Lieferzeit
Eine Lieferzeit ist die Verzögerung zwischen dem Beginn und dem Abschluss eines Prozesses. In supply chains, wann immer Waren gekauft, verarbeitet oder gewartet werden, sind Lieferzeiten involviert, die üblicherweise in Tagen gemessen werden. Aus planungstechnischer Sicht sind Lieferzeiten von Bedeutung, da sie implizieren, dass die meisten routinemäßigen Entscheidungen im Voraus getroffen werden müssen, um die beabsichtigte Wirkung zu erzielen, wie z. B. die Aufrechterhaltung der Servicequalität. Der Bedarf an Nachfrageprognosen ergibt sich typischerweise ebenfalls aus dem Vorhandensein von Lieferzeiten, da die Angemessenheit einer Entscheidung – wie z. B. einer Bestands replenishment – von unbekannten zukünftigen Ereignissen abhängt, die die supply chain während der gesamten Lieferzeit beeinflussen.
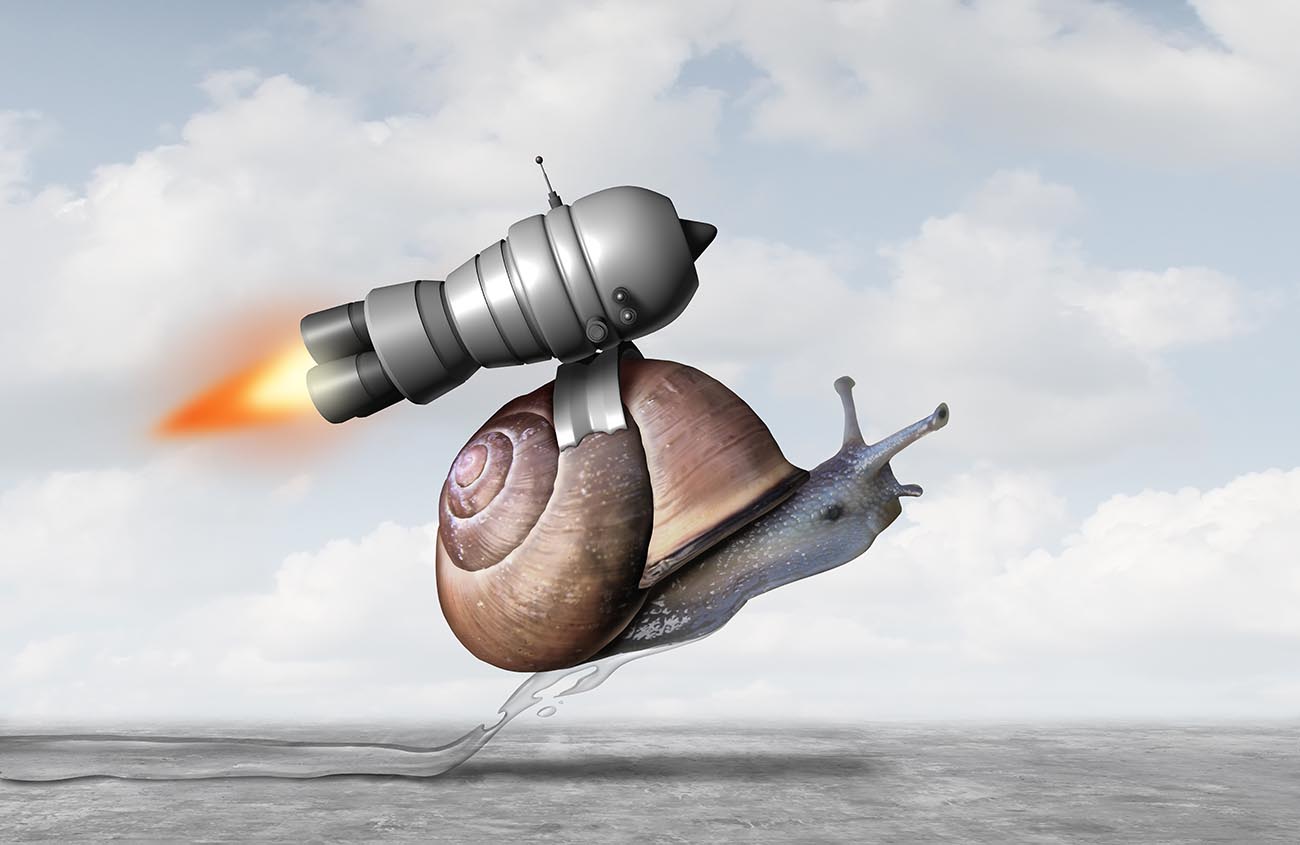
Ursachen und Konsequenzen von Lieferzeiten
Lieferzeiten prägen maßgeblich den Betrieb der supply chain und die meisten ihrer finanziellen Elemente, wie das erforderliche Betriebskapital und die Kapitalrendite (ROCE). Tatsächlich bedeuten längere Lieferzeiten, dass es länger dauert, einen Inventurzyklus abzuschließen, in dem Materialien oder Produkte gekauft, möglicherweise verarbeitet und wieder verkauft werden.
Längere Lieferzeiten bedeuten mechanisch höhere Lagerverpflichtungen, selbst wenn die vorhandenen Bestände scheinbar niedrig bleiben. Zum Beispiel, wenn ein Unternehmen in Europa Waren aus Asien bestellt, die per Container geliefert werden sollen, ist das Unternehmen ab dem Datum der Bestellaufgabe verpflichtet, die Waren zu verkaufen oder zu verbrauchen. Dennoch dauert es in diesem Fall typischerweise über 6 Wochen, bis die stock levels in Europa diesen Auftrag widerspiegeln.
Außerdem erhöhen längere Lieferzeiten die Abhängigkeit von Prognosen. Betrachtet man das obige Beispiel, kann sich das Unternehmen nicht leisten, lediglich eine Bestellung basierend auf seinen aktuellen Bedürfnissen aufzugeben; bis die Bestellung eintrifft, hat sich die Situation verändert. Die aktuellen Lagerbestände werden durch den fortlaufenden Verbrauch weiter reduziert, und die Nachfrage wird sich höchstwahrscheinlich verändert haben, wenn auch nur aufgrund der Saisonalität.
Lieferzeiten stellen eine Untergrenze für die maximale Agilität dar, die ein Unternehmen erreichen kann. Als Faustregel gilt, dass, wenn sich die Marktbedingungen drastisch ändern, das Unternehmen grob für die Dauer der Lieferzeiten an seine bisherigen Entscheidungen gebunden bleibt. Es gibt verschiedene Möglichkeiten, diese Effekte abzumildern, angefangen bei vertraglichen Vereinbarungen mit den Lieferanten. Die zugrundeliegenden Risiken können jedoch selten vollständig eliminiert und werden lediglich innerhalb der supply chain verlagert.
Angesichts der negativen Auswirkungen längerer Lieferzeiten könnte man sich fragen, warum Unternehmen häufig scheinbar (subjektiv) lange Lieferzeiten in Kauf nehmen. Es stellt sich heraus, dass es verschiedene wirtschaftliche Faktoren gibt, die die Waagschalen zugunsten längerer Lieferzeiten verschieben.
Spezialisierung treibt längere Lieferzeiten voran: Einige Länder verfügen über ziemlich einzigartige Industrien1, die vor Ort schwer oder kostspielig zu reproduzieren sind. Solch konzentrierte Industrien entstanden historisch primär aufgrund von hochwertigen Materialien, die leicht zu transportieren waren. Selbst wenn Flugzeuge jeden Punkt des Globus in weniger als 24 Stunden erreichen können, führen Zollabfertigungen und Prozesse dazu, dass die tatsächlichen Lieferzeiten bei der Betrachtung von Übersee-Lieferanten erheblich steigen.
Auch Economies of scale begünstigen längere Lieferzeiten. Durch die Erhöhung der Losgrößen (häufig realisiert als MOQs) können Hersteller oder Transportunternehmen ihre Kosten senken. Allerdings, wenn die losweise abgesetzten Mengen größer werden, nimmt auch die Anzahl der Lose ab und damit deren Frequenz – unter ansonsten gleichen Bedingungen, insbesondere bei der Nachfrage. Dennoch sind nicht alle Branchen gleichermaßen anfällig für economies of scale, die je nach angewendeter Technologie tendenziell ein Plateau erreichen.
Reduzierung der hohen Quantile
Während eine Lieferzeit durch Verringerung ihrer durchschnittlichen Dauer verbessert werden kann, zählen in der Regel vor allem die Verbesserungen der schlimmsten Fälle – also der längsten Situationen – am meisten. In supply chains konzentrieren sich die größten Probleme – gemessen in Dollar des Einflusses – tendenziell am Ende der Verteilung: Es sind die unerwartet langen Lieferzeiten, die stock-outs oder Produktionsunterbrechungen verursachen, nicht die kleinen Stolpersteine.
Eine der einfachsten Methoden, diese Worst-Case-Szenarien zu bewerten, besteht in der Verwendung von Quantilen. Zum Beispiel, wenn ein Lieferant eine 7-tägige Lieferzeit für das 95%-Quantil angibt, bedeutet dies, dass 95% der an diesen Lieferanten erteilten Bestellungen in weniger als 7 Tagen geliefert werden. Diese „hohen“ Quantile, also nahe 100%, können erheblich von der durchschnittlichen Lieferzeit abweichen. Derselbe Lieferant könnte im Durchschnitt in 2 Tagen liefern, was weniger als ein Drittel seiner Schätzung des hohen Quantils für dieselbe Lieferzeit ausmacht.
Um diese Servicequalitätsprobleme zu vermeiden, wachsen alle Lagerpuffer innerhalb der supply chain – unabhängig von der verwendeten Methodik – in der Regel linear, nicht mit dem Durchschnitt der Lieferzeit, sondern mit einem hohen Quantil der Lieferzeit. Tatsächlich existieren Lagerpuffer genau dazu, Schwankungen der supply chain-Bedingungen auszugleichen. Die beiden dominierenden Faktoren, die die unerwarteten Schwankungen in der supply chain verursachen, sind in der Regel: schwankende Nachfrage und schwankende Lieferzeit.
Vielfalt der Lieferzeiten
Die gesamte Lieferzeit von den ursprünglichen Bestellungen bei den Lieferanten bis zur Lieferung an den Kunden kann in der Regel in viele, möglicherweise Dutzende, Zwischenstufen zerlegt werden. Um entweder den Wert der Lieferzeit oder ihre Variabilität zu reduzieren, ist es in der Regel effektiv, diese gesamte Lieferzeit in ihre wesentlichen Teilkomponenten zu zerlegen, die einfacher zu analysieren und zu verbessern sind.
Zum Beispiel kann ein Großhändler, der Waren von ausländischen Lieferanten bezieht, vor folgenden Herausforderungen stehen:
- Eine Bestell-Lieferzeit, verursacht durch den wöchentlichen Einkaufsprozess des Großhändlers selbst.
- Eine Gelegenheitslieferzeit, verursacht durch die MOQs der Lieferanten.
- Eine Produktionslieferzeit, die von den Lieferanten benötigt wird, um die Bestellung zu erfüllen.
- Eine Transportlieferzeit, die von dem Frachtunternehmen benötigt wird.
- Eine administrative Lieferzeit, um den Zollprozess zu durchlaufen.
- Eine Empfangs-Lieferzeit, für Inventarisierung und Qualitätskontrolle durch den Großhändler.
- Eine Versandlieferzeit, die vom Distributionszentrum benötigt wird, um Kundenaufträge zu erfüllen.
- Eine Zustell-Lieferzeit für die letzte Meile, die von einem Transportunternehmen benötigt wird, um die Lieferung an den Kunden zu tätigen.
Für jeden Vorgang ist es in der Regel von Interesse, sowohl die durchschnittliche Verzögerung als auch die Varianz der Verzögerung zu verringern.
Die Überwachung all dieser Vorgänge erfordert viel Bürotätigkeit, die durch moderne IT-Systeme entweder über Barcodes und/oder RFIDs erheblich erleichtert werden kann. Electronic records werden typischerweise in den IT-Systemen der beteiligten Unternehmen gespeichert. Die Vorteile gehen weit über die Optimierung der Lieferzeiten hinaus, da diese Systeme die traceability der Waren gewährleisten und bis zu einem gewissen Grad Schwund im Bestand verhindern.
Bis in die späten 1990er-Jahre erforderte das Speichern und Verarbeiten all dieser Aufzeichnungen kostspielige Rechenressourcen, sodass es nicht immer wirtschaftlich machbar war, alle detaillierten Aufzeichnungen, die durch den Fluss physischer Waren innerhalb einer supply chain generiert wurden, zu erfassen und noch weniger zu speichern. Seit den frühen 2010er-Jahren sind die Kosten für Datenspeicherung und Rechnen jedoch weit unter den Punkt gefallen, an dem rohe Rechenressourcen nahezu keine Rolle mehr spielen, wenn es um physische Abläufe geht. Dennoch können IT-Kosten, insbesondere Systemintegrationen, den Erwerb dieser elektronischen Aufzeichnungen verhindern.
Um Lieferzeiten zu verbessern und somit, wie oben diskutiert, in der Regel ihre hohen Quantile zu reduzieren, sind Messungen erforderlich. Feinkörnige Messungen der Lieferzeit sind sehr nützlich, wenn es um Ursachenanalysen geht. Tatsächlich variiert die Art der vorgenommenen Verbesserungen stark, da die Abläufe von einem Schritt zum nächsten erheblich variieren.
Bestelllieferzeit
Die Bestelllieferzeit bezieht sich typischerweise auf die Zeitspanne zwischen der Kundenbestellung und der Lieferung der Waren. Diese Dauer fällt auf, da es die Art von Lieferzeit ist, an die die breite Öffentlichkeit – im Gegensatz zu supply chain specialists – gewöhnt ist. In vielen Branchen außerhalb des B2C-Ecommerce steht die Bestelllieferzeit in engem Zusammenhang mit der Servicequalität. Insbesondere sind stockouts oft der dominierende Faktor, der zu außergewöhnlich langen Bestelllieferzeiten führt.
Ein Teil der Herausforderung, die Bestelllieferzeiten zu verbessern, besteht nicht darin, die Lieferzeiten selbst zu verkürzen, sondern die richtigen Erwartungen der Kunden hinsichtlich des Lieferdatums zu setzen. Insbesondere scheinen mehrere große E-Commerce-Unternehmen seit über einem Jahrzehnt den Ansatz zu verfolgen, eine quantile forecast Schätzung der Bestelllieferzeit zu teilen, die als wahrscheinliche obere Grenze für die Verzögerung fungiert. Die Verzerrung in der Verzögerungsschätzung wird absichtlich eingeführt, um die Häufigkeit von Situationen zu minimieren, in denen die Waren nicht rechtzeitig geliefert werden.
Lieferzeitprognose
Die richtige Vorhersage zukünftiger Lieferzeiten ist ein wesentlicher Bestandteil der Optimierung einer supply chain. Ähnlich wie bei der Nachfrage können und sollten Lieferzeiten prognostiziert werden, wobei in der Regel auf die vorhandenen historischen Daten zurückgegriffen wird, wann immer dies relevant ist.
Obwohl die Prognose von Lieferzeiten bei den „Nachfrage“-Planungsteams (noch) nicht weit verbreitet ist, muss beachtet werden, dass die meisten Zyklen, die auf die Nachfrage zutreffen, auch bei Lieferzeiten beobachtet werden können. Zum Beispiel neigen Lieferzeiten dazu, Saisonalitäten, Effekte des Tages im Monat und der Woche aufzuweisen. Lieferzeiten ändern sich im Laufe der Zeit. Ein Lieferant könnte beispielsweise seine Prozesse überarbeiten, um die Lieferzeiten zu verkürzen, oder sie erhöhen, um seine Kosten zu senken. Auch Quasi-Saisonalitäten spielen eine Rolle, etwa mit Ereignissen wie dem chinesischen Neujahr, das die Lieferzeiten periodisch in die Höhe treibt, da in dieser Zeit viele Fabriken in Asien geschlossen sind.
Probabilistic forecasts sollten für Lieferzeiten bevorzugt werden, denn wie oben erwähnt, sind es die hohen Quantile, die die wirtschaftlichen Auswirkungen der Lieferzeiten bestimmen. Die Kosten und Probleme konzentrieren sich am Ende der Verteilung. Allerdings sei gleich darauf hingewiesen, dass für Lieferzeiten keine Normalverteilungen (Gaussian) verwendet werden sollten. Als Faustregel gilt: Lieferzeiten sind niemals normalverteilt, und die Nutzung eines solchen Modells führt zu einer massiven Unterschätzung der hohen Quantile, was wiederum die Grundlage für eine fortlaufende Reihe von Serviceproblemen darstellt.
Lieferzeiten können besser als multimodale Verteilungen modelliert werden, die das zugrunde liegende physische System widerspiegeln. Zum Beispiel neigen die Produktionslieferzeiten einer Produktionslinie dazu, sehr vorhersehbar zu sein, es sei denn, eine der Rohmaterialien fehlt, in welchem Fall die Herstellungs-Lieferzeit erheblich länger dauern kann. Somit beinhaltet die praktische Modellierung der Wahrscheinlichkeitsverteilung in der Regel eine Mischung aus diskreten und parametrischen Verteilungen.
Für die probabilistische Prognose der Lieferzeit wird erwartet, dass für jede innere Phase eine diskrete Zufallsvariable erzeugt wird. Es ist häufig sinnvoll anzunehmen, dass diese inneren Phasen statistisch unabhängig sind (z. B. ist die durch den Zoll verursachte Verzögerung strikt unabhängig von der Herstellungsverzögerung). In diesen Fällen können die Zufallsvariablen kanonisch summiert werden, was technisch eine Faltung über die zugrunde liegenden Verteilungen bedeutet.
Kontrollierte Modalitäten
Während das geeignete probabilistische Modell zur Lieferzeitprognose in der Regel multimodal ist, gibt es bestimmte Modalitäten, die eine spezifische Behandlung erfordern, wenn ein gewisser Grad an Kontrolle vorliegt, im Gegensatz zu passiven Beobachtungen. Zum Beispiel, wenn es möglich ist, von einem Lieferanten eine Luftfracht oder Seefracht anzufordern, sollten die beiden Transportmodi aus prognostischer Sicht nicht zusammengefasst werden. Es ist ein gewisser Kontrollgrad involviert. Jeder Transportmodus hat seine eigene Variabilität, und somit sind zwei unterschiedliche Prognosen erforderlich.
Nachfragekopplung
Da Produktionskapazitäten bei einem Nachfrageanstieg begrenzt sind, neigt die Produktions-Lieferzeit dazu, ebenfalls zu steigen. Diese Kopplung zwischen Nachfrage und Lieferzeit wirkt sich negativ auf die Servicequalität aus, da sie die Fähigkeit des Unternehmens verringert, einem Nachfrageanstieg durch zusätzliche Einkaufs- oder Produktionsaufträge entgegenzuwirken, gerade wegen der zusätzlichen Lieferzeit. Daher kann es relevant sein, ein gemeinsames Vorhersagemodell für sowohl die Nachfrage als auch die Lieferzeit zu haben, da die erforderlichen Lagerpuffer von zwei Faktoren abhängen.
Allerdings, wenn man Fertigungseinheiten betrachtet, die über genügend Flexibilität verfügen, ihre Auftragsschlangen (neu) zu organisieren, hängen die beobachteten Lieferzeiten stark von der priorisierten Behandlung jedes einzelnen Auftrags ab. Daher sollte die passende prognostische Modellierung der Lieferzeit den Aspekt der Warteschlangenbildung berücksichtigen, da Lieferzeiten je nach willkürlichen Priorisierungsentscheidungen drastisch variieren können. Dieser zusätzliche Kontrollgrad kann genutzt werden, um die Auswirkungen eines Nachfrageanstiegs zu mildern.
Leitnachfrage
Die lead demand zeigt die Menge der Artikel, die über die Dauer der Lieferzeit bedient werden sollen. Dieser Wert ist von besonderem Interesse, da um stockouts zu vermeiden, der Gesamtlagerbestand (Summe aus vorhandenem Bestand und bestelltem Bestand) jederzeit über der lead demand bleiben muss. Sinkt der Gesamtlagerbestand unter die Lieferzeit, ist ein stockout unausweichlich.
Angenommen, dass für sowohl die zukünftige Nachfrage als auch die zukünftige Lieferzeit probabilistische Prognosen erstellt werden können, wird es möglich, (hohe) Quantilschätzungen der lead demand zu berechnen, wie definiert durch:
Wo:
- $${0≤τ≤1}$$ ist das Ziel der Quantilschätzung
- $${y}$$ ist die Nachfrage, die sich im Laufe der Zeit verändert
- $${L}$$ ist die Lieferzeit
- $${Qτ[..]}$$ ist das Quantil der inneren reellwertigen Funktion
- $${Ω}$$ ist die Menge der möglichen Ergebnisse
- $${t}$$ ist die Zeit, wobei 1 die erste zukünftige Periode ist
- $${y_ω}$$ ist die Nachfrage, die dem Ergebnis $${ω}$$ zugeordnet ist
- $${L_ω}$$ ist die Lieferzeit, die dem Ergebnis $${ω}$$ zugeordnet ist
Diese Quantilschätzung des Lieferbedarfs ist von Interesse, wenn man versucht, ein Ziel-Serviceniveau aufrechtzuerhalten. Angenommen wird ein einfaches Bestandsmodell ohne Mindestbestellmenge (MOQ) für einzelne SKUs und einzelne Lieferanten, dann kann die Menge, die zu einem beliebigen Zeitpunkt nachbestellt werden soll, mit der Formel definiert werden:
Wo:
- $${OnHand}$$ ist der Lagerbestand
- $${OnOrder}$$ ist der auf Bestellung befindliche Bestand
Diese Formel geht implizit davon aus, dass keine Nachfrage verloren geht, wenn ein Lagerengpass auftritt. Diese Annahme ist in vielen Situationen nicht realistisch, z. B. im Verbrauchereinzelhandel, wo Kunden typischerweise entweder auf das Produkt verzichten, auf ein Ersatzprodukt ausweichen oder sich für einen Konkurrenten entscheiden, anstatt ihren Konsum einfach zu verschieben. Um diese Annahme aufzuheben, muss die Auswirkung der verlorenen Nachfrage explizit modelliert werden. Dies ist besonders wichtig, wenn die Nachfrage stark saisonal ist, da die Waren, die nach dem saisonalen Höhepunkt verfügbar werden, lange Zeit unverkauft oder ungenutzt bleiben können.
Lieferzeitgetriebene Feedback-Schleifen
Die Lieferzeit kann als ein Eingabefaktor zur Berechnung der Nachbestellung betrachtet werden, wie im vorherigen Abschnitt detailliert beschrieben. Allerdings hängt die Lieferzeit selbst vom Bestell- (oder Produktions-) Zeitplan ab. Außerdem ist der Zeitplan in der Regel so ausgelegt, dass er erwartete Skaleneffekte erzielt, indem die gewünschte EOQ (economic order quantity), MOQ (Mindestbestellmenge) oder die nominale Produktionschargengröße erreicht werden.
Daher sind Fachleute im Bereich supply chain häufig mit einer Feedback-Schleife konfrontiert, die die Entscheidung, die heute getroffen werden muss (Nachbestellung und Bestellung), mit dem Zeitpunkt verbindet, zu dem diese Entscheidung in Zukunft wiederholt werden soll. Einfach ausgedrückt hängt die heute zu bestellende Menge vom Datum der nächsten Nachbestellung ab: Eine spätere Nachbestellung bedeutet, dass eine größere Menge erforderlich ist. Allerdings wird das Datum der nächsten Nachbestellung auch durch die heutige Nachbestellung beeinflusst: Eine größere sofortige Nachbestellung bedeutet ein späteres Datum für die nächste Nachbestellung.
Da die explizite Modellierung und numerische Optimierung dieser Feedback-Schleife nicht trivial sind, erstellen Fachleute im Bereich supply chain häufig einen groben Zeitplan (d. h. eine Bestellung pro Woche, pro Monat), der in etwa den Zielmengen entspricht, um die gewünschte Bestellmenge zu erreichen (d. h. die EOQ, MOQ oder Chargengröße). Dieser Zeitplan wird dann als starr angenommen, während die Nachbestellmengen nach Bedarf variieren. Allerdings führt der Ansatz mit festem Zeitplan per Design zu Ineffizienzen, da die supply chain nicht alle ihre Freiheitsgrade ausschöpft.
Bessere numerische Lösungen können entwickelt werden, um diesen Aspekt der Feedback-Schleife von vornherein anzugehen. Die dabei verwendeten Algorithmen fallen typischerweise unter den Bereich des Reinforcement Learning. Eine detaillierte Darstellung dieser Algorithmen liegt jedoch außerhalb des Umfangs dieses Dokuments.
Branchenspezifische Probleme
Lieferzeiten sind vielfältig und die angemessene Perspektive variiert in der Regel je nach betrachteter Branche. Im folgenden Abschnitt betrachten wir einige Bereiche, die bemerkenswerte spezifische Herausforderungen im Zusammenhang mit den Lieferzeiten aufweisen.
Haltbarkeit von frischen Lebensmitteln
Frische Lebensmittel sind hoch verderblich, und infolgedessen haben die Produkte eine kurze Haltbarkeit. Die Verkürzung der Lieferzeiten ist in der Regel entscheidend, um den Marktwert der Produkte, die in den Verkaufsregalen präsentiert werden sollen, möglichst zu erhalten. Beim Abwägen von Optionen (Verpackung, Transport), die die Lieferzeiten beeinflussen, wirken sich diese Optionen nicht nur auf die Servicequalität aus, sondern häufig auch auf den erwarteten Umsatz und den zu erwartenden Ausschuss der gesamten supply chain.
Zudem stehen Marken oder Distributoren typischerweise vor mehreren Beschaffungsoptionen mit unterschiedlichen Trade-offs zwischen Lieferzeiten und Haltbarkeit. Beispielsweise kann eine Marke direkt vom Produzenten einkaufen, was eine lange Lieferzeit, aber bei Wareneingang eine hohe Haltbarkeit mit sich bringt; oder die Marke kann von einem Großhändler beziehen, was eine kurze Lieferzeit, aber den Erhalt von Produkten mit kurzer Haltbarkeit bedeutet. In diesen Situationen balanciert eine angemessene supply chain optimization beide Optionen aus, was seinerseits eine prädiktive Analyse der jeweiligen Lieferzeiten und Haltbarkeiten erfordert.
Durchlaufzeit (TAT) für MROs
MROs (Maintenance Repair & Overhaul) verwalten reparaturfähige Komponenten. Für jeden Komponententausch muss ein einsatzfähiges Bauteil sofort verfügbar sein, während das demontierte Bauteil bis zur Reparatur nicht einsatzfähig ist. Die gesamte Verzögerung von der Anforderung des Komponententauschs bis zur erneuten Verfügbarkeit der einsatzfähigen Einheit wird als Durchlaufzeit bezeichnet.
Der Bestand an Komponenten, den die MRO vorhält, hängt direkt von der Durchlaufzeit ab. Tatsächlich wäre, wenn die MRO die (theoretische) Fähigkeit hätte, ein nicht einsatzfähiges Bauteil augenblicklich zu reparieren, kein Bestand erforderlich. Folglich neigen Lieferzeitprognosen und -optimierungen dazu, für MROs noch kritischer zu sein als die Nachfrageprognose.
Die Betonung der TAT-Analyse (im Vergleich zur Nachfrageanalyse) wird in der Regel durch die Natur der ungeregelten Reparaturen verstärkt, welche auf Ausfälle zurückzuführen sind, die ein gewisses Maß an irreduzierbarer Unsicherheit in den zugrunde liegenden physikalischen Prozessen mit sich bringen – d. h., wenn es eine Möglichkeit gäbe, das Problem proaktiv anzugehen, würden Diagnosen diese Vorgänge in geplante Reparaturen umwandeln.
Reverse Logistics für E-Commerce
Die meisten Verbraucher-ecommerces in den meisten Ländern bieten heutzutage die Möglichkeit, die Ware zurückzusenden, falls dem Verbraucher das erhaltene Produkt nicht zusagt. Allerdings variiert die Rücksendequote von Land zu Land erheblich, meist aus kulturellen Gründen. Beispielsweise weisen deutsche Verbraucher im Fast-Fashion-ecommerce typischerweise Retourenraten von über 50% auf. Diese hohen Raten werden teilweise durch die Gewohnheit bedingt, mehrere Größen zu bestellen und alle bis auf eine zurückzusenden.
Wenn die Retourenraten hoch sind, muss der Online-Händler damit rechnen, dass ein beträchtlicher Teil des Lagerbestands tatsächlich zurückfließt; andernfalls riskiert der Händler, systematisch mit Überbeständen konfrontiert zu werden, wenn die Artikel nach den Nachbestellvorgängen zurückfließen. Es gibt jedoch drei Unsicherheiten in Bezug auf die zukünftigen Rücksendungen: Erstens, ob die Artikel zurückgeschickt werden oder nicht, zweitens, ob die Artikel nach Wareneingang die Qualitätskontrolle bestehen, und drittens, wie viel Zeit vergehen wird, bis die Artikel wieder verkauft werden können.
Diese Prognoseprobleme eignen sich durchaus für eine hochspezifische, strukturierte Analyse. Tatsächlich wird die maximale Anzahl von Artikeln, die zu jedem Zeitpunkt zurückgesendet werden können, durch das Volumen der jüngsten Sendungen begrenzt. Eine Begrenzung von Randereignissen ist aus supply chain-Perspektive von größter Bedeutung. Außerdem ist es, wenn man mit der Situation „3 Größen bestellt, 2 Größen zurückgeschickt“ konfrontiert ist, möglich, mit großer Sicherheit den Anteil der Verbraucherbestellungen vorauszuberechnen, der zurückgesendet wird.
Leasingunternehmen
Leasingunternehmen, wie z. B. Autoleasingfirmen oder Büromöbel-Leasingunternehmen, stehen vor Situationen, die teilweise vergleichbar mit denen von MROs sind, jedoch nicht ganz. Tatsächlich hängt der angemessene Lagerbestand nicht nur von der zukünftigen Nachfrage ab, sondern auch von den zukünftigen Halteraten, da der Bestand am Ende des Leasings an das Leasingunternehmen zurückfließt. Da das Leasingunternehmen nicht die volle Kontrolle über die Leasingdauer hat, müssen diese Dauern prognostiziert werden, um den Lagerbestand zu optimieren. Die Dauer dieser Halteperioden und deren Auswirkung auf den Lagerbestand können unter dem Aspekt der regulären Lieferzeiten analysiert und prognostiziert werden.
Allerdings haben die meisten Leasingunternehmen ein gewisses Maß an Kontrolle über die Halteperiode durch ihre Preisgestaltung und die Sonderangebote, die sie ihren Kunden gewähren können. Ähnlich wie ein Einzelhändler, der die Nachfrage für ein Produkt durch eine Promotion ankurbeln kann, kann ein Leasingunternehmen seine Halteperiode verlängern, indem es günstigere Konditionen anbietet. Somit ist in Leasing-Situationen die Preisgestaltung in hohem Maße mit der Lieferzeitanalyse verknüpft.
Lieferzeit-Antipatterns
Der Begriff „antipatterns“ bezieht sich auf Praktiken, Prozesse oder Werkzeuge, die als Lösungen gedacht sind, jedoch nicht die erwarteten Ergebnisse liefern. In supply chain sind Lieferzeiten anfällig für eine Reihe von antipatterns, die wir in diesem Abschnitt betrachten.
Unterschätzung
Lieferzeiten sind einer der Hauptgründe, warum Planung und Prognose überhaupt eine Rolle im supply chain management spielen. Dennoch erhalten Lieferzeiten – als ein Phänomen, das modelliert und geformt werden soll – in der Regel nur einen winzigen Bruchteil der Aufmerksamkeit, die anderen konkurrierenden Phänomenen, wie der Nachfrage, zukommt. Es gibt mehrere Institute, die sich der Nachfrageprognose widmen, aber keines, das sich der Lieferzeitprognose widmet. Dieses enorme Ungleichgewicht in der Aufteilung der Bemühungen führt häufig zu Situationen, in denen quantitative Analysen bis auf das Gramm genau auf der Nachfrageseite durchgeführt werden, um sie anschließend auf die nächste Tonne – auf der Lieferzeitseite – zu runden. Die meisten Branchen erfordern, dass Lieferzeiten erstklassige Bürger in der supply chain optimization sind – gleichgestellt mit der Nachfrage – sowohl in Bezug auf Prozesse als auch auf Werkzeuge.
Überauslastung
In den meisten supply chains verbringt der Großteil des Lagerbestands – einschließlich Rohstoffen und Halbfertigwaren – die meiste Zeit unbewegt und wartet auf den nächsten Arbeitsschritt. An jedem einzelnen Schritt der supply chain bilden sich Warteschlangen, und jede Warteschlange bringt ihre eigene Wartezeit mit sich. Je näher jedoch die Auslastung eines Vermögenswerts an 100% liegt, desto näher kommt die Wartezeit in der Schlange der Unendlichkeit. Somit ist die Auslastungsrate ein Kompromiss zwischen der Abschreibung des Vermögenswerts selbst und den damit verbundenen Lieferzeiten. Dieser Kompromiss besteht darin, die abnehmenden Erträge höherer Auslastungsraten gegenüber den exponentiell wachsenden Wartezeiten abzuwägen.
Blind agieren
Die Verbesserung der Lieferzeit beginnt in der Regel damit, die Schuld richtig dem spezifischen Teil des Prozesses zuzuweisen, der die größte vermeidbare Verzögerung verursacht. Allerdings können die Messungen der Lieferzeit selbst irreführend sein. Beispielsweise, wenn man die Lieferzeit eines Lieferanten misst und die gelieferten Paletten häufig unbearbeitet darauf warten, elektronisch an einem Dock erfasst zu werden, kann dies die Lieferzeit des Lieferanten deutlich aufblähen, während der fehlerhafte Prozess in der Annahme liegt. Diese Probleme können typischerweise nicht durch Datenanalyse behoben werden, sondern erfordern Vor-Ort-Beobachtungen, um zu verstehen, ob der Datenerfassungsprozess vertrauenswürdig ist oder nicht. Auch die bloße Erfassung elektronischer „Tops“, da dies eine zusätzliche Arbeitsbelastung für das Personal darstellt, kann die Gesamtlieferzeit erhöhen – was den ursprünglichen Zweck unterläuft.
Entstehendes LIFO
Die Verarbeitung von Aufträgen oder Bestellungen nach dem FIFO-Prinzip (first in, first out) ist nahezu immer eine Voraussetzung, um eine angemessene Servicequalität zu gewährleisten. Tatsächlich führen Verletzungen des FIFO-Prinzips unregelmäßig zu extrem langen Lieferzeiten. Allerdings neigt sich auf physikalischer Ebene in vielen Situationen natürlich eine LIFO (last in, first out) Abfolge ein, und es bedarf spezifischer Anstrengungen, um diese entstehenden LIFO-Situationen zu verhindern. Zum Beispiel:
- Jeder eingehende Auftrag (Kommissionierung, Produktion, Reparatur etc.) wird automatisch als „Auftragsblatt“ ausgedruckt. Alle eingehenden Auftragsblätter werden in einem Fach abgelegt. Aufgrund des Druckprozesses liegen die zuletzt eingegangenen Aufträge jedoch oben auf dem Stapel, was die Bediener in Richtung LIFO lenkt.
- Wenn ein Förderband zu kurz ist, neigen die Waren dazu, überzulaufen und am Anfang des Förderbands auf den Boden gelegt zu werden. Schnell entsteht ein Haufen von Waren, wobei die Artikel, die am längsten vorhanden sind, sich zufällig am Boden des Stapels befinden. Das Abnehmen der Waren erfolgt nach dem LIFO-Prinzip.
- Wenn Kisten oder Paletten an einem Dock durch einen Zustrom von Transporteuren entladen werden, neigen die frisch angelieferten Waren – sofern das Dock nicht nach jeder Entladeoperation geräumt wird – dazu, vor oder oben auf den bereits vorhandenen platziert zu werden, was später beim Verarbeiten zu einem LIFO-Effekt führt.
Anmerkungen
-
Ab 2020 gibt es nur drei Länder, die RAM (Random Access Memory) herstellen, eine grundlegende Hardwarekomponente moderner Computer. Außerdem gibt es drei Länder, die für nahezu 90% der weltweiten Reserven und Produktion von Lithium verantwortlich sind, einem wesentlichen Element moderner Batterien. ↩︎