Kanban (Gestione dell'Inventario)
Il metodo Kanban (billboard in giapponese), come Lean Manufacturing ha le sue radici nel produttore automobilistico giapponese Toyota. È stato implementato per migliorare l’efficienza produttiva e ridurre gli sprechi, fornendo un processo semplice e visivo di riapprovvigionamento dei materiali, in modo che ogni fase del processo produttivo riceva la quantità giusta in tempo per operare senza intoppi, senza accumulare materie prime o componenti. Fondamentalmente, ogni volta che viene consumata una certa quantità di materiale - visibile immediatamente come una scatola vuota o uno scaffale vuoto -, viene inviato un segnale visivo (tipicamente una scheda) per attivare il riapprovvigionamento della stessa quantità. Da qui, il sistema Kanban ha guadagnato influenza in diversi settori, in particolare nello sviluppo software con la filosofia di gestione Agile, o in supply chain management, come un metodo semplice per evitare eccedenze.
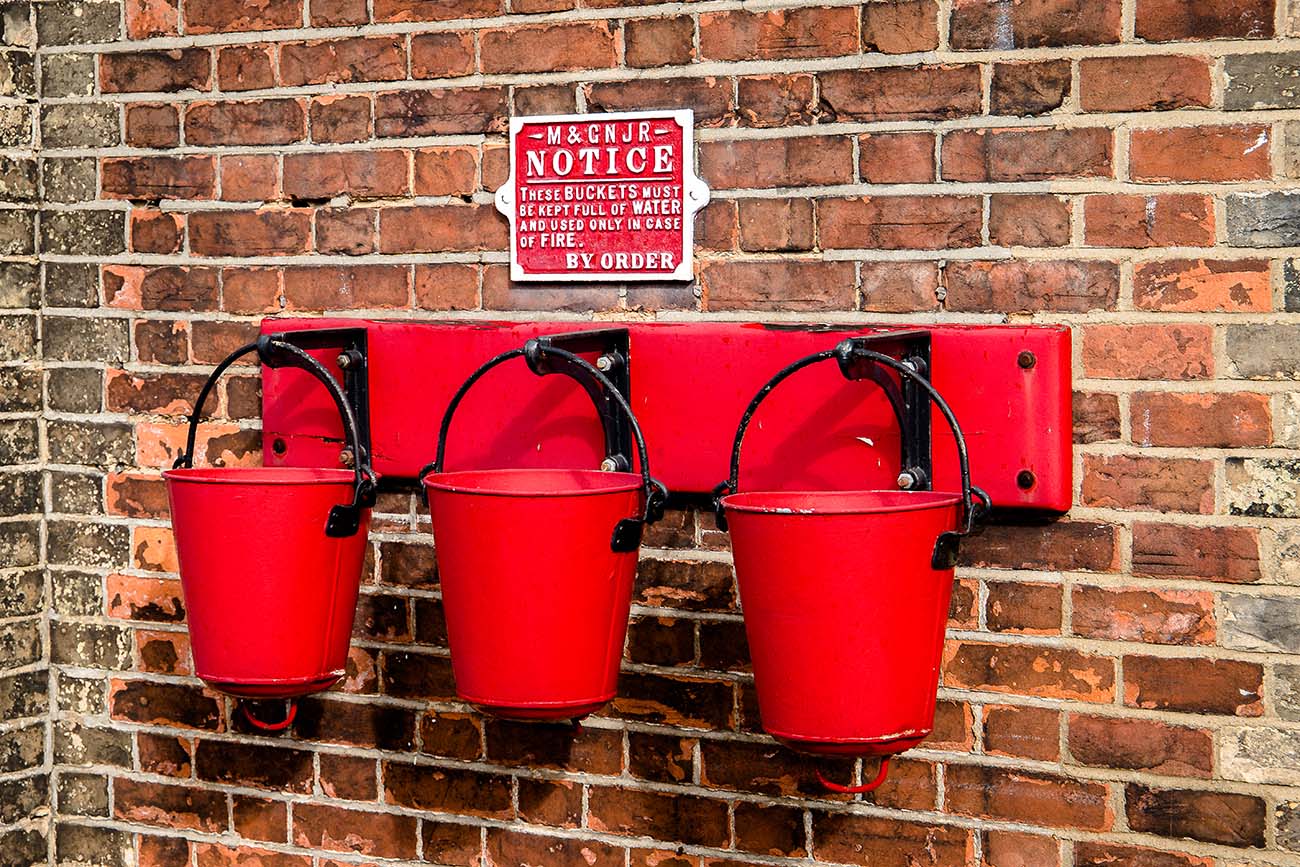
Origini del Kanban ed evoluzione oltre la manifattura
Originate negli anni ‘40/‘50, in un contesto post Seconda Guerra Mondiale con praticamente nessun computer o digitalizzazione disponibile, il Kanban ebbe il grande merito di razionalizzare il mondo della manifattura attraverso un sistema semplice ed elegante, costituito da poco più che schede di carta e scatole o contenitori.
Nel loro impegno di ridurre gli sprechi - e quindi gli stock inutili nei stabilimenti o nei negozi - gli ingegneri Toyota idearono un sistema in cui il riapprovvigionamento era direttamente legato al consumo effettivo. Scelsero di seguire un sistema pull anziché push. Esiste una dicotomia fondamentale tra i due. Tradizionalmente, la produzione di beni si basa sull’anticipazione della domanda (solitamente materializzata da previsioni di domanda); i beni vengono prodotti in anticipo e poi spinti sul mercato. Con il pull, il sistema è trainato dalla domanda e i beni vengono realizzati su ordinazione. La produzione e il riapprovvigionamento avvengono solo quando necessario e non in previsione della domanda.
Esistono diversi modi per implementare un sistema Kanban. Le espressioni più semplici sono il sistema a 2 contenitori o il sistema a 3 contenitori. Ad esempio, un magazzino che utilizza un sistema a 2 contenitori espone scaffali dimensionati per ospitare due scatole piene di articoli, ciascuna scatola contenente una scheda Kanban, tipicamente con informazioni sull’articolo (referenza, codice a barre, quantità, ecc.). Ogni volta che una scatola è vuota, essa viene messa da parte per essere riutilizzata successivamente e la scheda Kanban viene spostata in una posizione visibile - tipicamente alla fine della fila, su un tavolo o contenitore apposito. Mentre la seconda scatola è in uso, le schede Kanban esposte vengono prelevate da un addetto che andrà a recuperare una scatola piena dai depositi e a sostituire la scheda Kanban al suo interno. Idealmente, quando l’addetto porta il riapprovvigionamento, l’altra scatola non è ancora completamente esaurita, ma quasi. L’idea è semplice: c’è una scatola principale e una di riserva; quando quella di riserva inizia ad essere utilizzata, è il momento di rifornire quella principale e così via. In effetti, la scatola di riserva non è altro che una scorta di sicurezza.
In un sistema a 3 contenitori implementato in una fabbrica, un contenitore/scatola di materiali viene posizionato sul pavimento della fabbrica per essere lavorato nella produzione, un contenitore si trova al livello del magazzino della fabbrica e uno presso il fornitore. Quando il contenuto del primo contenitore è stato utilizzato nel processo produttivo, viene immediatamente inviato un segnale al magazzino per prelevare il contenuto del contenitore pieno presente nello store. A sua volta, il magazzino della fabbrica, ora in possesso di un contenitore vuoto, preleva il contenuto del terzo contenitore detenuto dal fornitore, che poi lo riempirà. Lo stock entra solo quando viene consumato ed esaurito. Un contenitore vuoto crea un segnale Kanban per ordinare la spedizione di ulteriori materiali in una quantità predeterminata. Ancora, nessun stock inutile viene mantenuto oltre il contenitore a livello del magazzino della fabbrica - un buffer o scorta di sicurezza - e il processo si basa sulla sostituzione fluida dei contenitori e sulla capacità del fornitore di elaborare gli ordini di riapprovvigionamento senza ritardi non previsti, ovvero non più del tempo necessario per svuotare un contenitore.
Proprio come il concetto Lean, il Kanban, con l’idea di schede o segnali che portano visibilità lungo il ciclo produttivo e evitano accumuli inutili, ha fiorito ben oltre il campo della manifattura. È stato ampiamente adottato nello sviluppo software o nel marketing come metodo di gestione del workflow per materializzare fasi logiche. Può essere semplice come presentare una bacheca di attività con tre colonne (Da fare / In corso / Fatto), con schede che evidenziano parti del progetto da realizzare e da assegnare ai membri del team. Strumenti come Trello possono fornire sistemi Kanban utili ed ergonomici per la gestione di progetti.
Lo sviluppo software ha perfezionato il processo con la gestione Agile. Una bacheca mostrerebbe contenitori come Build / Test / Complete. Viene stabilita una lista di attività prioritarie, come le funzionalità da sviluppare basate sul feedback degli utenti; qualsiasi sviluppatore può prendere una scheda da questa lista per sviluppare una particolare funzionalità; una volta sviluppata, tale funzionalità entra in una fase di test prima di essere rilasciata. Inoltre, ogni contenitore ha un limite al Work In Progress pensato per adattarsi alla capacità del team: in pratica, un numero massimo di schede può essere collocato in un contenitore. Il vantaggio di una tale bacheca è la facile visualizzazione, per tutto il team, delle attività da svolgere, l’identificazione rapida dei potenziali colli di bottiglia creati (ad esempio, l’accumulo di schede nel contenitore di Testing) e la capacità di tenere traccia dell’efficienza del workflow (quante schede vengono gestite, quanto velocemente passano da una fase all’altra, ecc.).
Pro e contro
Pro
Bella nella sua semplicità e nel suo design, il Kanban offre molti vantaggi che possono spiegare perché il metodo sia diventato così diffuso. Innanzitutto, un tale sistema è facile da comprendere e da implementare - almeno una versione semplice del Kanban lo sarebbe - guadagnando quindi consensi sia dal management sia dai team, e rendendo il change management meno impegnativo. È inoltre flessibile e versatile per natura e può facilmente adattarsi alle specificità di un’azienda o essere compatibile con i processi già in atto. Spetta ad ogni azienda definire i propri contenitori e le fasi logiche che abbiano senso all’interno dell’organizzazione. Semplici analisi e report possono a loro volta essere prodotti basandosi su un sistema Kanban per analizzarne l’efficienza o le carenze relative a una fase specifica o un’altra.
Una delle ragioni principali per cui il Kanban è così facile da comprendere è il suo uso di segnali visivi: una scheda, uno spazio vuoto o una scatola. In un sistema Kanban ideale, tutto è progettato per rendere le cose evidenti. Scatole vuote sono collocate in posizioni ben visibili, tavoli di dimensioni specifiche possono essere disposti per esporre articoli difettosi in modo che venga lanciato un allarme quando il tavolo è pieno e non vi è spazio per ulteriori articoli, ecc. Le schede sono solitamente di colori vivaci e utilizzano caratteri di grandi dimensioni; possono anche contenere informazioni aggiuntive come ricette o serie di operazioni da compiere per raccogliere tutte le informazioni semplici e rilevanti in un unico posto. L’idea principale è quella di poter valutare una situazione con un solo sguardo (bisogno di riapprovvigionamento, collo di bottiglia, accumulo di articoli difettosi, ecc.) e agire di conseguenza in maniera molto routinaria e automatica, quasi senza rifletterci troppo.
Inoltre, affidandosi a semplici segnali visivi come le schede, il Kanban non ha bisogno dell’IT per funzionare. Oggi esistono versioni digitali del Kanban (e-Kanban), con schede dematerializzate, integrate direttamente negli ERPs, ecc. Hanno i loro vantaggi e possono ridurre alcuni errori manuali, ma uno dei grandi punti di forza del Kanban è che è stato progettato per funzionare in un mondo senza computer. Un’organizzazione può implementare il Kanban senza alcuna dipendenza dall’IT e per lavoratori senza accesso ai computer - e quindi senza necessità di formazione per l’uso di terminali e simili.
Il modo in cui il Kanban è progettato, con segnali evidenti che richiamano sempre la medesima azione immediata in maniera ripetitiva e inequivocabile, lo rende un sistema in tempo reale, ancor di più se non è coinvolto l’IT. Una volta implementato il sistema, le azioni sono automatizzate e è necessaria poca comunicazione all’interno del team. Vale la pena sottolineare questo, poiché quasi tutte le altre alternative introducono ritardi legati al processo decisionale (fasi di validazione, autorizzazioni e così via).
Queste caratteristiche rendono il Kanban un sistema robusto, lasciando poco spazio a errori e fraintendimenti. L’approccio pull del Kanban lo rende ancora più solido quando si tratta di manifattura o di supply chain management. Il prelievo basato sul consumo effettivo è meno rischioso; significa che il riapprovvigionamento si basa su dati reali piuttosto che su previsioni (per loro natura mai del tutto accurate). Di conseguenza, implementare il Kanban di solito porta a riduzioni dell’inventario, e quindi a una riduzione dei costi, a un maggior spazio di stoccaggio, a una diminuzione delle scorte morte, ecc. Questo è l’obiettivo di un processo Lean.
Punti critici
Implementare un sistema Kanban adeguato comporta una serie di regole senza le quali il Kanban può rapidamente diventare inefficiente o privo di significato. Senza entrare nei dettagli e mostrare le sei Regole di Toyota, possiamo evidenziare alcuni aspetti critici per coloro che potrebbero considerare l’implementazione del Kanban.
Una delle chiavi per un buon sistema Kanban è il monitoraggio rigoroso e l’osservanza delle regole. Le schede Kanban devono essere posizionate correttamente, le azioni devono essere eseguite in modo preciso e tempestivo. Uno dei punti di forza del sistema risiede nell’automazione delle azioni: ad es. una parte difettosa viene sempre posizionata nello stesso contenitore nello stesso luogo, una scheda che segnala la necessità di riapprovvigionamento viene sempre collocata alla fine della fila del magazzino nello stesso modo, ecc. Se le azioni non vengono eseguite correttamente e alcuni passaggi vengono dimenticati o alterati, il meccanismo ben oliato può rapidamente andare storto e innescare un effetto domino. Tutto deve essere monitorato, costantemente, e gli addetti devono essere formati in modo preciso. Con l’e-kanban, questo pone molta pressione sulla precisione e sull’affidabilità del sistema IT, in particolare, sull"accuratezza nell’inventario. L’e-kanban era pensato per evitare errori manuali, ma si verificano errori nell’inserimento dei dati o bug in un sistema…
Il Kanban è inizialmente flessibile per natura, nel modo in cui può adattarsi a molte situazioni, ma una volta completamente implementato e ottimizzato per le dimensioni dei contenitori e così via, il sistema deve essere molto rigoroso. Infatti, una volta impostato e salvo nuove modifiche, il Kanban perde ogni flessibilità. Per esempio, una volta definiti, gli importi collocati nei contenitori/scatole non dovrebbero essere modificati dall’utente per adattarsi a una situazione specifica. Ciò comporta il rischio di una mancanza di adattabilità. A meno che non venga usato in un ambiente estremamente stabile, i sistemi Kanban devono essere riesaminati regolarmente poiché potrebbe essere necessaria un’ulteriore messa a punto.
Contro
Il Kanban non è adatto a ogni situazione. Come spesso accade, il diavolo è nei dettagli. Innanzitutto, la semplicità del Kanban può talvolta nascondere una notevole complessità… Due contenitori sembrano sufficientemente semplici, ma dimensionarli correttamente per garantire il loro funzionamento senza interrompere un processo produttivo o bloccare una supply chain è difficile. Utilizzando il Kanban, molte organizzazioni pensano di poter sfuggire alla necessità di prevedere la domanda che comporta un classico sistema push. In parte, ci riusciranno, ma solo fino a un certo punto. La dimensione dei contenitori, scatole, secchi o qualsiasi spazio da riempire in un sistema Kanban è in realtà il risultato di una previsione. È direttamente legata alla quantità che un’organizzazione sceglie di utilizzare come buffer o scorta di sicurezza. È una mitigazione del rischio, e quindi basata su una valutazione del rischio. Il fatto che la maggior parte delle volte tale valutazione non sia basata sui dati, ma piuttosto empirica e realizzata attraverso mesi di ottimizzazione e operazioni dicotomiche e ricalibrazioni, non la rende meno una previsione.
In particolare, si dovrebbe porre un’enfasi speciale sulla capacità di ottenere il riapprovvigionamento da fornitori e terze parti. La dimensione del contenitore può essere interpretata come una scorta di sicurezza, che a sua volta è direttamente collegata al lead time. Fondamentalmente, la domanda è la seguente: quanto dovrebbe durare un contenitore per coprire le esigenze di un processo nel lasso di tempo necessario a un fornitore per consegnare nuovi articoli? Se il fornitore è affidabile e i lead time sono costanti, la risposta è diretta. L’esperienza mostra, tuttavia, che non è sempre così. Pertanto, in situazioni in cui i fornitori non sono affidabili, o i lead time sono fluttuanti, o la qualità dei materiali utilizzati per un processo produttivo è essa stessa variabile, il Kanban può essere difficile da implementare. Il non riuscire a tenere in considerazione le fluttuazioni dei lead time potrebbe alla fine portare a mantenere buffer inutilmente grandi in ogni momento.
Lo stesso vale quando la domanda varia nel corso dell’anno, con forte stagionalità ad esempio. Anche con un sistema pull, la domanda deve essere in qualche modo gestita per evitare rotture di stock. Che si tratti della produzione o della gestione della supply chain, la dimensione dei contenitori non dovrebbe rimanere costante in tali casi. Allo stesso tempo, se i contenitori vengono continuamente rivalutati, il sistema perde gran parte del suo significato. Pertanto, una delle principali critiche che si potrebbe muovere al sistema Kanban è la mancanza di proattività e adattabilità.
Kanban diventa anche inefficiente - o molto più difficile da implementare - quando si tratta di produzione a lotti ed economie di scala, che per natura sono alquanto in contrasto con un approccio “abbastanza giusto”. Al contrario, l’idea è produrre in grandi quantità in un’unica soluzione (o acquistare di più effettuando un grande ordine a un fornitore per ottenere prezzi più bassi) per ridurre i costi. Ciò significa anche correre il rischio di produrre o accumulare troppo in previsione di una domanda che potrebbe non concretizzarsi. Assumere tali rischi può portare a grandi ricompense, mentre Kanban, in modo più stabile, potrebbe non deludere, ma potrebbe anche non essere così remunerativo.
Infine, si può sostenere che Kanban si basi su una visione molto locale, con un’ottimizzazione passo dopo passo e un’azione locale e semplice da intraprendere in risposta a un evento particolare. Trae la sua forza proprio da tale visione locale, ma allo stesso tempo Kanban rimane cieco agli effetti di rete, a una cattiva distribuzione dei flussi o delle risorse in un sistema, ecc. Sarà inoltre debole nei confronti dei rischi sistemici. Ad esempio, in alcuni business B2B, certe categorie di prodotti esistono solo se esiste uno specifico cliente. Quando detto cliente scompare, la necessità del prodotto scompare del tutto. Kanban non è semplicemente progettato per considerare tale rischio. Lo stesso vale per le problematiche relative all’obsolescenza. Questi svantaggi non disqualificano Kanban come sistema efficiente; evidenziano semplicemente che va utilizzato con la consapevolezza dei suoi limiti intrinseci.
Kanban applicato a SCM e controllo dell’inventario
Inizialmente legato esclusivamente alla produzione, Kanban ha seguito il suo metodo affine, Lean, nel campo della Supply Chain Management (SCM). Il principio rimane lo stesso: un metodo semplice e visivo per emettere un ordine d’acquisto per una quantità predefinita quando lo stock si esaurisce, al fine di minimizzare l’inventario e i rischi ad esso associati. Questo non sorprende, poiché Kanban nasce dall’osservazione dei consumatori nei supermercati. I consumatori non acquistano merci per accumularle a casa; comprano ciò di cui hanno bisogno e ritornano quando le merci sono state consumate, sapendo che ci saranno sempre più prodotti disponibili ogni volta che ne avranno bisogno. Nei supermercati stessi, gli scaffali sono organizzati per contenere una certa quantità di prodotti e niente di più; non appena iniziano a svuotarsi perché il contenuto è stato consumato, vengono riempiti nuovamente. Esistono classicamente diverse profondità standardizzate degli scaffali per tenere conto della rotazione dei prodotti. Chiunque si muova tra gli scaffali può rapidamente valutare a colpo d’occhio se è necessario un rifornimento o meno.
Ciò che è vero a livello locale per i supermercati e i punti vendita in generale può essere esteso ulteriormente. In SCM, il metodo dei 3 contenitori potrebbe essere interpretato come segue: un primo “contenitore” viene posizionato al livello del negozio o punto vendita per soddisfare la domanda iniziale, un secondo contenitore si trova a livello del magazzino (o in un punto equivalente di inventario), e un terzo è presso il fornitore. Quando il negozio esaurisce il proprio stock, segnala la necessità di un rifornimento al magazzino, che a sua volta si rivolge al fornitore. Ciò che è stato detto in precedenza riguardo alla dimensione del contenitore rimane valido: la dimensione del “contenitore” è direttamente correlata alla quantità di scorta di sicurezza che l’organizzazione è disposta a detenere e al lead time del fornitore insieme alla sua capacità di rifornire in modo affidabile. Ulteriori considerazioni possono intervenire a livello del fornitore, come il MOQ (Quantità Minima d’Ordine), poiché il fornitore potrebbe non essere disposto a rifornire se non vengono raggiunte determinate quantità, che possono essere comuni a diversi riferimenti e potrebbero non essere considerate SKU per SKU. A volte la questione si riduce al prezzo per unità. Un piccolo rifornimento potrebbe essere possibile, ma costoso.
I pro e i contro di Kanban per la SCM sono quelli menzionati in precedenza e non differiscono da quanto si potrebbe dire per la produzione. L’applicazione di Kanban solitamente riduce l’inventario (e i rischi e i costi collegati), a volte a scapito della flessibilità e introducendo una maggiore dipendenza dai fornitori e dai loro tempi di consegna. Ciò rende più difficile beneficiare degli effetti di rete o sfruttare i MOQ, i MOV (Valore Minimo d’Ordine) del fornitore o gli sconti sui prezzi.
Inoltre, utilizzando una visione piuttosto semplice dell’inventario, Kanban è cieco alle situazioni in cui l’irregolarità potrebbe essere un vantaggio. Kanban si basa sul presupposto che la produzione debba procedere senza interruzioni e che il rifornimento continui ogni volta che lo stock viene esaurito. Tuttavia, ci sono situazioni in cui l’esaurimento delle scorte può essere auspicabile per prodotti in fase terminale del loro ciclo di vita o prodotti stagionali. Esistono anche situazioni in cui fornitori inaffidabili, o meglio fornitori con tempi di consegna lunghi o irregolari, possono comportare prezzi per unità più bassi. Vendere alcuni articoli che a volte sono esauriti ma offrono alti margini può essere vantaggioso, e mantenere scorte di sicurezza (o contenitori pieni) sufficientemente elevate da non rimanere mai a secco di stock solitamente non è praticabile. Per alcuni prodotti, sfruttare il fatto che vengono prodotto in modo intermittente (ad es. fragole locali) o che sono suscettibili a fluttuazioni di mercato (ad es. produzioni legate ai prezzi di mercato mondiali) può rappresentare un enorme vantaggio per un’organizzazione. Kanban non lo consente davvero.
Tuttavia, quando la domanda è estremamente stabile, o estremamente bassa, al punto che le previsioni risultano altamente inaccurate, Kanban può essere una delle opzioni migliori disponibili. Ad esempio, nel settore della moda, alcuni piccoli punti vendita registrano volumi di vendita bassi in maniera molto irregolare. Alcuni SKU potrebbero ottenere solo un paio di vendite durante una stagione. Per questi punti vendita e per questi tipi di referenze, Kanban può essere la soluzione ideale, perché qualsiasi altra cosa risulta fallimentare.
Abbiamo già spiegato che Kanban alleggerisce la necessità di previsioni, ma non la elimina - la definizione della dimensione dei contenitori è in sé una specie di previsione. Si può quindi sostenere che siano possibili approcci misti. Le previsioni possono integrarsi con Kanban e, viceversa, è possibile integrare un pizzico di Kanban all’interno di un processo di previsione attraverso alcune euristiche per le situazioni che lo richiedono.
Il punto di vista di Lokad
La potenza di Kanban risiede nella forza di euristiche ben scelte e in invarianti imposti. Sono un’approssimazione, eppure sono robuste e immutabili. Vengono implementate con la correttezza per design e con la limitazione del rischio in mente, cosa che spesso è difficile da superare. Si potrebbe dire che esista una “valle inquietante” tra Kanban e gli altri metodi. Kanban può sicuramente essere superato, ma farlo richiede molto impegno. L’uso di semplici strumenti di previsione (i classici modelli matematici e simili) o di soluzioni AI poco sviluppate - soprattutto per alcuni tipi di dati - di solito non risolve il problema. In molte situazioni, il metodo di previsione deve possedere una reale superiorità per superare i benefici di Kanban e dei suoi semplici contenitori, scorte di sicurezza e schede.
Tuttavia, questo metodo semplice rimane statico, con una visione locale, poco sofisticato e cieco a determinate classi di rischi (e opportunità). Non sarà utile quando si tratta di problematiche di rete o di valutare i vantaggi delle irregolarità. In Lokad, crediamo che sia possibile ottenere il meglio da entrambi i mondi e andare oltre Kanban sfruttando, quando la situazione lo richiede, euristiche intelligenti ancorate alla realtà del business. Questa è una delle idee alla base delle liste prioritarie che cerchiamo di implementare con il Quantitative Supply Chain: mantenere le cose semplici e visive per l’utente, fornendo al contempo una soluzione evolutiva, misurata, ponderata e rivista che sia sempre guidata dai dati.