Kanban(在庫管理)
The Kanban method (billboard in Japanese), like Lean Manufacturing takes its roots from the Japanese automotive manufacturer Toyota. It was implemented to improve manufacturing efficiency and reduce waste by providing a simple and visual material replenishment process, so that every step of the production process would get just enough in a timely manner to operate smoothly, without stockpiling raw materials or components. Basically, each time a certain quantity of material is consumed - immediately visible as an empty box or an empty shelf -, a visual signal (typically a card) is sent to trigger replenishment for the same quantity. From here, the Kanban system gained influence in several fields, in particular in software development with the Agile management philosophy, or in supply chain management, as a simple method to avoid overstocks.
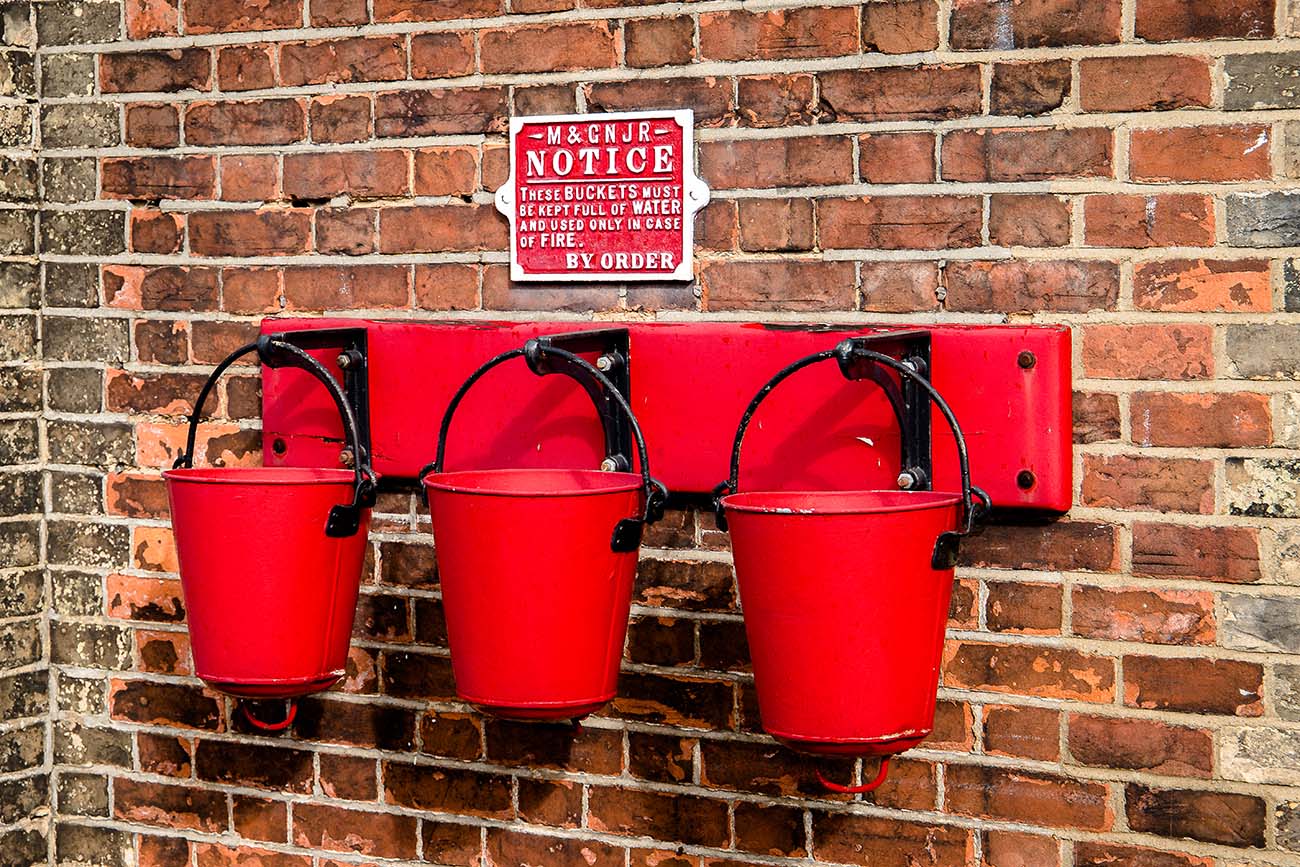
Kanbanの起源と製造以外での進化
1940年代~1950年代に生まれたKanbanは、第二次世界大戦後、コンピューターやデジタル技術がほとんど存在しなかった環境下で、紙のカードや箱・ビンのみというシンプルでありながらエレガントなシステムにより、製造現場の合理化に大きく貢献しました。
廃棄物、すなわち工場や店舗での不要在庫を削減するため、トヨタの技術者たちは、補充が実際の消費に直接連動するシステムを考案しました。彼らはプッシュ方式ではなくプル方式を採用しました。この二つには根本的な対立があります。伝統的には、商品の生産は需要予測(通常、需要予測により具体化される)に基づき、あらかじめ製造され、その後プッシュされ市場に供給されます。一方、プル方式ではシステムが需要駆動型となり、受注生産が行われます。生産と補充は、需要を予測するのではなく、必要になったときにのみ実施されるのです。
Kanbanシステムの実装方法はいくつか存在します。その中でも最も単純な形は、2ビン方式または3ビン方式です。例えば、2ビン方式を採用する倉庫では、2つの箱が収まるサイズの棚が設置され、各箱には通常、アイテムに関する情報(品番、バーコード、数量など)を含んだKanbanカードが入っています。箱が空になると、その箱は後で再利用するために取り置かれ、Kanbanカードは目立つ場所(通常は列の端、専用のテーブルや容器)に移動されます。2つ目の箱が使用されている間、表示されているKanbanカードは担当者によって回収され、倉庫から満杯の箱と交換されます。理想的には、担当者が補充品を持ち込む際、もう一方の箱は完全に使い切られているのではなく、残量が僅かである状態になっています。考え方はシンプルです:メインの箱と予備の箱があり、予備が使用され始めたらメインを補充する、という流れです。実際、予備の箱は単なる安全在庫にすぎません。
工場で実施される3ビン方式では、1つのビン(箱)の資材が生産用に工場現場に置かれ、1つは工場内倉庫に、もう1つはサプライヤーの施設に配置されます。最初のビンの内容が生産プロセスで使い切られると、倉庫にある満杯のビンの内容を引き出すための信号が直ちに送られます。次に、空になったビンを保持している工場内倉庫が、サプライヤーが管理する第3のビンの内容を引き出し、その後サプライヤーがそれを再充填します。在庫は消費され枯渇した時のみ補充されるのです。空のビンは、あらかじめ定められた数量で追加の資材を手配するKanbanトリガーを発します。再度言えば、工場内倉庫レベルのビン以上の不要在庫は抱えず、プロセスはビンの円滑な交換と、サプライヤーが予定外の遅延なく補充注文を処理できることに依存しています。
リーンの概念そのものと同様、カードや信号によって生産サイクル全体に視認性をもたらし、不要な蓄積を回避するという考え方により、Kanbanは製造業の枠を超えて発展しました。ソフトウェア開発やマーケティングにおいて、論理的工程を具現化するワークフロー管理手法として広く採用されています。タスクボードに「To-do / In progress / Done」といった3つのカラムを配置し、実装すべきプロジェクトの各部分をカードで示し、担当チームメンバーに割り当てるだけというシンプルな形もあり得ます。Trelloのようなツールは、プロジェクト管理に役立つ実用的で使いやすいKanbanシステムを提供します。
ソフトウェア開発では、アジャイルマネジメントを取り入れることでこのプロセスがさらに洗練されました。ボードには、Build / Test / Completeといったバケットが配置されます。ユーザーのフィードバックに基づき開発すべき機能など、優先順位のつけられたタスクのリストが作成され、任意の開発者がそのリストからカードを取って特定の機能を開発します。開発された機能は、リリース前にテスト段階に入ります。さらに各バケットには、チームの能力に合わせた作業中上限(Work In Progressリミット)が設定され、具体的にはバケットに置けるカードの最大数が定められています。このようなボードの利点は、チーム全体がタスクを一目で把握でき、潜在的なボトルネック(例:Testingバケットでのカードの蓄積)を迅速に特定でき、ワークフローの効率(扱われるカード数、各段階間の進行速度など)を把握できる点にあります。
長所と短所
長所
そのシンプルさとデザインの美しさから、Kanbanにはこの手法が広く普及した理由を説明する多くの利点があります。まず、システム自体が(少なくともシンプルなKanbanは)理解しやすく実装しやすいため、経営陣やチーム双方に受け入れられ、変革管理の難易度を低減します。また、柔軟かつ多用途であり、各企業の特性や既存プロセスに容易に適合させることが可能です。各企業は、自社に適したビンやバケット、論理的な工程を定義すればよく、Kanbanシステムに基づいたシンプルな分析やレポートで、システムの効率や各工程の課題を評価することもできます。
Kanbanが非常に理解されやすい主な理由の一つは、視覚的信号(カード、空白、箱など)の活用にあります。理想的なKanbanシステムでは、すべてが一目で分かるよう設計されています。空の箱は目立つ場所に配置され、特定サイズのテーブルは不良品を表示するために設置され、テーブルが満杯になるとこれ以上品を置けなくなるなどの仕組みが取られています。カードは通常、明るい色で大きなフォントが使用され、レシピや一連の作業手順など、シンプルかつ必要な情報を一か所にまとめる追加情報が含まれることもあります。主な考え方は、状況(補充の必要性、ボトルネック、不良品の蓄積など)を一目で判断し、ほぼ自動的かつ日常的に適切な対応を取ることにあります。
さらに、カードなどのシンプルな視覚的手がかりに依存することで、KanbanはITなしでも機能します。今日では、非物質化されたカードを用い、ERPなどに直接統合されたデジタル版(e-Kanban)も存在します。これらには利点があり、手作業のミスを減らすことも可能ですが、Kanbanの大きな強みは、コンピュータのない環境でも機能するよう設計されている点にあります。組織は、コンピュータ未使用の労働者でも、ITにまったく依存せずKanbanを実装できるのです(そのため、端末の使用などのトレーニングも不要です)。
Kanbanは、はっきりした信号で常に同じ即時の行動を反復的かつ明確に促す設計となっており、特にITが関与しなければ、リアルタイムシステムと言えます。一度システムが整えば、行動は自動化され、チーム内で必要なコミュニケーションはほとんどなくなります。これは、他の多くの代替手段が(検証、承認等の意思決定プロセスに伴う)遅延を招くのと対照的です。
これらの特徴により、Kanbanは堅牢なシステムとなり、ミスや誤解の余地をほとんど残しません。Kanbanのプル方式は、製造や供給チェーン管理においてさらにその堅牢性を高めます。実際の消費に基づくプルはリスクが低く、補充が予測(本質的に完全ではない)ではなく事実に基づいて行われるため、Kanbanの実装は通常、在庫削減、コスト削減、保管スペースの増加、死蔵在庫の減少などに繋がるのです。これがリーンプロセスの目的です。
留意点
適切なKanbanシステムの実装には、一連のルールが伴い、これを遵守しなければKanbanはすぐに非効率または無意味になってしまいます。ここでは、トヨタの6原則の詳細に立ち入らず、Kanban導入を検討する際の注意点を挙げます。
優れたKanbanシステムの鍵は、厳格な監視とルールの遵守にあります。Kanbanカードは適切に配置され、行動は正確かつ迅速に実施される必要があります。システムの強みは、行動の自動化—例えば、不良部品は常に同じ容器の同じ場所に配置され、補充が必要であることを示すカードは必ず同じ方法で倉庫の列末に配置される—にあります。もし行動が適切に行われず、一部の工程が省略または変更されると、よく機能していた仕組みがすぐに狂い、ドミノ倒しのような連鎖反応を引き起こす可能性があります。すべてを常に監視し、担当者は正確な訓練を受ける必要があります。e-kanbanでは、これが精度やITシステム、特に電子的な在庫正確性の信頼性に大きな負荷をかけます。e-kanbanは手作業のミスを避けるために設計されましたが、データ入力の誤りやシステムのバグが起こることもあります…
Kanbanは、多くの状況に適応できる柔軟性を持っていますが、一度完全実装されビンのサイズ調整などが行われると、システムは非常に厳格になります。実際、一度実装され再度挑戦されない限り、Kanbanは柔軟性を失います。例えば、一度設定されると、ユーザーが特定の状況に合わせてビンや箱の数量を変更することは想定されていません。これは適応性の欠如というリスクを孕みます。極めて安定した環境で使用しない限り、追加調整が必要になる可能性があるため、Kanbanシステムは定期的な再評価が求められます。
短所
Kanbanはすべての状況に適しているわけではありません。小さなディテールに問題が潜みがちです。まず、Kanbanのシンプルさは隠れた複雑さを覆い隠すことがあります。2ビン方式は一見シンプルに見えますが、生産プロセスの中断や供給チェーンの詰まりを防ぎながら、適切なサイズに設定するのは難しいものです。多くの組織は、Kanbanを採用することで従来のプッシュ方式に伴う需要予測の必要性から逃れられると考えますが、部分的にはそうなりますが限界があります。Kanbanシステムで用いるビン、箱、バケット、またはスペースのサイズは、実は予測の産物です。それは、組織がバッファや安全在庫として採用する数量に直接関係しています。これはリスク軽減策であり、リスク評価に基づいています。多くの場合、この評価はデータに基づくのではなく、経験的であり、何ヶ月にもわたる微調整や再評価を経た結果であるため、それが予測であることに変わりはありません。適切に行われなかった場合、もしくはビンサイズがカバーする現実の複雑さについて正確な評価が行われなかった場合、Kanbanシステムの微調整は長期化する可能性があります。
特に、サプライヤーや第三者から補充を得る能力に重点を置く必要があります。ビンのサイズは安全在庫とみなすことができ、これはサプライヤーのリードタイムに直接関連します。基本的に、問題は次の通りです:サプライヤーが新たなアイテムを届けるのにかかる時間をカバーするため、ビンはどの程度持続すべきか?サプライヤーが信頼でき、リードタイムが一定であれば答えは簡単ですが、経験上必ずしもそうではありません。したがって、サプライヤーが信頼できず、リードタイムが変動する、または生産工程で使用される資材の品質自体が変動する場合、Kanbanの導入は難しくなります。リードタイムの変動を考慮できないと、結果的に常に不必要に大きなバッファを抱えることになりかねません。
年間を通して需要が変動する、例えば強い季節性がある場合も同様です。プルシステムであっても、ストックアウトを避けるため、需要に何らかの形で対応する必要があります。生産または供給チェーン管理において、ビンのサイズは状況に応じて変化すべきであり、一定であってはなりません。同時に、ビンが絶えず再評価されると、システム自体の意味が失われてしまいます。したがって、Kanbanシステムに対する主要な批判の一つは、積極性と適応性の欠如です。
Kanban は、バッチ生産と規模の経済という特性上、「必要最小限」という考え方に反する場合、効率が悪化したり、実装がはるかに困難になったりする。逆に、一度に大量生産する(または、仕入先に大口注文を出してより安価に仕入れる)ことでコストを削減するという考え方が存在する。これは、需要が必ずしも発生しない可能性を前提に、過剰生産や在庫過多のリスクを取ることを意味する。そのようなリスクには大きなリターンが伴うこともあるが、Kanban はより安定した運用を実現する一方で、大きな成果が得られない可能性もある。
最後に、Kanban は極めて局所的な視点に依存しており、一段階ごとに最適化を行い、特定の事象に対して局所的かつ単純な対応をするという議論がある。この局所的な視点こそが Kanban の強みであるが、同時に Kanban は ネットワーク効果 や、システム全体におけるフローや資源の不適切な分配などに対しては無知である。また、システム全体のリスク にも弱い。例えば、ある B2B ビジネスでは、特定の顧客が存在する場合にのみあるカテゴリーの製品が存在することがある。その顧客が消滅すると、製品に対する需要も完全に消滅してしまう。Kanban はそのようなリスクを考慮するようには設計されていない。陳腐化の問題 に関しても同様である。これらの欠点は、Kanban を効率的なシステムとして無効にするものではなく、むしろその本質的な限界を理解した上で利用すべきであることを示している。
Kanban の SCM(サプライチェーン管理)と在庫管理への応用
もともとは製造業に純粋に関連していた Kanban は、姉妹手法である Lean とともにサプライチェーン管理(SCM)の分野に進出した。基本原理は変わらず、在庫が枯渇した際に、事前に定められた数量の発注をシンプルかつ視覚的に行うことで、在庫およびそれに伴うリスクを最小限に抑えるというものである。これは、Kanban がスーパーマーケットでの消費者の行動観察から生まれた事実と矛盾しない。消費者は、自宅に商品をため込むためではなく、必要なものを購入し、消費が終われば再び来店する。そして、必要な時には常に商品が補充されるという認識を持っている。スーパーマーケットでは、棚は一定量の商品しか保持しないように配置され、内容が消費され棚が空になると適宜補充される。製品の回転率を考慮して、いくつかの標準的な棚の奥行きが設定されており、棚を見回す担当者は、一目で補充の必要性を判断できる。
スーパーマーケットや一般の販売現場で成立していることは、さらに広い範囲に適用できる。SCM では、3ビン方式は次のように解釈できる。まず、初期需要を満たすための「ビン」が店舗や販売現場に配置され、次に倉庫(またはそれに相当する在庫拠点)に第二のビン、そして仕入先側に第三のビンが設置される。店舗が在庫を消費すると、倉庫への補充を要求し、倉庫は仕入先に発注する。前述のビンのサイズに関する考えはここでも有効であり、「ビン」の大きさは、組織が保持する安全在庫の量と、仕入先のリードタイムおよび信頼性ある補充能力に直接関連する。さらに、仕入先側では MOQ(最小発注量)などの追加考慮事項が存在する場合があり、仕入先は一定の数量に達しなければ補充に応じないことがある。これは複数の品目に共通する場合があり、SKU ごとに SKU として管理されないこともある。場合によっては、単位あたりの価格の問題に帰着する。少量の補充は可能な場合もあるが、コストが高くつく。
SCM における Kanban の長所と短所は、先に述べた製造業でのそれと変わらない。Kanban を適用することで、在庫(およびそれに伴うリスクやコスト)は通常削減されるが、その代償として柔軟性が損なわれ、仕入先やそのリードタイムへの依存度が増す。さらに、ネットワーク効果を享受したり、仕入先の MOQ(最小発注量)、MOV(最小発注額)、または価格割引の恩恵を十分に活かすことが難しくなる。
さらに、在庫に対して非常に単純な見方を採用しているため、Kanban は変動性がプラスに働く状況に対して鈍感である。Kanban は、生産が途切れることなく進行し、在庫が使い果たされた際には常に補充が行われるという前提に基づいている。しかし、ライフサイクルの末期にある商品や季節商品においては、あえて在庫切れにすることが望ましい場合もある。また、信頼性の低い、もしくはリードタイムが長期あるいは不規則な仕入先の場合、単位あたりの価格が低く抑えられることもある。在庫切れが時折発生するが高い利益率を持つ商品の販売は好ましい場合もあり、決して在庫切れとならないよう十分な安全在庫(または満杯のビン)を維持することは実際的ではない。特定の商品において、断続的に生産される(例:地元のイチゴ)または市場の変動(例:世界市場価格に連動する生産)の特性を活用することは、組織にとって大きな利点となり得る。しかし、Kanban はそのような利点を十分に活かすことができない。
しかし、需要が非常に安定している、または極端に低い場合、予測が非常に不正確になるほどであっても、Kanban は有力な選択肢の一つとなりうる。例えば、ファッション業界では、一部の小規模な販売拠点で非常に不規則な低い販売量が見られる。ある SKU では、シーズン中にわずか数件の販売に留まることもある。このような販売拠点や品目において、Kanban は信頼できる解決策となる。なぜなら、それ以外の方法では対応が困難だからである。
前述の通り、Kanban は予測の必要性を軽減するものの、それを完全に排除するものではない(ビンのサイズ設定自体が一種の予測である)。したがって、混合アプローチも可能だと言える。予測が Kanban に組み込まれることもあれば、逆に必要な場面において、いくつかのヒューリスティックを通じて予測プロセス内に Kanban の要素を統合することも可能である。
Lokad の見解
Kanban の力は、適切に選ばれた ヒューリスティックと強制された不変条件 にある。これらはあくまで近似値であるものの、堅牢で揺るがない。設計段階から正確性とリスク制限を念頭に置いて実装されているため、その上回るのは難しい。Kanban と他の手法の間には「不気味の谷」が存在するとも言える。確かに Kanban を凌駕することは可能だが、そのためには多大な労力が必要である。単純な予測ツール(従来の数学モデルなど)や中途半端な AI ソリューションの使用—特に特定の種類のデータに対して—では通常、効果を発揮しない。多くの場合、予測-方法と-excel-での-数式は、Kanban のシンプルなビン、安全在庫、カードの利点を克服するための、実際の優位性を備えている必要がある。
しかし、この単純な方法は静的なものであり、局所的な視点にとどまり、洗練されず、特定のリスク(およびリワード)に対して盲目的である。そのため、ネットワークの問題や不規則性の利点を評価する際には役に立たない。Lokad では、状況に応じてビジネスの現実に根ざしたスマートなヒューリスティックを活用することで、両者の長所を取り入れ、Kanban を超えることが可能だと考えている。これは、決定-駆動-最適化および 量的-供給-チェーン-マニフェストを実装する際の基本コンセプトの一つであり、ユーザーにはシンプルで視覚的な操作性を提供しつつ、常にデータに基づいた進化的で計測され、熟慮され、改訂されるソリューションを提供することを目指している。