Lagerumschlag (Lagerumschläge)
In der Buchhaltung bezeichnet der Lagerumschlag (auch bekannt als Lagerumschläge oder Bestandsumschlag) die Anzahl der Male, in denen der Bestand in einem bestimmten Zeitraum, typischerweise einem Jahr, verkauft oder verbraucht wird. Der Lagerumschlag wird typischerweise entweder auf SKU (Stock-Keeping Unit) Ebene gemessen oder auf einer aggregierten Ebene durchschnittlich ermittelt. Numerisch wird der Lagerumschlag häufig als das Verhältnis der verkauften Warenkosten zum durchschnittlichen Lagerbestand definiert. Diese Messung dient als Stellvertreter für die gesamte supply chain performance, insbesondere aus der Perspektive des Betriebskapitals. Der Lagerumschlag ist eine weit verbreitete Kennzahl, besonders in den FMCG-Sektoren.
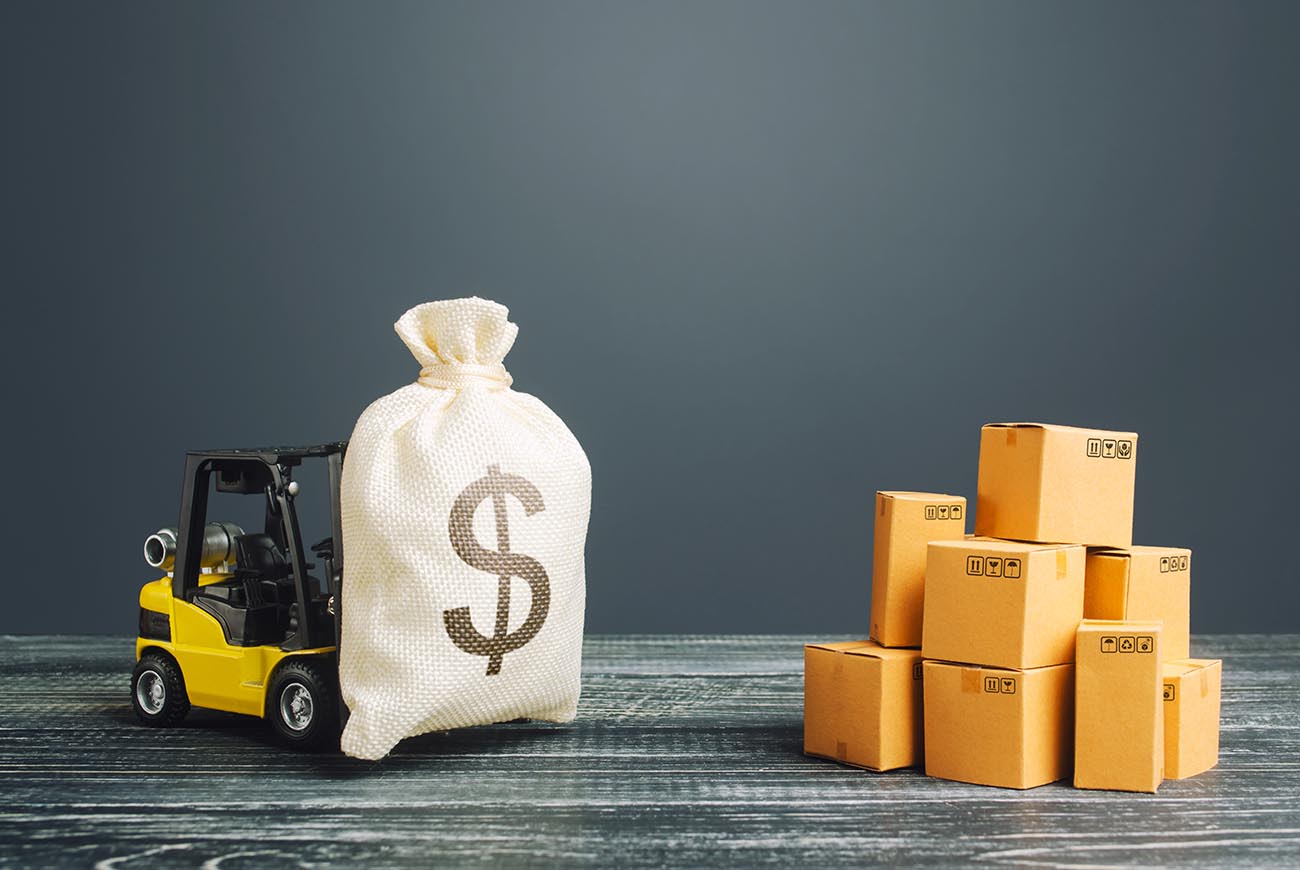
Überblick über die Lagerumschlagsverhältnisse
Unter gleichen Bedingungen wird ein Unternehmen, das es schafft, eine Produkteinheit für $1 zu kaufen und sie dann für $2 weiterzuverkaufen, während es diesen Zyklus 20 Mal im Jahr durchführt, doppelt so viel Bruttogewinn erwirtschaften wie ein Wettbewerber, der denselben Zyklus nur 10 Mal im Jahr durchführt. Dennoch haben beide Unternehmen in Bezug auf ihre Lagerbestände ungefähr die gleichen Anforderungen an das Betriebskapital. Daher, auch wenn sich Lagerumschläge nicht direkt in Rentabilitätsniveaus übersetzen lassen, korrelieren sie in hohem Maße.
Auch wenn die Analyse der Lagerumschlagsverhältnisse auf SKU-Ebene erfolgt, sind Ausreißer aus der Perspektive des Supply Chain Management (SCM) in der Regel von größtem Interesse. Tatsächlich werden SKUs mit niedrigen Lagerumschlagsverhältnissen häufig mit übermäßig hohem Bestand oder sogar mit totem Lagerbestand und Bestandsabschreibungen in Verbindung gebracht. Zudem erhöhen niedrige Quoten den Druck auf die Anforderungen an das Betriebskapital.
Im Gegensatz dazu werden hohe Lagerumschlagsverhältnisse im Allgemeinen mit einem schnellen Verkauf der Waren und einem gesunden Lagerbestand assoziiert, bei dem es nur wenige Probleme mit Wertminderung und Veralterung gibt. Obwohl hohe Quoten häufig als Ausdruck einer guten Bestandskontrolle angesehen werden, können sie auch auf unzureichende Sicherheitsbestände oder auf einen ungenügenden Schutz vor supply chain Risiken hinweisen.
In der Praxis sind Lieferzeiten in der Regel der treibende Faktor hinter den beobachteten Lagerumschlagsverhältnissen. Tatsächlich führen entfernte Lieferanten (möglicherweise auch überseeische Lieferanten) zu hohen Lagerbeständen, da der Bestand, der benötigt wird, um die gesamte lead demand abzudecken, höher ist, was mechanisch die Lagerumschlagsverhältnisse senkt. Andere Faktoren wie Losgrößen, MOQ (Mindestbestellmenge) oder EOQ (wirtschaftliche Bestellmenge) beeinflussen diese Verhältnisse ebenfalls.
Lagerumschlagsformel
Das Verhältnis des Lagerumschlags wird klassischerweise entweder aus der Einkaufsperspektive oder aus der Verkaufsperspektive definiert. Die Einkaufsperspektive spiegelt sich in folgender Formel wider:
Inventory Turnover = Cost of Goods Sold / Average Inventory at Cost
Dabei:
- die Cost of Goods Sold (COGS) umfasst die Anschaffungskosten der Rohmaterialien sowie die Herstellungskosten, falls vor dem Verkauf des Endprodukts in einem bestimmten Zeitraum eine Umwandlung stattgefunden hat. Diese Kosten beinhalten nicht die Vertriebskosten (wie Werbung) oder allgemeine Verwaltungskosten (wie Personalwesen).
- der Average Inventory at Cost folgt derselben Kostendefinition wie die bei den COGS, wird jedoch auf den gesamten aktuell vom Unternehmen gehaltenen Bestand angewendet, sei es verfügbar oder bestellt. Diese Kosten beinhalten nicht die Lagerhaltungskosten.
Die Verkaufsperspektive spiegelt sich in folgender Formel wider:
Inventory Turnover = Net Sales / Average Inventory at Selling Price
Dabei:
- der Nettoumsatz stellt die Einnahmen dar, die durch den Verkauf der Einheiten in einem bestimmten Zeitraum generiert werden, ohne Steuern (wie Mehrwertsteuer) sowie temporäre Rückvergütungen oder Rabatte.
- der Average Inventory at Selling Price folgt demselben Bewertungsmaßstab wie der für den Nettoumsatz, wird jedoch auf den gesamten, vom Unternehmen aktuell gehaltenen Bestand angewendet, wie oben.
Beide Perspektiven erfordern, dass der gesamte Bestand in die Berechnung einbezogen wird. Dies umfasst den verfügbaren Lagerbestand, aber auch die auf Bestellung befindlichen Waren. Tatsächlich trägt das Unternehmen, sobald die Waren bestellt sind, das mit diesen Mengen verbundene Risiko, was sich negativ auf die Agilität der supply chain des Unternehmens auswirkt.
Es existieren viele weitere Varianten des “Turnover”. Der Zähler repräsentiert stets den Fluss des Bestands, während der Nenner immer den Zustand des Bestands widerspiegelt. Die meisten dieser Varianten sind akzeptabel, solange das Verhältnis homogen ist und die Einheiten für beide Werte übereinstimmen. Abstrakt kann man sagen, dass der Lagerumschlag versucht, das Verhältnis Fluss über Zustand abzubilden.
Als Faustregel gilt, dass die einkaufsspezifische Variante des Lagerumschlags in den meisten Branchen vorherrscht. Betrachtet man die mit Teilen, Komponenten oder Rohmaterialien assoziierten Lagerbestände, ist der Begriff des Verkaufspreises des Bestands etwas unklar, da nur die Preise der Endprodukte direkt beobachtet werden.
Panelteilnehmer und Ersteller von Branchendaten verwenden häufig den Nettoumsatz als Zähler in der Lagerumschlagsformel. Die Hauptmotivation für diese Praxis ist die Zurückhaltung der Unternehmen, ihre detaillierten Bruttomargen preiszugeben. Tatsächlich gelten Verkaufsvolumen als weniger sensibel, da die Verkaufspreise ohnehin bereits öffentlich sind.
Anekdotisch gibt es viele populäre post-hoc Rechtfertigungen für diesen Umstand, basierend auf der vermeintlichen Überlegenheit der Verkaufsperspektive, die vor allem von jenen Akteuren gefördert wird, denen die Daten fehlen, um die Einkaufsperspektive anzuwenden. Obwohl die Verkaufsperspektive nicht ohne Verdienste ist, hat sie nahezu identische Vor- und Nachteile im Vergleich zu ihrer Einkaufsversion.
Einschränkungen der Lagerumschlagsquoten
Trotz der weit verbreiteten Annahme, dass Lagerumschlagsquoten (im Folgenden einfach als Turns bezeichnet) einen guten Stellvertreter für die supply chain performance eines Unternehmens darstellen, sind diese Indikatoren bestenfalls Stellvertreter. Sie leiden unter vielen oft unterschätzten Einschränkungen.
Verborgene Komplexitäten. Die Messung von Turns ist ein komplexes Unterfangen, da die meisten naiven Messungen zu simpel sind und unsinnige Ergebnisse liefern. Zum Beispiel ist der Begriff der COGS ein ziemlich unklarer Begriff, wenn Lieferanten Preisreduzierungen anbieten oder wenn beim Einkauf von Rohstoffen deren Marktpreise sich ständig ändern. Umgekehrt können Erträge durch Retouren, Rückrufe oder Promotions negativ beeinflusst werden, was im Gegensatz dazu optisch zu verbessern (niedrigere Turns) scheint. In der Praxis müssen Turns mit viel Fachwissen individuell erarbeitet werden, um Probleme zu mildern, die den ursprünglichen Zweck, Turns als faire Darstellung der supply chain Rücklaufquote zu verwenden, unterlaufen würden. Die meisten Enterprise Software liefert nicht das erforderliche Detaillierungsniveau, wenn es um die KPIs der Turns geht, sodass Teams gezwungen sind, auf Tabellenkalkulationen zurückzugreifen, um “angemessene” Messungen zu erhalten.
Veralteter Indikator. Aufgrund der Konzeption müssen Turns über lange Zeiträume gemittelt werden, die ein Vielfaches der Lieferzeiten darstellen, um statistisch signifikant zu sein. Außerdem muss der Messzeitraum häufig so lang wie ein Jahr sein, um aufgrund von Nachfragemustern wie Saisonalität sinnvolle Ergebnisse zu liefern. Infolgedessen skizzieren Turns nur ziemlich “alte” Probleme – die bereits behoben worden sein sollten – oder langsame Veränderungen in der supply chain des Unternehmens, die früher durch alternative Indikatoren hätten erkannt werden müssen. Die Minderung der Veralterung von Turns erfordert in der Praxis vorhersagende Technologien, die in der Lage sind, aktuelle Beobachtungen zuverlässig zu extrapolieren und deren lokale (zeitliche) Verzerrungen, wie Saisonalität, Promotions, stock-outs, etc. zu korrigieren.
Bikeshedding. Wie die meisten supply chain Indikatoren – und insbesondere ABC-Analyse – sind Turns äußerst anfällig für lange, unproduktive Diskussionen, an denen innerhalb des Unternehmens mehrere Parteien beteiligt sind – Buchhaltung, Finanzen, supply chain, Fertigung … Zudem, da der Indikator in der Theorie sowohl einfach als auch in der Praxis komplex ist, neigen KPIs, die auf Turns basieren, in vielerlei Hinsicht dazu, irreführend zu sein, was zu weiteren Reibungen zwischen den Teams und zu einer potenziell fehlerhaften Gestaltung von Anreizen führt. Diese Einschränkung kann durch eine gründliche Dokumentation des Kleingedruckten der Indikatoren gemildert werden, was jedoch leider der anfänglich wahrgenommenen Einfachheit der Lagerumschlagsquoten widerspricht.
Mangelnde Relevanz. Es gibt Situationen, in denen Lagerumschläge schlichtweg irrelevant sind. In von Neuheiten getriebenen Branchen – Mode, Luxus, Kulturprodukte – sind Produkte oft ein Treffer oder Fehl, und der Nachfragelebenszyklus der Produkte könnte zu kurz sein, als dass Turns wirklich zählen würden. In Branchen, die von fortlaufenden (reparierbaren) Beständen angetrieben werden – Luft- und Raumfahrt, Industrieausrüstung – ist die TAT (Turn-Around Time) in der Regel aussagekräftiger als die Lagerumschlagsquoten.
Methoden zur Verbesserung der Lagerumschlagsquoten
Es gibt mehrere populäre Ansätze, um die Lagerumschlagsquoten zu senken, wobei jeder Ansatz seine eigenen Nachteile mit sich bringt.
Methode | Vorteile | Nachteile |
---|---|---|
Senkung der Verkaufspreise | Niedrigere Preise steigern die Nachfrage und führen zu weiteren economies of scale | Niedrigere Margen und Abschreibung des Markenwerts |
Reduzierung der Sortimentsbreite, Eliminierung von Ladenhütern | Reduzierte supply chain Komplexität, geringere Lagerbestände | Potenzielle Benachteiligung der Kunden, Verlust von loyalty |
Verkürzung der Lieferzeiten, mehr lokale Lieferanten | Keine Vorabinvestition, bessere Gesamtagilität | Erhöhte Transportkosten, teurere Lieferanten |
Reduktion der Losgrößen, MOQ und EOQ | Bessere Gesamtagilität der supply chain über bessere Turns hinaus | Erhöhte Einkaufs- und/oder Herstellungskosten |
Senkung der Sicherheitsbestände | Reduziertes Betriebskapital, geringere Lagerhaltungskosten | Potenzielle Benachteiligung der Kunden, Lagerausfälle können störend sein |
Verbesserung der prädiktiven Bewertung von Bestandsrisiken | Reduziert nicht nur die schlechtesten Turns, sondern auch Bestandsabschreibungen und Veraltungskosten | Schwierig umzusetzen. Die meisten Softwareanbieter übertreffen nicht den Status quo |
Anreize für rückständiger Auftrag oder verzögerte Lieferungen | Rückständige Aufträge beinhalten geringe Bestandsrisiken und geringes Betriebskapital | Kunden könnten zu Wettbewerbern wechseln, wenn die Lieferzeit entscheidend ist |
Zusammenfassend ist die “lower turns”-Perspektive eng gefasst und erfasst nicht, was üblicherweise als leistungsstarke supply chain wahrgenommen wird. Daher sollten Turns zwar typischerweise reduziert werden, wenn sich eine kostengünstige Möglichkeit bietet, jedoch müssen Sekundäreffekte wie der Verlust der Kundenloyalität oder die Beibehaltung nicht wettbewerbsfähiger Lieferanten bewertet werden, um zu entscheiden, ob das Endergebnis einen Nettogewinn für das Unternehmen darstellt.
Lokads Sichtweise
Wie die meisten (scheinbar) einfachen supply chain Indikatoren sind die Lagerumschlagsquoten einköpfig und spiegeln nicht angemessen die widersprüchlichen wirtschaftlichen Kräfte wider, die innerhalb des Unternehmens und seiner supply chain wirken. Turns, ähnlich wie Sicherheitsbestände, sind ein Ausgleich zwischen verschiedenen Risiken, vor allem den Kosten des Bestands und den Kosten von stock-outs. Zwar können Turns wertvolle hochrangige Einblicke in die supply chain bieten, doch die Verfeinerung dieser Messungen, sodass sie auf die “richtige” Weise durchgeführt werden, erfordert einen enormen Aufwand, der von vielen Unternehmen tendenziell stark unterschätzt wird, da die meisten Anbieter von Enterprise Software sofort einsatzfähige Turn-ähnliche KPIs bieten. Dennoch sind diese eingebauten Funktionen in Bezug auf die Spezifika des Unternehmens immer recht einfach gestrickt. Daher erfordern diese KPIs in der Praxis maßgeschneiderte Implementierungen, die häufig die Kapazitäten der BI (Business Intelligence)-Werkzeuge, die nicht auf komplexe finanzielle Ingenieurkunst ausgelegt sind, übersteigen.