Kanban (Gestion des stocks)
The Kanban method (billboard in Japanese), like Lean Manufacturing takes its roots from the Japanese automotive manufacturer Toyota. It was implemented to improve manufacturing efficiency and reduce waste by providing a simple and visual material replenishment process, so that every step of the production process would get just enough in a timely manner to operate smoothly, without stockpiling raw materials or components. Basically, each time a certain quantity of material is consumed - immediately visible as an empty box or an empty shelf -, a visual signal (typically a card) is sent to trigger replenishment for the same quantity. From here, the Kanban system gained influence in several fields, in particular in software development with the Agile management philosophy, or in supply chain management, as a simple method to avoid overstocks.
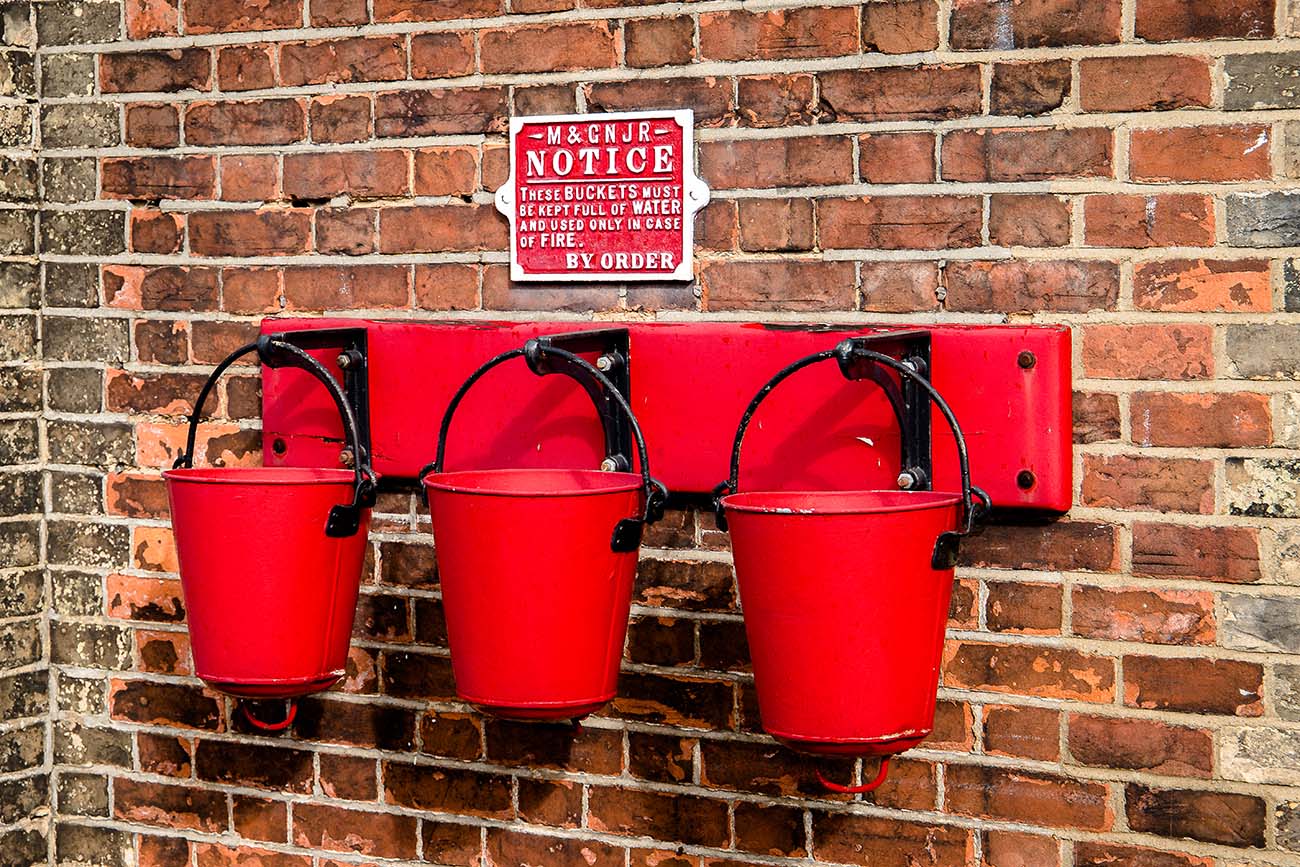
Origines du Kanban et évolution en dehors de la fabrication
Originaire des années 40/50, dans un environnement d’après-guerre avec pratiquement aucun ordinateur ou digitalisation disponible, le Kanban a eu le grand mérite de rationaliser le monde de la fabrication grâce à un système simple et pourtant élégant, avec peu plus que des cartes en papier et des boîtes ou bacs.
Dans leurs efforts pour réduire le gaspillage - et donc l’excès de stocks inutiles sur les ateliers ou en magasin - les ingénieurs de Toyota ont conçu un système dans lequel le réapprovisionnement était directement lié à la consommation réelle. Ils ont choisi d’adopter un système pull plutôt qu’un système push. Il existe une dichotomie fondamentale entre les deux. Traditionnellement, la production de biens se base sur l’anticipation de la demande (généralement matérialisée par des prévisions de demande) ; les biens sont produits à l’avance et ensuite poussés sur le marché. Avec le pull, le système est orienté par la demande et les biens sont fabriqués sur commande. La production et le réapprovisionnement n’interviennent que lorsque cela est nécessaire et non pas en anticipation de la demande.
Il existe plusieurs façons de mettre en place un système Kanban. Les expressions les plus simples sont le système à 2 bacs ou 3 bacs. Par exemple, un entrepôt utilisant un système à 2 bacs afficherait des étagères dimensionnées pour accueillir deux boîtes pleines d’articles, chaque boîte contenant une carte Kanban, comportant généralement des informations sur l’article (référence, code-barres, quantité, etc.). Chaque fois qu’une boîte est vide, celle-ci est mise de côté pour être réutilisée ultérieurement et la carte Kanban est déplacée vers un emplacement visible - typiquement à la fin de la rangée, sur une table spéciale ou dans un conteneur. Pendant que la deuxième boîte est utilisée, les cartes Kanban affichées sont récupérées par un préparateur qui va rapporter une boîte pleine des magasins et remplacer la carte Kanban à l’intérieur. Idéalement, lorsque le préparateur apporte le réapprovisionnement, l’autre boîte n’est pas encore totalement utilisée, mais presque. L’idée est simple : il y a une boîte principale et une de réserve, quand la boîte de réserve commence à être utilisée, il est temps de réapprovisionner la principale, et ainsi de suite. En réalité, la boîte de réserve n’est rien d’autre qu’un stock de sécurité.
Dans un système à 3 bacs mis en place dans une usine, un bac/boîte de matériaux est placé sur l’atelier pour être traité pour la production, un bac est situé au niveau du magasin de l’usine, et un autre dans les locaux du fournisseur. Lorsque le contenu du premier bac a été utilisé par le processus de production, un signal est immédiatement envoyé au magasin pour appeler le contenu du bac plein stocké dans le magasin. À son tour, le magasin de l’usine, maintenant en possession d’un bac vide, fait appel au contenu du troisième bac détenu par le fournisseur, qui le reconstitue ensuite. Le stock n’arrive que lorsqu’il est consommé et épuisé. Un bac vide crée un déclencheur Kanban pour commander l’envoi de nouveaux matériaux dans une quantité prédéfinie. Encore une fois, aucun stock inutile n’est détenu au-delà du bac au niveau du magasin de l’usine - un tampon ou stock de sécurité - et le processus repose sur le remplacement fluide des bacs et sur la capacité du fournisseur à traiter les commandes de réapprovisionnement sans retards imprévus, c’est-à-dire, pas plus que le temps nécessaire pour vider un bac.
Tout comme le concept Lean lui-même, le Kanban, avec cette idée de cartes ou de signaux apportant de la visibilité tout au long du cycle de production et évitant les accumulations inutiles, a prospéré bien au-delà du domaine de la fabrication. Il a été largement adopté dans le développement logiciel ou le marketing comme une méthode de gestion de workflow pour matérialiser des étapes logiques. Il peut être aussi simple que la présentation d’un tableau des tâches à trois colonnes (À faire / En cours / Terminé), avec des cartes mettant en évidence les parties du projet à mettre en œuvre et à attribuer aux membres de l’équipe. Des outils comme Trello peuvent fournir des systèmes Kanban utiles et ergonomiques pour la gestion de projet.
Le développement logiciel a affiné le processus grâce à la gestion Agile. Un tableau afficherait des compartiments tels que Build / Test / Complete. Une liste de tâches priorisées est établie, comme des fonctionnalités à développer en fonction des retours des utilisateurs ; tout développeur peut prendre une carte de cette liste pour développer une fonctionnalité particulière ; une fois développée, cette fonctionnalité entre ensuite dans une phase de test avant d’être publiée. De plus, chaque compartiment est assorti d’une limite de travail en cours conçue pour s’adapter à la capacité de l’équipe : concrètement, un nombre maximum de cartes peut être placé dans un compartiment. L’avantage d’un tel tableau est la visualisation aisée pour l’ensemble de l’équipe des tâches à effectuer, l’identification rapide des goulets d’étranglement potentiels créés (par exemple, l’accumulation de cartes dans le compartiment Testing) et la capacité de suivre l’efficacité du workflow (combien de cartes sont traitées, à quelle vitesse passent-elles d’une étape à l’autre, etc.).
Avantages et inconvénients
Avantages
Magnifique dans sa simplicité et son design, le Kanban présente de nombreux avantages qui peuvent expliquer pourquoi la méthode s’est tellement répandue. Tout d’abord, un tel système est facile à comprendre et à mettre en œuvre - du moins une version simple du Kanban le serait - gagnant ainsi l’adhésion tant de la part de la direction que des équipes, et rendant la gestion du changement moins problématique. Il est également flexible et polyvalent par nature et peut facilement s’adapter aux spécificités d’une entreprise ou être compatible avec des processus déjà en place. Il appartient à chaque entreprise de définir ses bacs/compartiments et les étapes logiques qui font sens au sein de l’organisation. Des analyses simples et des rapports peuvent à leur tour être produits à partir d’un système Kanban pour analyser l’efficacité du système ou ses lacunes concernant une étape ou une autre.
Une des principales raisons pour lesquelles le Kanban est si facile à comprendre est son utilisation de signaux visuels : une carte, un espace vide, ou une boîte. Dans un système Kanban idéal, tout est conçu pour que les choses soient évidentes. Des boîtes vides sont placées dans des emplacements conspicues, des tables de taille spécifique peuvent être aménagées pour exposer des articles défectueux afin qu’une alerte soit déclenchée lorsque la table est pleine et qu’aucun autre article ne puisse y être placé, etc. Les cartes sont généralement de couleurs vives et utilisent de grandes polices ; elles peuvent également contenir des informations additionnelles telles que des recettes ou des séries d’actions à accomplir pour réunir toutes les informations simples et pertinentes en un seul endroit. L’idée principale est de pouvoir évaluer une situation d’un seul coup d’œil (besoin de réapprovisionnement, goulet d’étranglement, accumulation d’articles défectueux, etc.) et de prendre les mesures appropriées de manière très routinière et automatique, presque sans y penser.
De plus, en s’appuyant sur des indices visuels simples tels que les cartes, le Kanban n’a pas besoin de l’informatique pour fonctionner. De nos jours, il existe des versions digitales du Kanban (e-Kanban), avec des cartes dématérialisées, directement intégrées dans les ERPs, etc. Elles présentent leurs avantages, et peuvent réduire certaines erreurs manuelles, mais l’une des grandes forces du Kanban est qu’il a été conçu pour fonctionner dans un monde sans ordinateurs. Une organisation peut mettre en place le Kanban sans aucune dépendance à l’informatique et pour des travailleurs n’ayant pas accès aux ordinateurs - et donc sans formation pour utiliser des terminaux et autres.
La manière dont le Kanban est conçu, avec des signaux conspicues appelant toujours à la même action immédiate de manière répétitive et non ambiguë, en fait un système en temps réel, d’ailleurs encore plus s’il n’y a pas d’informatique impliquée. Une fois le système en place, les actions sont automatisées et peu de communication est nécessaire au sein de l’équipe. Cela mérite d’être mentionné, car presque toutes les autres alternatives introduisent des délais liés à la prise de décision (étapes de validation, autorisation, etc.).
Ces caractéristiques font du Kanban un système robuste, laissant peu de place aux erreurs et aux mauvaises interprétations. L’approche pull du Kanban le rend encore plus solide lorsqu’il s’agit de fabrication ou de gestion de la supply chain. Se baser sur la consommation réelle est moins risqué ; cela signifie que le réapprovisionnement est fondé sur des faits plutôt que sur des prévisions (par nature jamais totalement précises). Par conséquent, la mise en place du Kanban conduit généralement à une réduction des stocks, et donc à une diminution des coûts, à des gains d’espace de stockage, à une réduction des stocks dormants, etc. Tel est l’objectif d’un processus Lean.
Points sensibles
La mise en place d’un système Kanban adéquat s’accompagne d’un certain ensemble de règles sans lesquelles le Kanban peut rapidement devenir inefficace ou vide de sens. Sans entrer dans les détails et exposer les six règles de Toyota, nous pouvons souligner quelques mises en garde pour ceux qui envisageraient de mettre en place le Kanban.
L’une des clés d’un bon système Kanban est la surveillance stricte et le respect des règles. Les cartes Kanban doivent être placées correctement, les actions doivent être entreprises de manière précise et opportune. L’un des points forts du système réside dans l’automatisation des actions : par exemple, une pièce défectueuse est toujours placée dans le même conteneur, au même endroit, une carte signalant un besoin de réapprovisionnement est toujours placée à la fin de la rangée de l’entrepôt de la même manière, etc. Si les actions ne sont pas correctement exécutées et que certaines étapes sont oubliées ou modifiées, le mécanisme bien huilé peut rapidement dérailler et un effet domino peut être déclenché. Tout doit être surveillé en permanence et les opérateurs doivent être formés avec précision. Avec l’e-kanban, cela exerce une forte pression sur la précision des prévisions et la fiabilité du système informatique, en particulier, sur la fiabilité des stocks. L’e-kanban était destiné à éviter les erreurs manuelles, mais des erreurs lors de la saisie de données ou des bugs dans un système se produisent…
Le Kanban est initialement flexible par nature dans sa capacité à s’adapter à de nombreuses situations, mais une fois entièrement mis en œuvre et ajusté pour la dimension des bacs, etc., le système se veut très strict. En effet, une fois implémenté et sauf remise en question, le Kanban perd toute flexibilité. Par exemple, une fois défini, les quantités placées dans les bacs/boîtes ne sont pas censées être modifiées par l’utilisateur pour s’adapter à une situation spécifique. Cela pose le risque d’un manque d’adaptabilité. Sauf en environnement extrêmement stable, les systèmes Kanban doivent être réévalués régulièrement car des ajustements supplémentaires pourraient être nécessaires.
Inconvénients
Le Kanban ne convient pas à toutes les situations non plus. Comme souvent, le diable est dans les détails. Tout d’abord, la simplicité du Kanban peut parfois masquer une grande complexité cachée… Deux bacs semblent suffisamment simples, mais les dimensionner correctement afin de s’assurer qu’ils fonctionnent sans heurts sans stopper un processus de production ou obstruer une supply chain est difficile. En utilisant le Kanban, de nombreuses organisations pensent qu’elles pourront échapper à la nécessité de prévoir la demande qui accompagne un système push classique. En partie, c’est le cas, mais seulement dans une certaine mesure. La taille des bacs, boîtes, compartiments, ou tout espace à remplir dans un système Kanban est en fait le fruit d’une prévision. Elle est directement liée à la quantité qu’une organisation choisit d’utiliser comme tampon ou stock de sécurité. C’est une atténuation des risques, et donc fondée sur une évaluation des risques. Le fait que, dans la plupart des cas, cette évaluation ne soit pas basée sur les données, mais plutôt empirique et réalisée au travers de mois d’ajustements et d’opérations par dichotomie et réajustements, ne la rend pas moins prévisionnelle.
En particulier, une attention particulière doit être portée à la capacité à obtenir un réapprovisionnement de la part des fournisseurs et des tiers. La taille du bac peut être interprétée comme un stock de sécurité, qui à son tour est directement lié au délai d’approvisionnement. Fondamentalement, la question est la suivante : combien de temps un bac devrait-il durer pour couvrir les besoins d’un processus pendant le temps nécessaire à un fournisseur pour livrer de nouveaux articles ? Si le fournisseur est fiable et que les délais sont cohérents, la réponse est simple. L’expérience montre cependant que ce n’est pas toujours le cas. Par conséquent, dans les situations où les fournisseurs ne sont pas fiables, ou que les délais fluctuent, ou que la qualité des matériaux utilisés pour un processus de production fluctue elle-même, le Kanban peut être difficile à mettre en place. Ne pas être en mesure de prendre en compte les fluctuations des délais d’approvisionnement pourrait en fin de compte conduire à ce que des tampons excessivement grands soient conservés en permanence.
Il en va de même lorsque la demande varie au cours de l’année, avec par exemple une forte saisonnalité. Même avec un système tiré, la demande doit être accommodée d’une manière ou d’une autre pour éviter les ruptures de stock. Que ce soit pour la production ou la gestion de la supply chain, la détermination de la taille des bacs ne devrait pas rester constante dans ce cas. Par ailleurs, si les bacs sont constamment réévalués, le système perd une grande partie de sa signification. Par conséquent, l’un des principaux reproches que l’on peut faire au système Kanban est son manque de proactivité et d’adaptabilité.
Kanban devient également inefficace - ou beaucoup plus difficile à mettre en œuvre - lorsqu’il s’agit de production en lots et économies d’échelle, qui sont par nature assez opposées à une manière de penser « juste assez ». Au contraire, l’idée est de produire en grande quantité en une seule fois (ou d’acheter davantage en passant une grosse commande à un fournisseur pour obtenir des prix plus bas) afin de réduire les coûts. Cela signifie également prendre le risque de produire ou de stocker trop en anticipant une demande qui pourrait ne pas se concrétiser. Prendre de tels risques peut s’avérer très récompensateur, tandis que Kanban, de manière plus stable, pourrait ne pas décevoir, mais pourrait également ne pas offrir autant d’avantages.
Enfin, on peut soutenir que Kanban repose sur une vision très locale, avec une optimisation étape par étape, et une action locale et simple à entreprendre en réponse à un événement particulier. Il tire sa force d’une telle vision locale, mais en même temps, Kanban reste aveugle aux effets de réseau, à une mauvaise répartition des flux ou des ressources à travers un système, etc. Il sera également faible face aux risques systémiques. Par exemple, dans certaines entreprises B2B, certaines catégories de produits n’existent que si un certain client existe. Lorsque ce client disparaît, le besoin pour le produit disparaît complètement. Kanban n’est tout simplement pas conçu pour prendre en compte un tel risque. Il en va de même pour les problèmes d’obsolescence. Ces inconvénients ne disqualifient pas Kanban en tant que système efficace. Ils soulignent simplement qu’il doit être utilisé en comprenant ses limites inhérentes.
Kanban appliqué à la SCM et au contrôle des stocks
Initialement lié uniquement à la fabrication, Kanban a suivi sa méthode sœur, Lean, vers le domaine de la Supply Chain Management (SCM). Le principe reste le même : une méthode simple et visuelle pour émettre un bon de commande pour une quantité prédéfinie lorsque les stocks sont épuisés, afin de minimiser les stocks et les risques associés. Cela n’est pas surprenant, puisque Kanban est initialement issu de l’observation des consommateurs dans les supermarchés. Les consommateurs n’achètent pas des produits pour les accumuler chez eux ; ils achètent ce dont ils ont besoin et reviennent lorsque les produits ont été consommés. Ils le font en sachant qu’il y aura toujours plus de produits disponibles dès qu’ils en auront besoin. Dans les supermarchés eux-mêmes, les rayons sont organisés pour contenir une certaine quantité de produits et jamais plus ; dès qu’ils commencent à se vider du fait que le contenu a été consommé, ils sont réapprovisionnés en conséquence. Il existe classiquement plusieurs profondeurs de rayons standardisées afin de prendre en compte la rotation des produits. Tout intervenant parcourant les rayons peut rapidement évaluer d’un coup d’œil si un réapprovisionnement est nécessaire ou non.
Ce qui est vrai au niveau local pour les supermarchés et les points de vente en général peut être étendu davantage. Dans la SCM, la méthode des 3 bacs pourrait être interprétée comme suit : un premier « bac » est placé au niveau du magasin ou du point de vente pour satisfaire la demande initiale, un deuxième bac est situé au niveau de l’entrepôt (ou à tout point d’inventaire équivalent), et un troisième se trouve chez le fournisseur. Lorsque le magasin utilise ses stocks, il signale le besoin de réapprovisionnement à l’entrepôt, qui à son tour se tourne vers le fournisseur. Ce qui a été dit ci-dessus concernant la taille des bacs reste vrai : la taille du « bac » est directement liée à la quantité de stock de sécurité que l’organisation est prête à détenir et au délai de livraison du fournisseur ainsi qu’à sa capacité à réapprovisionner de manière fiable. Des considérations supplémentaires peuvent s’ajouter au niveau du fournisseur, telles que le MOQ (Minimum Order Quantity), car le fournisseur pourrait ne pas être disposé à réapprovisionner à moins que certaines quantités ne soient atteintes, ce qui peut être commun à plusieurs références et ne pas être envisagé SKU par SKU. Parfois, il s’agit simplement d’une question de prix unitaire. Un petit réapprovisionnement peut être possible, mais coûteux.
Les avantages et inconvénients du Kanban pour la SCM sont ceux mentionnés précédemment et ne diffèrent pas de ce qui peut être dit pour la fabrication. L’application du Kanban réduit généralement les stocks (ainsi que les risques et coûts associés), en partie au détriment de la flexibilité et en introduisant une dépendance plus forte vis-à-vis des fournisseurs et de leurs délais de livraison. Cela complique la possibilité de bénéficier des effets de réseau ou de tirer parti des MOQ (Minimum Order Quantity), des MOV (Minimum Order Value) ou des remises sur les prix.
De plus, en utilisant une vision assez simple des stocks, Kanban est aveugle aux situations où l’irrégularité pourrait être un atout. Kanban repose sur le postulat que la production doit se poursuivre sans interruption et que le réapprovisionnement doit continuer dès que les stocks ont été utilisés. Cependant, il existe des situations où les ruptures de stock peuvent être souhaitables, notamment pour des produits en fin de cycle de vie ou des produits saisonniers. Il y a aussi des situations où des fournisseurs peu fiables, ou plutôt des fournisseurs avec des délais de livraison longs ou erratiques, peuvent signifier des prix par unité plus bas. Vendre certains articles qui sont parfois en rupture de stock mais qui présentent de fortes marges peut s’avérer avantageux, et conserver des stocks de sécurité (ou des bacs complets) suffisamment élevés pour ne jamais être en rupture est généralement impraticable. Pour certains produits, tirer parti du fait qu’ils sont produits de manière intermittente (par exemple, des fraises locales) ou sont susceptibles aux fluctuations du marché (par exemple, des productions liées aux prix du marché mondial) peut représenter un énorme avantage pour une organisation. Kanban ne le permet tout simplement pas vraiment.
Cependant, lorsque la demande est extrêmement stable, ou extrêmement faible, à tel point que les prévisions sont très inexactes, Kanban peut être l’une des meilleures options disponibles. Par exemple, dans la mode, certains petits points de vente connaissent de faibles volumes de ventes de manière très erratique. Certains SKU pourraient n’obtenir que quelques ventes pendant une saison. Pour ces points de vente et ce type de références, Kanban peut être une solution de référence, car toute autre approche échoue.
Nous avons déjà expliqué que Kanban atténue le besoin de prévisions mais ne les supprime pas - la détermination de la taille des bacs étant une sorte de prévision en soi. On peut donc soutenir que des approches mixtes sont possibles. Les prévisions peuvent envahir Kanban et, réciproquement, il est possible d’intégrer une touche de Kanban dans un processus de prévision grâce à quelques heuristiques pour les situations qui l’exigent.
La vision de Lokad
La puissance de Kanban réside dans la puissance d’heuristiques bien choisies et d’invariants imposés. Elles sont une approximation, mais elles sont robustes et immuables. Elles sont mises en œuvre avec une conception garantissant la correction et une limitation des risques en tête, ce qui est souvent difficile à surpasser. On pourrait dire qu’il existe une « vallée dérangeante » entre Kanban et d’autres méthodes. Kanban peut définitivement être surpassé, mais cela demande beaucoup d’efforts. Pour de nombreuses situations, la méthode de prévision doit présenter une réelle supériorité pour surmonter les bénéfices de Kanban et de ses simples bacs, stocks de sécurité et cartes.
Cependant, cette méthode simple demeure statique, avec une vision locale, peu sophistiquée et aveugle à certaines classes de risques (et de récompenses). Elle ne sera pas utile lorsqu’il s’agit de problèmes de réseau, ou d’évaluer les avantages des irrégularités. Chez Lokad, nous croyons qu’il est possible de tirer le meilleur des deux mondes et d’aller au-delà du Kanban en tirant parti, lorsque la situation l’exige, d’heuristiques intelligentes ancrées dans la réalité des affaires. C’est l’une des idées derrière les listes prioritaires que nous essayons de mettre en œuvre avec la Supply Chain Quantitative: garder les choses simples et visuelles pour l’utilisateur, tout en offrant une solution évolutive, mesurée, réfléchie et révisée qui est toujours guidée par les données.