Scheduling Optimization: A Programmatic Solution
Every now and then, a methodology emerges that borders on magical. To outside observers, it can seem like sorcery, whereas for experts in the field, it is simply the next inevitable step in the ceaseless march of technology. To try and bridge this divide, I have written a paper with the aim of white-boxing for the general audience Lokad’s latest breakthrough: scheduling optimization.
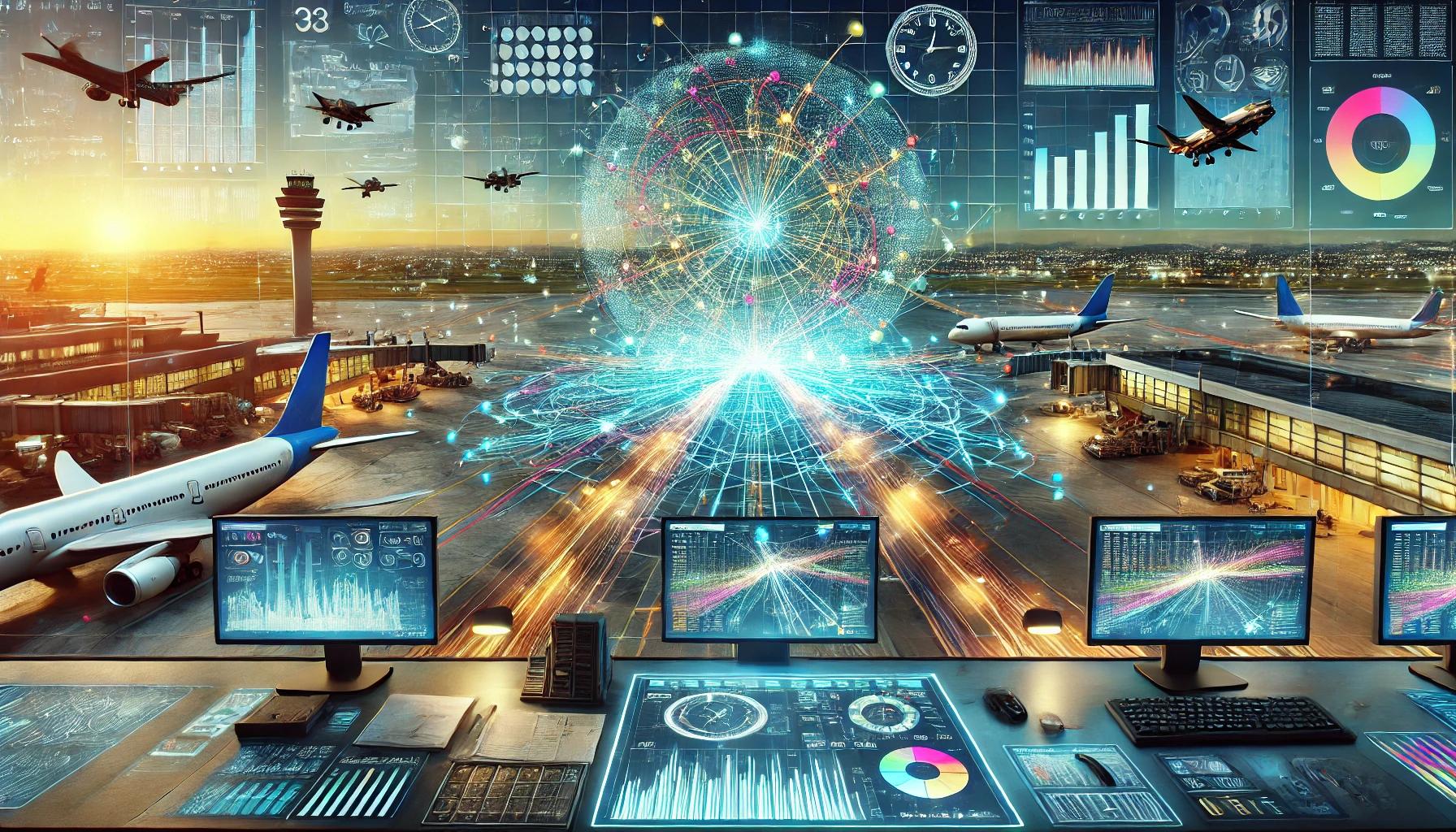
Scheduling optimization is the process of generating an efficient sequence of actions (e.g., to produce/repair an engine) that maximizes both resource utilization (parts, tools, people) and financial outcomes. This sequence of actions accounts for the uncertainties and daily disruptions companies encounter. Such a sequence needs to be generated at least once a day (typically overnight), and regenerated any time a resource that you thought would be available is missing (e.g., a technician is sick, a part is missing, or a tool is broken).
Lokad can regenerate a sequence of steps - if needed - for enormous bills of resources1 and complex processes in the time it take to brew a coffee. Critically, these “exceptions” are the norm, as emergencies (absent resources) are a feature of the system, not a bug.
This initial version is written from the perspective of aerospace OEMs and MROs, but the fundamental principles described here apply to any manufacturing, production, or repair company (particularly the sections You Have a Bill of Resources, Probability Theory in Scheduling, and Why FIFO Fails).
As always, the aim is to create a dialogue on these ideas, so anybody who wishes to provide feedback is warmly invited to do so. My email is in the white paper, you can ping me on LinkedIn, or you can simply reach out at contact@lokad.com.
In closing, this paper was produced in close collaboration with several talented and experienced supply chain experts, including Simon Schalit, Luciano Lisiotti, Fabian Hoehner, Tristan Oualid, Rémi Quentin, Victor Noisette, and Alexey Tikhonov. An additional thanks to Timothy Russo and Joshua Bradshaw for generously providing external review. Everyone’s input was greatly appreciated.
-
This concept is proposed as a more comprehensive replacement for bill of materials (BOM). Whereas a BOM focuses on the physical parts required to manufacture or repair something, a bill of resources (BOR) refers to all the parts, tools, and people (particularly their skills) required to complete the process. This point is explained in detail in the white paper. ↩︎