Quantitative Prinzipien für supply chain (Vorlesungen 1.6 Zusammenfassung)
Sinnvolle supply chain-Optimierung ist das Beherrschen der Optionalität, mit der man konfrontiert wird als Folge der inhärenten Variabilität im Warenfluss, und dieses Beherrschen ist der quantitativen Analyse zugewandt. Supply chain Probleme sind ebenso quantitativ, aber wicked und gelegentlich geradezu seltsam, was im Widerspruch zu herkömmlichen Analysen steht. Die Anwendung quantitativer Prinzipien sowohl in der Beobachtungs- als auch in der Optimierungsphase kann Fachleuten helfen, viele obskure, aber dennoch vorhersehbare Fallstricke in der supply chain zu vermeiden.
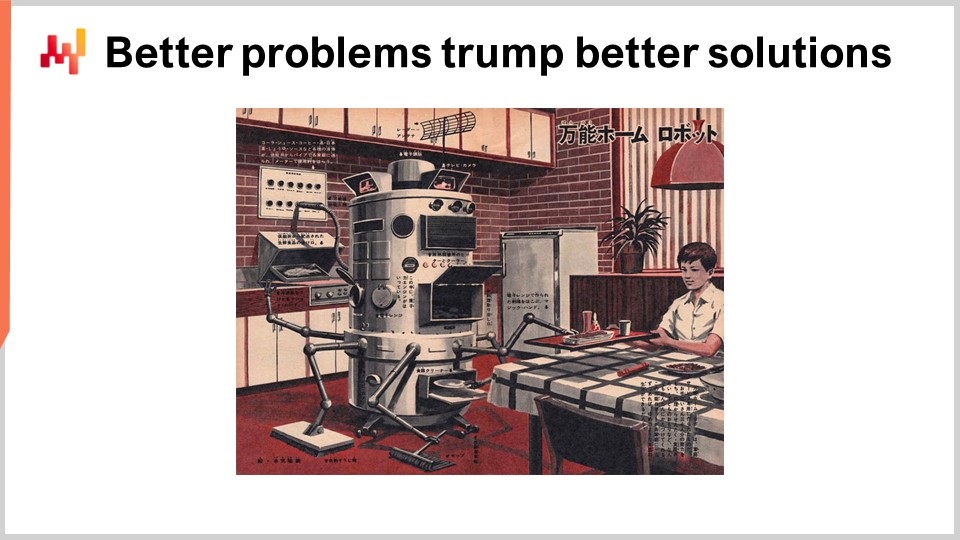
Die Vorlesung ansehen
Beobachtungsprinzipien
Übergreifend sind die Arten von Entscheidungen und Einschränkungen, mit denen Supply Chain-Praktiker kämpfen, stets quantitativ – wie beispielsweise Lagerauffüllung Werte, Service Level-Ziele, MOQs, usw. Allerdings entziehen sich supply chains selbst einer direkten Beobachtung. Man kann nicht einen Schnappschuss der gesamten supply chain machen, wie man es bei einem einzelnen mechanischen Gerät tun könnte, obwohl beide argumentativ CapEx sind, beide aus vielen beobachtbaren physischen Unterteilen bestehen und beide (in der Regel) zu einem physischen Ergebnis führen.
Trotz dieser Einschränkung sind supply chains nicht feindlich gegenüber quantitativer Analyse. Im Gegenteil, eine quantitative Analyse der supply chain offenbart mehrere lehrreiche, wenn auch debattierbar kontraintuitive Beobachtungen.
Supply chain Probleme sind nicht normal verteilt
Vielleicht enttäuschenderweise neigen supply chain Probleme nicht dazu, normalverteilt zu sein, was zu vielen organisatorischen Schwierigkeiten führt, denen man bei ihrem Optimierungsversuch begegnet. Bei einer Normalverteilung können eine große Anzahl kleiner, unabhängiger Faktoren einen Wert in beide Richtungen beeinflussen (z. B. mehr oder weniger, nach oben oder nach unten). Mit anderen Worten: Eine Normalverteilung resultiert aus vielen kleinen zufälligen Veränderungen, die einen Wert erhöhen oder verringern können1.
Supply chain Probleme entstehen jedoch oft aus einer kleinen Anzahl gravierender, systemischer Faktoren statt aus einer Vielzahl kleiner, unabhängiger Faktoren. Diese Faktoren umfassen:
-
Nachfragevariabilität: Die Nachfrage nach Produkten ist oft sehr schwankend und kann von einer Vielzahl von Faktoren wie saisonalen Trends, wirtschaftlichen Bedingungen und Marketingkampagnen beeinflusst werden. Diese Variabilität kann zu Problemen wie Fehlbeständen oder Überbeständen führen.
-
Lieferantenzuverlässigkeit: Die Leistung von Lieferanten kann einen erheblichen Einfluss auf die supply chain haben, und Schwankungen in der Zuverlässigkeit von Lieferanten können zu Problemen wie verzögerten Lieferungen und Qualitätsproblemen führen.
-
Logistische Störungen: Probleme wie Transportverzögerungen, Zollverzögerungen oder Naturkatastrophen können erhebliche Störungen in der supply chain verursachen.
Die oben genannten Probleme sind keine trivialen Bedrohungen für die Kontinuität (und Optimierung) der supply chain. Vielmehr handelt es sich um unverhältnismäßig große, boshafte Probleme, die dramatisch überproportionale Auswirkungen haben können.
Darüber hinaus weisen supply chain Probleme häufig ein gewisses Maß an Schiefe auf, was bedeutet, dass es in der Regel nur wenige Hauptprobleme gibt, die einen großen Anteil der Probleme verursachen, anstatt einer symmetrischen Verteilung der Probleme um einen vorhersehbaren Durchschnitt. In vielen Fällen zeigen diese Probleme auch eine „Long-Tail“-Verteilung – d. h. eine Vielzahl unterschiedlicher Probleme treten jeweils selten auf.
Die wechselseitigen Abhängigkeiten und Feedback-Schleifen, die in supply chains innewohnen (zum Beispiel, wie der aktuelle Lagerbestand zukünftige Bestellentscheidungen beeinflusst), bewirken ebenfalls, dass das Auftreten von Problemen von der Normalverteilung abweicht. Solche nichtlinearen, komplexen Systeme werden genauer durch andere statistische Modelle beschrieben (im Folgenden näher erläutert).
Die umgekehrte Beziehung zwischen Häufigkeit und Rang
Ein besseres quantitatives Modell zur Untersuchung von supply chain Problemen (und Werten im Allgemeinen) ist das Zipf’sche Gesetz. Einfach ausgedrückt, gibt es zwei Hauptelemente des Zipf’schen Gesetzes:
-
Einige wenige Werte in einem Datensatz treten sehr häufig auf, während die meisten nur selten vorkommen.
-
Die Häufigkeit eines Wertes ist umgekehrt proportional zu seinem Rang.
Betrachten Sie die Worthäufigkeit in einem Lehrbuch. Das am häufigsten vorkommende Wort in einem beliebigen Buch (sofern es in einer Sprache geschrieben ist, die ein bestimmtes/unbestimmtes Artikelsystem verwendet) wird wahrscheinlich the sein. Das zweithäufigste Wort könnte of sein, und seine Häufigkeit wird (ungefähr) halb so hoch sein wie die von the. Dieser Trend wird in den Ranglisten fortgesetzt2.
Ein relevantes Beispiel aus dem Einzelhandel ist die häufige Erkenntnis, dass eine kleine Anzahl von Artikeln im Katalog einen großen Teil des Umsatzes ausmacht, während ein Long-Tail anderer Artikel selten verkauft wird. Dieses Muster – einige „Erfolge“ und viele „Flops“ – entspricht der Zipf-Verteilung. Dies ist ein ähnliches Konzept wie das Pareto-Prinzip, das besagt, dass etwa 80% der Effekte von 20% der Ursachen stammen. Die hier beschriebene Asymmetrie ist in der Tat das treibende Prinzip hinter Bestandskontroll-systemen wie ABC und ABC-XYZ. Allerdings gibt es einige wesentliche Unterschiede zwischen der Pareto- und der Zipf-Verteilung, die es wert sind, genauer betrachtet zu werden.
-
Pareto-Verteilung: Stellen Sie sich ein Online-Einzelhandelsunternehmen mit einem umfangreichen Katalog vor. Die supply chain Abteilung könnte feststellen, dass 80% des Umsatzes des Unternehmens nur von 20% des Sortiments generiert werden, was darauf hindeutet, dass die Ressourcen besser darauf ausgerichtet sein sollten, den Lagerbestand dieser beliebten Artikel zu halten. Obwohl dies ein nützlicher allgemeiner Richtwert sein mag, fehlt die Auflösung, die die Abteilung benötigt, um die Verkaufsdaten richtig zu analysieren (über die bloße Identifizierung hinaus, welche SKUs den meisten Umsatz generiert haben).
-
Zipf-Verteilung: Würde dieselbe supply chain Abteilung eine Zipf-Verteilung anwenden, so käme eine interessante zusätzliche Detailebene in die Analyse ein. Durch die Untersuchung aller Verkäufe und ihrer Häufigkeiten könnte das Team Muster erkennen, die einer Pareto-Verteilung entgehen. Zum Beispiel könnten sie feststellen, dass, während Elektronik und Haushaltsgeräte tatsächlich die besten Performer sind, es auch andere Produktkategorien gibt, wie Bücher oder Kleidung, die zusammen einen erheblichen Anteil am Gesamtumsatz beitragen – obwohl sie für sich genommen keine signifikanten Margenlieferanten sind. Eine Zipf-Verteilung würde auch potenziell interessante Beziehungen im Katalog aufzeigen, die es wert sein könnten, untersucht zu werden, wie zum Beispiel warum das drittbeliebteste Produkt etwa ein Drittel des Umsatzes des meistverkauften Produkts beiträgt, obwohl es austauschbar ist und vergleichbare Werbeausgaben erhält.
Die Tyrannei der kleinen Zahlen
Eine zipf’sche Verteilung wird vielleicht am deutlichsten, wenn es darum geht, explizite supply chain Probleme zu quantifizieren, insbesondere in Situationen, in denen ein unverhältnismäßig negativer Einfluss nur wenigen Ursachen zuzuschreiben ist.
Betrachten Sie die negativen Auswirkungen, wenn ein B2B-Unternehmen seinen größten Lieferanten verliert, insbesondere wenn dieser Lieferant doppelt so viel beiträgt wie der zweitgrößte Lieferant des B2B-Unternehmens. Ebenso würde der Verlust der beiden größten Kunden zu einem außergewöhnlichen Umsatzrückgang führen, wenn man bedenkt, dass der drittgrößte Kunde etwa ein Drittel des Volumens des größten Kunden abnimmt.
Wichtig ist, dass, wenn supply chain Probleme normalverteilt wären, sie vorhersehbarer wären und standardmäßige Abmilderungsstrategien ausreichen würden. Die Tatsache, dass jedoch wenige signifikante Probleme (wie hier beschrieben) den Großteil der Störungen verursachen können, bedeutet, dass Fachleute ihre Ressourcen darauf konzentrieren müssen, diese hochwirksamen Probleme zu identifizieren und zu mindern. Dies erfordert einen strategischeren, proaktiven und ganzheitlichen Ansatz im supply chain Management.
Optimierungsprinzipien
Nachdem man das von Vorurteilen durchzogene Terrain der menschlichen Beobachtung umschifft hat, ist der Schritt hin zur supply chain Optimierung der Reise ebenso anfällig für Hindernisse. Supply chain Optimierungsinitiativen sind oft fehlerbehaftet, nicht nur in Bezug auf Software (denken Sie an ERPs), sondern auch an der Wetware (denken Sie an vererbte Weisheit).
Softwareprobleme, wie Heisenbugs, werden üblicherweise durch wiederholte Anwendungen des Programms behoben. Wetware-Fehler hingegen haben die unheimliche Eigenschaft, weitgehend fest einprogrammiert zu sein, was zusätzliche Deprogrammierungsmaßnahmen erfordert.
Verborgene Weisheit in gealterten supply chains
Supply chains, die seit mehreren Jahrzehnten bestehen, haben mindestens ein grundlegendes Maß an Weisheit angesammelt. Es ist im ersten Moment schwer vorstellbar, auf ein Unternehmen zu stoßen, das seit 20 oder mehr Jahren funktioniert und nicht zumindest zufällig auf einige nützliche Strategien oder Faustregeln gestoßen ist. Als solche verkörpern alle bestehenden Praktiken und betrieblichen Normen eine Form von Quasi-Optimalität, insofern sie das Unternehmen in die richtige Richtung (bezüglich der Gesamtnettoprofitabilität) lenken können, jedoch mit erheblichen Unvollkommenheiten3.
Ähnlich wie ein Fluss, der sich seinen Weg durch ein Gebirge bahnt, neigt sich eine solche Weisheit dazu, sich an eine einzige treibende Kraft zu binden. Wie die Schwerkraft einen Fluss durch Sedimente zieht, werden gealterte supply chains oft mit dem Ziel einer einzigen Kennzahl (KPI) verfolgt, wie etwa der Erhöhung des Service Levels oder der Reduktion von Totbeständen. Obwohl diese Ziele sinnvoll erscheinen mögen, reduzieren sie implizit die supply chain auf ein diskretes Bündel von voneinander losgelösten Elementen, die in Isolation angepasst werden können.
Dies führt im Wesentlichen zu einer Booleschen Mentalität, in der die supply chain Optimierung naiv in binären Begriffen ausgedrückt wird. Betrachten Sie Folgendes:
-
Wenn sich die Service Levels verbessern, muss die supply chain verbessert worden sein. Dies übersieht natürlich die Tatsache, dass eine Steigerung des Service Levels in der Regel eine generelle Erhöhung der Lagerbestände erfordert (vorausgesetzt, es handelt sich nicht um eine quantitative supply chain Optimierung). Eine Erhöhung der Lagerbestände führt wiederum in der Regel zu erhöhten Totbeständen, was zu einem verringerten Nettogewinn führt.
-
Wenn sich die Totbestände verringern, muss die supply chain verbessert worden sein. Ähnlich ignoriert diese einseitige Sicht auf Optimierung den Einfluss, den eine Reduktion des Lagerbestands wahrscheinlich auf Service- und Kundenzufriedenheitsziele haben wird, und beeinflusst so Käufe (und oft die Kundenbindung) negativ.
Supply chains dieser Art, die im Alter sind, besitzen eine eindimensionale Quasi-Optimalität, die, wie ein wenig Wissen, eine äußerst gefährliche Sache sein kann. Dass die supply chains standardmäßig in Richtung eines Quasi-Erfolgs tendieren, trägt wahrscheinlich zu ihrer Langlebigkeit bei und verfestigt suboptimale Praktiken.
Große, eindimensionale Verbesserungen in gealterten supply chains stehen häufig in engem Zusammenhang mit Misserfolg – nicht wegen mangelnden Engagements, sondern vielmehr aufgrund fehlender Berücksichtigung der gewaltigen, systemischen und miteinander verflochtenen Komplexität, die in modern supply chains mitschwingt.
Der Irrtum der lokalen Optimierung
Grundlegend für die Optimierung eines so weitläufigen und voneinander abhängigen Systems wie der supply chain ist das Verständnis, dass lokale Optimierung Probleme nicht löst, sondern lediglich verlagert. Wie im vorherigen Abschnitt dargestellt, führt die Optimierung eines lokalen (im Sinne von “in Isolation”) supply chain Problems typischerweise zu einem Ungleichgewicht und erzeugt einen unerwünschten Nebeneffekt an anderer Stelle in der supply chain.
Ähnlich wie das Einbauen einer Solid State Drive (SSD) in einen 30 Jahre alten Computer den gesamten Speicher (oder die Leistung)4 nicht verbessert, ist die Optimierung eines supply chain Netzwerks (oder supply chain Systems) ein end-to-end, systemweiter Prozess.
Dieses Konzept wird in der Einzelhandelsbranche unübersehbar. In einem Einzelhandelsnetzwerk, das aus mehreren Filialen besteht, könnte die Intuition dazu verleiten, die Lagerbestände in jeder Filiale zu optimieren (vielleicht sogar manuell). Man könnte sogar bevorzugt Ressourcen der meistverkauften Filiale im Netzwerk zuweisen.
Ein solcher Ansatz berücksichtigt jedoch nicht das breitere Netzwerk von Vertriebszentren, die diese Filialen bedienen, sowie die nachgelagerten Konsequenzen einer Politik, die Lagerbestände zuweist, ohne die Auswirkungen auf andere Filialen zu berücksichtigen. Eine enge Fokussierung auf eine einzige Filiale mag deren Leistung verbessern, könnte jedoch für die anderen nachteilig sein.
Zudem wird das zentrale Anliegen einer Einzelhandels-Lagerbestandszuweisungsmission verfehlt, nämlich die Identifizierung, wo eine bestimmte Einheit/SKU am dringendsten benötigt wird, um die Gesamtleistung des Systems zu optimieren.
Folglich ist die Optimierung der Einzelhandels-Lagerbestandsallokation ein Problem, das nur auf Systemebene sinnvoll ist, was die Bedeutung einer ganzheitlichen, systemweiten Perspektive unterstreicht5.
Probleme neu definieren für überlegene Ergebnisse
Die klassische Ausbildung (und Verkäuferpräsentationen) stellen Probleme als am besten durch eine überlegene Lösung gelöst dar. Auf den ersten Blick erscheint dies völlig vernünftig, da der kürzeste Weg zwischen zwei Punkten tatsächlich eine gerade Linie ist. Dieser erfreulich lineare Ansatz neigt jedoch dazu, Probleme zu vereinfachen und geht im Grunde davon aus, dass man versuchen sollte, diese beiden Punkte überhaupt zu verbinden.
Angesichts der verschiedenen Kosten, die bei dem Versuch, eine supply chain zu optimieren, entstehen, ist dies keine triviale philosophische Beobachtung. Sowohl in der Theorie als auch in der Praxis übertrifft ein besseres Verständnis der eigenen Probleme (langfristig) eine großartige Lösung für ein schlecht verstandenes Problem (kurzfristig).
Ein Lehrbuchbeispiel ist das Problem der Nachfrageprognose. supply chain Anbieter und Akademiker gleichermaßen könnten ein fortgeschrittenes time series Prognosewerkzeug als ideale Lösung zur Quantifizierung der Nachfrage (und damit zur Festlegung der Lagerbestände) anpreisen. Auf den ersten Blick scheint dies intuitiv: Wenn ein Unternehmen die Nachfrage nicht genau vorhersagen kann, ist bessere Nachfrageprognose-Software angebracht, und die beiden entfernten Punkte werden durch eine (ziemlich) gerade Linie verbunden6.
Dies ist eine übermäßig lineare Denkweise und möglicherweise völlig orthogonal zum eigentlichen supply chain Problem von Interesse: die Entdeckung dessen, was tatsächlich die Schwierigkeit der Nachfrageprognose verursacht. Es ist völlig denkbar, dass andere zugrunde liegende Probleme, wie logistische Ineffizienzen, unzuverlässige Lieferanten oder fehlerhafte Einzelhandelsbestandszuteilungsrichtlinien, die Kräfte des Wandels darstellen.
Die Neudefinition der eigenen Probleme, anstatt bis zur supply chain roten Ampel zu rasen, kann supply chain Optimierungen richtig ausrichten und Bandbreite (und Ressourcen) von kurzfristigen Schnelllösungen umverteilen.
Notizen
-
Größe ist ein klassisches Beispiel für eine Normalverteilung (oder Gaußsche Verteilung). Dies liegt daran, dass die Größe von vielen unabhängigen genetischen und umweltbedingten Faktoren beeinflusst wird, was eine symmetrische Glockenkurve um einen Durchschnittswert herum erzeugt. Gemäß dem Zentralen Grenzwertsatz neigt die Summe vieler unabhängiger und identisch verteilter Zufallsvariablen dazu, eine Normalverteilung zu bilden. Dies führt dazu, dass die meisten Individuen sich um die durchschnittliche Größe gruppieren, während an den Extremen (sehr klein oder sehr groß) weniger Individuen vorhanden sind, was zu einer typischen Glockenkurve führt. ↩︎
-
Im Gegensatz zum vorherigen Beispiel der Größe (ein Phänomen, das von einer Vielzahl unabhängiger genetischer und epigenetischer Kräfte beeinflusst wird), gilt eine Zipf-Verteilung für rangierte Daten (wie Stadtbevölkerungen oder Wortfrequenzen), bei denen Rang und Häufigkeit umgekehrt proportional zueinander stehen. Da die Größe kein vergleichendes oder rangiertes Maß ist, folgt sie keiner Zipf-Verteilung. Zum Beispiel ist bei einer typischen Zusammenkunft die größte Person in einem Raum nicht doppelt so groß wie die zweitgrößte, noch um eine Größenordnung größer als die zehnte. ↩︎
-
Entgegen dem Schein diskreditiert die quantitative supply chain Theorie weder den Wert menschlicher Weisheit, noch mindert sie diesen. In der Tat ist eine solche Philosophie völlig agnostisch gegenüber der Möglichkeit eines individuellen Visionärs, der – wie Warren Buffett – die Verbrauchernachfrage mit unheimlicher Präzision vorhersagen könnte. Selbst wenn solche Randfälle alltäglich wären, würde dies die übergeordneten Kritiken an einem solchen Ansatz nicht entkräften: nämlich, dass Bauchgefühl nicht skaliert und aller Wahrscheinlichkeit nach nicht die beste Anwendung des Geistes hinter dem Bauch darstellt. Angesichts dieser Einschränkungen und der Tatsache, dass solche Menschen das supply chain Äquivalent zu Promethium sind, ist dies eine rein akademische Angelegenheit, wenn es um die Optimierung groß angelegter, geografisch verteilter supply chain Netzwerke geht. ↩︎
-
Ein 30 Jahre alter Computer verfügt fast sicher über Hardware und ein Betriebssystem, die mit modernen SSDs nicht kompatibel sind. Selbst wenn er die SSD irgendwie akzeptiert, würden die veraltete CPU, der RAM und die Busgeschwindigkeiten die Leistungssteigerungen stark begrenzen. Außerdem könnte das Betriebssystem SSD-Funktionen wie TRIM nicht unterstützen, was die Lebensdauer der SSD verringert. Software- und Hardwareinkompatibilitäten könnten weitere Probleme verursachen, wie Fehlfunktionen, Datenkorruption oder vollständige Nicht-Funktionalität. Zusammengefasst: Versucht das nicht zu Hause. ↩︎
-
Es ist wichtig zu beachten, dass dieses Prinzip nicht nur in einem streng geografischen Sinn gilt, sondern auch logisch innerhalb und entlang der supply chain selbst. Ein gutes Beispiel hierfür ist der Lebenszyklus von Elektronikgeräten. Geräte – wie Smartphones – existieren in verschiedenen Intervallen eines vierphasigen Zyklus: Einführung, Wachstum, Reife und Rückgang. Der Versuch, eine einzelne Phase isoliert zu optimieren, würde dem gesamten Lebenszyklus des Produkts zum Nachteil gereichen, zum Beispiel wenn man versucht, die Reife-Phase zu optimieren (in der sich der Verkauf des Geräts stabilisiert), ohne die nachgelagerten Effekte auf die Rückgangsphase zu berücksichtigen (in der etwaige Fehler in der Bestandsverwaltung, die zu Beginn des Lebenszyklus gemacht wurden, am deutlichsten zutage treten). ↩︎
-
Dieses Konzept wird, ziemlich wörtlich, in der Vorlesung am Beispiel der Routenoptimierung demonstriert. Zugegeben, im Kontext verwendet Vermorel die Routenoptimierung als Beispiel für Muster in der supply chain, jedoch funktioniert sie ebenso gut als Metapher für die Neudefinition von Problemen. Kurz gesagt, Routenoptimierung beschränkt sich nicht auf eine einzelne Route, sondern erfordert ein systemweites Verständnis jeder Route und warum die Routen schwer zu optimieren sind. Zum Beispiel: Warum verschieben sich manche Liefer-Hotspots im Laufe des Jahres? Warum gibt es eine Saisonalität bei den Hauptverkehrszeiten in Paris? Indem man bessere Fragen stellt, kann man die wahren Probleme von Interesse genauer bestimmen, bevor man versucht, sie anzugehen. ↩︎