リードタイム
リードタイムとは、プロセスの開始と完了の間に生じる遅延のことです。サプライチェーンでは、商品が購入、加工、またはサービス提供される際に、通常は日数で測定されるリードタイムが関与します。計画の観点から、在庫の補充など、意図した効果を達成するためには、多くのルーチンな意思決定を前もって行う必要があるため、リードタイムは重要な要素となります。また、リードタイムの存在から需要予測の必要性が生じることも多いです。
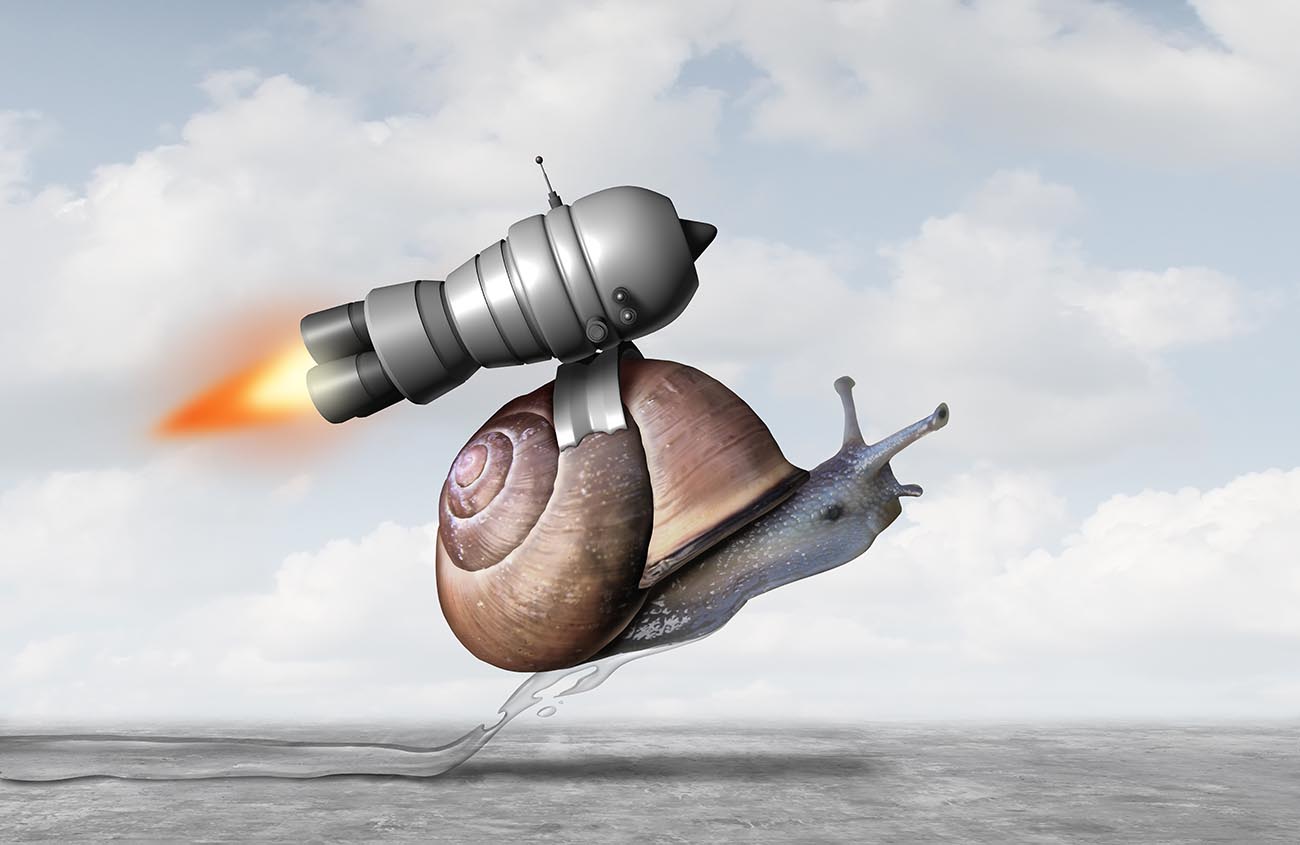
リードタイムの原因と影響
リードタイムは、サプライチェーンの運営方法や、必要な運転資本、資本収益率(ROCE)などの財務要素に大きな影響を与えます。実際、リードタイムが長いということは、原材料や製品の購入、場合によっては加工、再販までを含む在庫サイクルの完了により長い時間を要することを意味します。
リードタイムが長いと、実際の在庫数量が低く見えても、実質的にはより高い在庫の_initiative_(約束)が伴います。例えば、ヨーロッパの企業がアジアからコンテナによる商品配送を注文した場合、発注が出された時点から、その企業は商品を販売または消費することを約束した状態になります。しかし、この場合、ヨーロッパの在庫レベルがその約束を反映するまでには通常6週間以上かかります。
さらに、リードタイムが長いと予測への依存度が高まります。前述の例に戻ると、企業は現時点の需要に基づいて単に発注するだけでは不十分であり、注文が届く頃には状況が変化しているでしょう。現在の在庫レベルは継続的な消費によりさらに低下し、需要も季節性などの影響で変わっている可能性があります。
リードタイムは、企業が達成可能な最大の機敏性の下限を示します。経験則として、市場状況が急激に変わった場合でも、企業はおよそリードタイムの期間、過去の決定に縛られる傾向があります。これらの影響を緩和するための手段はいくつかあり、まずはサプライヤーとの契約条件が考えられます。しかし、根本的なリスクはほとんど排除できず、単にサプライチェーン内に移されるだけです。
リードタイムが長いことによる多くの悪影響を考えると、なぜ企業が(主観的に)長いと思われるリードタイムを選択するのか不思議に思われるかもしれません。実際、さまざまな経済的要因が、長いリードタイムに有利に働いています。
専門化がリードタイムの長期化を促しています。一部の国では、現地で再現するのが難しい、または費用がかかる非常にユニークな産業1が存在します。このような集中産業は、歴史的に輸送が容易な高価値素材によって主に発展しました。しかし、航空機が24時間以内に世界中のどこにでも到達できたとしても、海外サプライヤーの場合、通関手続きやその他のプロセスが実際のリードタイムを大幅に延ばす傾向があります。
スケールメリットもまた、リードタイムを長くする方向に働いています。ロットサイズを増やす(しばしばMOQとして具現化される)ことで、製造業者や運送業者はコストを下げることができます。しかし、ロット数量が大きくなると、ロットの回数も減少し、その頻度も低くなります(他の条件がすべて等しい場合、特に需要が)。それにもかかわらず、すべての産業が同じようにスケールメリットの影響を受けるわけではなく、適用技術に応じて限界が現れることがあります。
高いパーセンタイル値の低減
リードタイムは平均的な期間を短縮することで改善できるものの、実際に最も重視されるのは、最悪のケース、つまり最も長い状況の改善です。サプライチェーンでは、影響が金銭的な規模で測定される場合、最大の問題は分布の尾部に集中し、わずかな変動ではなく、予期せぬほど長いリードタイムがストックアウトや生産の中断を引き起こします。
最悪ケースを評価する最も簡単な方法の一つは、パーセンタイル測定を用いることです。例えば、あるサプライヤーの95パーセンタイルのリードタイムが7日であるとすれば、そのサプライヤーに渡される注文の95%が7日未満で配達されることを意味します。このような「高い」パーセンタイル値、すなわち100%に近い値は、平均リードタイムと大きく乖離する可能性があります。実際、同じサプライヤーでも平均配達日数が2日である場合、高いパーセンタイル値の推定の3分の1以下となることがあります。
これらのサービス品質の問題を回避するために、サプライチェーン内のすべての在庫バッファは、用いられる手法に関係なく、リードタイムの平均ではなく、ある_高いパーセンタイル値_に基づいて線形に増加する傾向があります。実際、在庫バッファはサプライチェーンの条件変動に対応するために存在しており、予期せぬ変動の主な要因は、需要の変動とリードタイムの変動です。
リードタイムの多様性
サプライヤーからの元の発注からクライアントへの配送までの全体のリードタイムは、通常、数多く、場合によっては数十の中間ステップに分解することができます。リードタイムの値やその変動性を低減するためには、この全体のリードタイムを、分析し改善しやすい主要なサブコンポーネントに分解することが効果的です。
例えば、海外サプライヤーから商品を流通させる卸売業者は、以下のようなリードタイムに直面する場合があります:
- 卸売業者自身の週次購入プロセスによる発注リードタイム。
- サプライヤーによって課せられるMOQによる機会リードタイム。
- 発注を履行するためにサプライヤーが必要とする製造リードタイム。
- 運送業者により必要とされる輸送リードタイム。
- 通関手続きを行うための事務手続きリードタイム。
- 卸売業者による在庫管理および品質管理のための受け入れリードタイム。
- 流通センターがクライアントの注文を履行するために必要とする発送リードタイム。
- 輸送業者がクライアントへの配送を行うために必要とするラストマイル配送リードタイム。
各オペレーションについては、通常、平均遅延と遅延の分散の両方を低減することが望まれます。
これらすべてのオペレーションを追跡することは多くの事務作業を伴いますが、バーコードやRFIDなどの最新ITシステムによって大幅に軽減できます。電子記録は、関係する企業のITシステムに通常保管されます。これらのシステムは、リードタイムの最適化を超えて、商品のトレーサビリティを保証し、在庫の縮小をある程度防ぎます。
1990年代後半までは、これらの記録の保管と処理には多大な計算資源が必要であったため、サプライチェーン内の物理的商品の流れから生成される細かな記録を取得、さらには保存することは常に経済的に実現可能というわけではありませんでした。しかし、2010年代初頭以降、データ保管および計算のコストは、物理的フローが関与する場合に計算資源自体がほとんど問題とならないほど低下しました。それでもなお、特にシステム統合などのITコストが、これらの電子記録の取得を妨げる可能性があります。
リードタイムを改善し、上述のように通常その高いパーセンタイル値を低減するためには、測定が必要です。詳細なリードタイム測定は、根本原因分析において非常に有用です。実際、各オペレーションはステップごとに大きく異なるため、もたらされる改善の内容も大きく異なる傾向があります。
注文リードタイム
注文リードタイムは通常、顧客の注文と商品の配送の間に経過する時間を指します。この期間は、一般の人々(サプライチェーン-サイエンティストとは異なり)に最も馴染みのあるリードタイムの形態として知られています。B2Cのeコマース以外の多くの業界では、注文リードタイムはサービスの_品質_に密接に関連しており、特にストックアウトが異常に長い注文リードタイムを引き起こす主要因となります。
注文リードタイムの改善における課題は、単にリードタイムそのものを短縮することではなく、顧客に対して配送日の適切な_期待値_を設定することにあります。特に、いくつかの大手eコマース企業は、過去10年以上にわたり、遅延の上限となる可能性のあるパーセンタイル予測の推定値を共有する手法を採用してきました。遅延推定値のバイアスは、商品が期限内に配送されない状況の頻度を最小限に抑えるために、あえて導入されています。
リードタイムの予測
将来のリードタイムを適切に予測することは、サプライチェーンの最適化に不可欠な要素です。需要と同様に、リードタイムも既存の履歴データを活用することで予測されるべきものです。
リードタイム予測は(まだ)「需要」計画チームの間で一般的な慣行ではありませんが、需要に適用されるほとんどの周期性はリードタイムにも見られます。例えば、リードタイムには季節性、月内の日、曜日の影響があり、時間の経過とともに変化します。例えば、サプライヤーはリードタイムを短縮するために自社プロセスを見直す場合もあれば、コスト削減のために延長する場合もあります。また、中国の旧正月のように、アジアの多くの工場が閉鎖される時期には、準季節性の影響でリードタイムが周期的に膨らむこともあります。
確率的予測はリードタイムに対して推奨されるべきです。前述のとおり、リードタイムの経済的影響は高いパーセンタイル値に起因しており、コストや問題が分布の尾部に集中するためです。ただし、正規分布(ガウス分布)はリードタイムの予測には使用すべきではありません。経験則として、リードタイムは_決して_正規分布せず、そのようなモデルに依存すると高いパーセンタイル値が大幅に過小評価され、結果として継続的なサービス問題を引き起こす原因となります。
リードタイムは、基礎となる物理システムを反映した多峰性分布としてより適切にモデル化することができます。例えば、生産ラインの起動時には、生産リードタイムは非常に予測可能ですが、原材料の一つが不足している場合、製造リードタイムが大幅に延びる可能性があります。したがって、確率分布の実用的なモデル化には、通常、離散分布とパラメトリック分布の混合が含まれます。
リードタイムの確率的予測は、各内部フェーズごとに離散的な確率変数を生成すると期待されます。これらの内部フェーズが統計的に独立していると仮定することは合理的であり(例:通関による遅延は製造遅延と完全に独立している)、その場合、確率変数は標準的に加算され、これは基礎分布に対する_畳み込み_操作を意味します。
制御されたモダリティ
適切なリードタイムの確率的予測モデルは通常多峰性ですが、受動的な観測とは異なり、ある程度の制御が働く場合には特定のモダリティに対して個別の対応が必要となります。例えば、サプライヤーに対して航空便または海上便を依頼できる場合、予測の観点からはこれら2つの輸送モードを一括りにすべきではありません。各輸送モードには固有の変動性があるため、別々の予測が必要となります。
需要連動
需要が急増すると生産能力が制限され、製造リードタイムも増加する傾向にあります。この需要とリードタイムの連動は、追加の購入や製造注文によって需要急増を緩和する企業の能力を減少させ、結果としてサービス品質に悪影響を及ぼします。したがって、必要な在庫バッファが2つの要因に依存することから、需要とリードタイムの共同予測モデルを構築することが有益な場合があります。
しかし、作業キューの再編成に十分な柔軟性を持つ製造ユニットでは、観察されるリードタイムは各作業に与えられる優先順位に大きく依存します。したがって、適切なリードタイム予測モデルは、キューイングの側面を考慮すべきであり、任意の優先順位の選択によりリードタイムが大きく変動する可能性があることを反映する必要があります。この追加の制御を活用することで、需要急増の影響を緩和することが可能です。
リード需要
リード需要は、リードタイム期間中にサービスを提供すべき商品の数量を示します。この値は、ストックアウトを回避するために、手元在庫と発注中在庫の合計である総在庫が常にリード需要以上でなければならないため、特に重要です。総在庫がリード需要を下回ると、必ずストックアウトが発生します。
将来の需要とリードタイムの両方について確率的予測が可能であると仮定すると、リード需要の(高い)パーセンタイル推定値を次式で計算することが可能になります:
ここで:
- $${0≤τ≤1}$$ はパーセンタイル推定の対象です
- $${y}$$ は時間とともに変動する需要です
- $${L}$$ はリードタイムです
- $${Qτ[..]}$$ は内部の実数値関数のパーセンタイルです
- $${Ω}$$ は可能な結果の集合です
- $${t}$$ は時間を示し、1は最初の将来期間です
- $${y_ω}$$ は結果 $${ω}$$ に関連付けられた需要です
- $${L_ω}$$ は結果 $${ω}$$ に関連付けられたリードタイムです
このリード需要の分位点推定は、目標とするサービスレベルを維持する際に重要です。単一SKU、単一サプライヤー、MOQなしの在庫モデルを仮定すると、任意の時点で補充される数量は次の数式で定義できます:
以下:
- $${OnHand}$$ は現在手元にある在庫です
- $${OnOrder}$$ は発注済みの在庫です
この数式は、品切れ時に需要が失われないという前提を暗黙に仮定しています。しかし、この前提は、たとえば消費者小売業のように、顧客が単に消費の先延ばしではなく、購入を放棄したり代替品や競合他社に流れる場合が多い状況では合理的ではありません。この前提を取り除くためには、失われた需要の影響を明示的にモデル化する必要があります。特に需要が非常に季節的な場合、季節ピーク後に利用可能となった商品が長期間売れ残ったり使われなかったりする可能性があるため、これは非常に重要です。
リードタイム駆動のフィードバックループ
リードタイムは、前節で詳述したように補充を計算するための入力要因と見なすことができます。しかしながら、リードタイム自体は発注(または生産)スケジュールに依存します。さらに、このスケジュールは、目標とするEOQ(経済的発注量)、MOQ(最小発注数量)、あるいは規定の生産バッチサイズを達成するために、規模の経済を狙ったものとなるのが一般的です。
このように、サプライチェーンの実務者は、今日行うべき(補充および発注の)決定と、その決定が将来再び実施される時点との間にフィードバックループが存在する状況に頻繁に直面します。言い換えれば、今日発注する数量は次回の再発注日時に依存し、再発注日時が遅ければ遅いほどより多くの数量が必要となります。しかし、次回の再発注日時も、現在の発注数量の影響を受けるため、大量に即時発注すれば次回の再発注は後ろ倒しになるのです。
このフィードバックループを明示的にモデル化し数値的に最適化することは容易ではないため、サプライチェーンの実務者は、目標とする発注サイズ(EOQ、MOQ、バッチサイズなど)に合わせて、おおまかなスケジュール(例えば週次または月次の発注)を設定することが多いです。そして、このスケジュールを固定的なものと仮定し、再発注数量のみを必要に応じて変動させます。しかし、この固定スケジュールのアプローチは、サプライチェーンが持つすべての自由度を活用できないため、本来的に非効率性を内包しています。
このフィードバックループの観点に対応するより優れた数値的解法が考案される可能性があります。これらの解法に関わるアルゴリズムは通常、強化学習の枠組みに該当します。ただし、これらのアルゴリズムの詳細な解説は本書の範囲外です。
業界固有の問題
リードタイムは多様であり、適切な視点も対象とする業界によって異なります。以下の節では、リードタイムに関して顕著な特有の課題を呈するいくつかの業界について概説します。
生鮮食品の賞味期限
生鮮食品は非常に劣化しやすいため、商品の賞味期限は短くなります。商品の市場価値をできるだけ維持するためには、リードタイムの短縮が通常、非常に重要です。したがって、リードタイムに影響を与えるパッケージングや輸送などの選択肢を検討する際、これらの選択肢はサービス品質のみならず、サプライチェーン全体で期待される収益や発生する廃棄量にも影響を及ぼします。
さらに、ブランドや流通業者は、リードタイムと賞味期限のトレードオフが異なる複数の調達オプションに直面します。たとえば、ブランドが生産者から直接購入する場合、リードタイムは長いものの、受領した商品の賞味期限は長くなります。一方、卸売業者から購入する場合は、リードタイムは短いですが、受け取る商品の賞味期限が短くなります。このような状況では、適切なサプライチェーン最適化により両者のバランスを取る必要があり、そのためにはそれぞれのリードタイムと賞味期限の予測分析が求められます。
MROのターンアラウンドタイム(TAT)
MRO(メンテナンス・修理・オーバーホール)は修理可能な部品を管理します。部品の交換が行われる際、使用可能な部品がすぐに利用できる状態でなければならず、取り外された部品は修理が完了するまで使用不能となります。部品交換の要求から、修理済みの使用可能な部品が再び利用できるようになるまでの全体の遅延をターンアラウンドタイムと呼びます。
MROが保有する部品在庫はTATに直接依存します。実際、もしMROが理論上、使用不能な部品を即座に修理できる能力を有していれば、在庫は不要となるでしょう。そのため、MROにおいては、需要予測よりもリードタイムの予測と最適化がさらに重要となります。
TAT分析が強調される理由として、_予定外修理_の性質が挙げられます。これらは、基礎的な物理プロセスに伴うある程度の回避不可能な不確実性を伴う故障に起因するためであり、もし問題に事前対応する手段があれば、診断によりそれらの作業は_定期修理_に切り替わるはずです。
電子商取引におけるリバースロジスティクス
ほとんどの国の消費者向け電子商取引では、消費者が受け取った商品を気に入らなかった場合に返品できる制度が現代では一般的です。しかし、消費者の返品率は国によって大きく異なり、主に文化的な理由によるものです。たとえば、ファストファッションの電子商取引では、ドイツの消費者は通常、返品率が50%を超える傾向にあります。これらの高い返品率は、複数のサイズを注文し、一部を除いてすべて返品するという習慣に部分的に起因しています。
返品率が高い場合、オンライン小売業者は、在庫のかなりの部分が実際に逆流してくることを見越さなければなりません。さもなければ、補充発注後に商品が戻ってくることで、体系的に在庫過剰に陥るリスクがあります。しかし、将来の返品に関しては、第一に商品が返品されるか否か、第二に返品された商品が受領後に品質検査に合格するかどうか、第三に再販可能になるまでに経過する時間という三つの不確実性が存在します。
これらの予測問題は、非常に特定の構造化された分析に適しています。実際、任意の時点で返品可能な商品の最大数は、直近の出荷量によって制限されます。テールイベントに上限を設けることは、サプライチェーンの観点から極めて重要です。また、“3サイズ注文、2サイズ返品”の状況では、返品される消費者注文の割合を高い確実性で予測することが可能です。
リース事業
車のリース会社やオフィス家具のリース会社などのリース事業は、MROの場合と似た側面を持つものの、完全に一致するわけではありません。適切な在庫水準は、将来の需要だけでなく、リース期間終了時に在庫がリース事業に返却される将来の保持率にも依存します。リース会社はリース期間を完全には管理できないため、在庫最適化のためにはその期間を予測する必要があります。これらの保持期間の長さと在庫への影響は、通常のリードタイムの観点から分析・予測することができます。
しかしながら、ほとんどのリース事業は、価格設定や顧客への特別オファーを通じて、保持期間をある程度コントロールすることが可能です。プロモーションによって商品の需要を高める小売業者と同様に、リース事業もより有利な条件を提示することで保持期間を延長することができます。したがって、リースの状況では、価格分析は大いにリードタイム分析と絡み合っています。
リードタイムのアンチパターン
「アンチパターン」とは、解決策として意図されたにもかかわらず、期待される結果を達成できない慣行、プロセス、またはツールを指します。サプライチェーンにおいて、リードタイムは本節で検討する一連のアンチパターンに陥りやすいです。
過小評価
リードタイムは、サプライチェーン管理において計画や予測が重要である根本的な理由のひとつです。しかし、モデル化・管理対象としてのリードタイムは、通常、需要など他の現象に比べてわずかな注目しか集めません。_需要予測_に専念する機関は多数存在する一方で、_リードタイム予測_に特化した機関は存在しません。このような努力配分の大きな不均衡は、需要側ではグラム単位まで定量分析が行われ、後にリードタイム側では最も近いトン単位に丸められるという状況を頻繁に引き起こします。ほとんどの業界では、リードタイムを需要と同等にサプライチェーン最適化の一級市民として扱う必要があり、プロセス面、ツール面の両方でその位置付けが求められます。
過剰活用
ほとんどのサプライチェーンでは、原材料や半製品を含む在庫の大部分が、次の作業を待つ間、ほとんど動かず留まっています。サプライチェーンの各段階で処理待ちのキューが形成され、それぞれに固有の待機時間が存在します。しかし、いかなる資産の利用率も100%に近づくにつれて、その待機時間は無限大に近づきます。すなわち、資産の利用率は、資産自体の償却と関係するリードタイムとの間のトレードオフとなるのです。このトレードオフは、利用率向上による収益の減少効果と、指数関数的に増加する待機時間とのバランスを取ることに他なりません。
盲目的な運用
リードタイムの改善は通常、避け可能な最大の遅延を引き起こしているプロセス部分に原因を求めることから始まります。しかし、リードタイムの測定値自体が誤解を招くことがあります。たとえばサプライヤーのリードタイムを測定する場合、納品されたパレットがドックで電子受領待ちのために未処理のまま置かれていると、その測定値は本来問題となる受領プロセスを反映せず、サプライヤーのリードタイムを大幅に膨らませる恐れがあります。これらの問題は通常、データ-抽出-パイプラインによるデータ分析だけでは対処できず、データ取得プロセスの信頼性を判断するために現地での観察が必要となります。また、電子「トップ」の取得自体がスタッフに追加の作業負荷を課すため、全体のリードタイムを増加させ、元々の目的を損なう結果となる場合もあります。
自然発生するLIFO
合理的なサービス品質を確保するためには、ほぼ常にFIFO(先入先出)の順序でジョブやオーダーを処理する必要があります。実際、FIFOの原則が破られると、突発的に非常に長いリードタイムが発生します。しかし、物理的なプロセスの観点からは、LIFO(後入先出)の順序が多くの状況で自然に現れる傾向があり、これらの自然発生するLIFO状況を防ぐためには特別な対策が必要です。例えば:
- すべての受注ジョブ(ピッキング、生産、修理など)は自動的に「ジョブシート」として印刷され、すべてのジョブシートは箱に入って保管されます。しかし、印刷プロセスの性質上、最新のジョブが積み重ねの上部に位置し、オペレーターはLIFOの順序で処理する傾向に誘導されます。
- コンベアが短すぎる場合、商品がコンベアからあふれ、始端付近の地面に置かれることがあります。すると、商品の山がすぐに形成され、最も古くからある商品が山の下部に位置します。その後、商品の荷降ろしはLIFOの順序に従って行われます。
- 箱やパレットが運搬車両によってドックで荷卸しされる際、各荷卸し後にドックが一掃されないと、新たに到着した商品は前方または既存の商品群の上に置かれ、結果的に後の処理時にLIFOの順序となります。
注釈
-
2020年現在、現代コンピュータの基本的ハードウェアコンポーネントであるRAM(ランダムアクセスメモリ)を生産している国は3カ国のみです。また、現代バッテリーの重要な要素であるリチウムの世界埋蔵量および生産量の約90%を占める国も3カ国存在します. ↩︎