente utilizzate all’interno dei sistemi supply chain. Inoltre, DDMRP non sta svelando proprietà nascoste / inedite / non evidenti dell’espressione net flow.
Algoritmi sofisticati per prevedere con dipendenze parzialmente note sono conosciuti da decenni, con pubblicazioni risalenti ai primi anni ‘908; con un grado di raffinatezza che va ben oltre le ricette numeriche presentate in DDMRP.
Esplosione disaccoppiata
Il termine “decoupled explosion”, coniato dagli autori di DDMRP, è la diretta conseguenza dello schema di colorazione binaria del grafo introdotto nella sezione precedente: le Distinte Base (BOM) non vengono enumerate in modo ricorsivo oltre qualsiasi nodo contrassegnato come “punto di disaccoppiamento”. Considerando il trattamento applicato sia ai lead times che alle BOM, osserviamo che DDMRP sfrutta i “punti di disaccoppiamento” come confini di partizionamento del grafo complessivo della supply chain.
Questo schema di partizionamento del grafo è in qualche modo simile a ciò che comunemente si conosce come algoritmo divide-et-impera, risalente al lavoro di John von Neumann nel 1945. Tuttavia, le ricette numeriche di DDMRP mancano della seconda parte degli approcci algoritmici divide-et-impera, ovvero la ricombinazione delle sotto-soluzioni in una soluzione più efficiente per il problema nel suo complesso. DDMRP partiziona il grafo della supply chain, risolvendo ogni sottografo con metodi MRP “classici”, e si ferma qui. Non avviene alcuna ulteriore ottimizzazione numerica a livello di sistema oltre quella locale eseguita in ciascun sottografo.
Pertanto, la principale critica a queste esplosioni disaccoppiate è che, per loro natura, completano il partizionamento dei grafi della supply chain in sottografi indipendenti, imponendo con questo processo un limite netto all’ottimizzazione che può essere raggiunta per l’intero sistema supply chain; proprio perché non può avvenire alcun tipo di accoppiamento tra gli elementi della partizione.
Questo aspetto potrebbe sembrare controintuitivo per un non specialista, ma da una prospettiva di ottimizzazione numerica, una partizione statica di un sistema rappresenta semplicemente una riduzione dei gradi di libertà disponibili al processo di ottimizzazione, e quindi una riduzione della capacità del processo di trovare effettivamente una soluzione migliore.
Priorità relativa
L’assunto chiave oltre i punti di disaccoppiamento in DDMRP è che lo stock sia sempre disponibile per quei SKU. Tuttavia, poiché avvengono fluttuazioni casuali della domanda o del lead time, il sistema supply chain sotto DDMRP potrebbe discostarsi da questo presupposto. Pertanto, DDMRP afferma che le decisioni della supply chain (ad es. ordini di acquisto o ordini di produzione) devono essere priorizzate in base alla loro capacità relativa di riportare il sistema in uno stato in cui i presupposti originali siano rispettati.
Ci sono due critiche principali allo schema di priorizzazione proposto da DDMRP. Innanzitutto, la priorizzazione guarda all’interno del sistema supply chain invece che all’esterno. In secondo luogo, la priorizzazione è unidimensionale e pertanto incapace di affrontare la maggior parte degli scenari non banali oltre il caso uniforme forward.
Il sistema supply chain esiste per servire interessi esterni (esogeni). Per dirla in modo più diretto, l’azienda massimizza i dollari di ritorno generati dalla sua interazione con l’economia in generale; eppure, DDMRP ottimizza i percentuali di errore rispetto a obiettivi forse arbitrari. Infatti, la priorizzazione, come definita da DDMRP, guarda all’interno: dirige il sistema supply chain verso uno stato coerente con i presupposti alla base del modello DDMRP stesso - ossia la disponibilità di stock nei punti di disaccoppiamento. Tuttavia, non vi è alcuna garanzia che questo stato sia in linea con gli interessi finanziari dell’azienda. Questo stato potrebbe addirittura andare contro gli interessi finanziari dell’azienda. Ad esempio, nel caso di un marchio che produce molti prodotti a basso margine che sono sostituti quasi perfetti l’uno dell’altro, mantenere elevati livelli di servizio per un determinato SKU potrebbe non essere un’opzione redditizia se i SKU concorrenti (quasi sostituti) hanno già un eccesso di inventario.
Pertanto, lo schema di priorizzazione proposto da DDMRP è fondamentalmente unidimensionale: l’adesione ai propri obiettivi di stock (il buffer). Tuttavia, le decisioni reali della supply chain sono quasi sempre problemi multidimensionali. Ad esempio, dopo aver prodotto un lotto di 1000 unità, un produttore solitamente colloca tali 1000 unità in un container per il trasporto marittimo; ma se un stock-out è imminente lungo la supply chain, potrebbe essere redditizio spedire 100 unità (su 1000) tramite aereo per mitigare preventivamente lo stock-out imminente. Qui la scelta della modalità di trasporto rappresenta una dimensione aggiuntiva alla sfida della priorizzazione supply chain. Per affrontare questa sfida, il metodo di priorizzazione richiede la capacità di integrare i driver economici associati alle diverse opzioni a disposizione dell’azienda.
Altre dimensioni che devono essere considerate come parte della priorizzazione possono includere:
- aggiustamenti dei prezzi, per aumentare o ridurre la domanda (eventualmente canali di vendita secondari)
- costruire o acquistare, quando sul mercato si possono trovare sostituti (tipicamente a un premio)
- date di scadenza degli stock (che richiedono un’analisi approfondita della composizione dell’inventario)
- rischi di reso (quando i partner distributivi hanno la possibilità di restituire le merci invendute)
Pertanto, sebbene DDMRP sia corretto nell’affermare che la priorizzazione è un approccio più flessibile rispetto agli approcci binari tutto o nulla implementati dai MRP “classici”, lo schema di priorizzazione proposto da DDMRP risulta piuttosto debole. Ancora una volta, i MRP non dovrebbero essere utilizzati come base di riferimento per valutare il merito di una ricetta di ottimizzazione numerica della supply chain.
Conclusioni
Le quattro innovazioni chiave di DDMRP, identificate come tali dagli autori di DDMRP, si rivelano essere deboli per quanto riguarda l’ottimizzazione numerica e obsolete di diverse decadi se si considera la storia dell’ottimizzazione numerica e della ricerca operativa.
Molte conclusioni sono tratte erroneamente sul falso presupposto che i MRP siano una base di riferimento rilevante per l’ottimizzazione della supply chain; cioè, migliorare l’MRP significherebbe un miglioramento dell’ottimizzazione della supply chain. Tuttavia, i MRP, come tutti i sistemi software progettati centralmente attorno a database relazionali, non sono affatto adatti alle sfide dell’ottimizzazione numerica.
I produttori bloccati dai limiti dei loro MRP non dovrebbero cercare miglioramenti incrementali dell’MRP stesso, poiché l’ottimizzazione numerica è fondamentalmente in contrasto con il design dell’MRP, ma piuttosto sfruttare tutti gli strumenti software e le tecnologie che sono stati progettati per le prestazioni numeriche fin dall’inizio.
Riferimenti
-
Il termine recipe non ha una connotazione negativa. Usiamo questo termine come in Numerical Recipes: The Art of Scientific Computing di William H. Press, Saul A. Teukolsky, William T. Vetterling, Brian P. Flannery ↩︎
-
A partire da marzo 2019, i benefici presentati per promuovere DDMRP sono (sic): gli utenti raggiungono costantemente una performance in orario del 97-100% del fill rate, in diversi settori industriali si sono ottenute riduzioni dei lead times superiori all'80%, e si registrano riduzioni tipiche dell’inventario del 30-45% pur migliorando il servizio al cliente. ↩︎
-
Decoupled Lead Time, The DDMRP Innovation Series: Parte #1, di Chad Smith, gennaio 2018 ↩︎
-
L’Equazione del Flusso Netto, La serie di innovazioni DDMRP: Parte #2, di Chad Smith, febbraio 2018 ↩︎
-
Esplosione Disaccoppiata, La serie di innovazioni DDMRP: Parte #3, di Chad Smith, febbraio 2018 ↩︎
-
Priorità Relativa, La serie di innovazioni DDMRP: Parte #4, di Chad Smith, febbraio 2018 ↩︎
-
Nonostante i loro nomi, e frequentemente nonostante le affermazioni dei fornitori, né gli ERP né gli MRP hanno qualcosa a che fare con la pianificazione. L’intero scopo di questi sistemi è gestire e tracciare le risorse; non prendere alcun tipo di decisioni per ottimizzare nulla. Per ulteriori dettagli Gestione vs Ottimizzazione. ↩︎
-
Previsione utilizzando domande parzialmente note, di Sunder Kekre, Thomas E. Morton, Timothy Smunt, febbraio 1990 ↩︎