リーン・サプライチェーンマネジメント (Lean SCM)
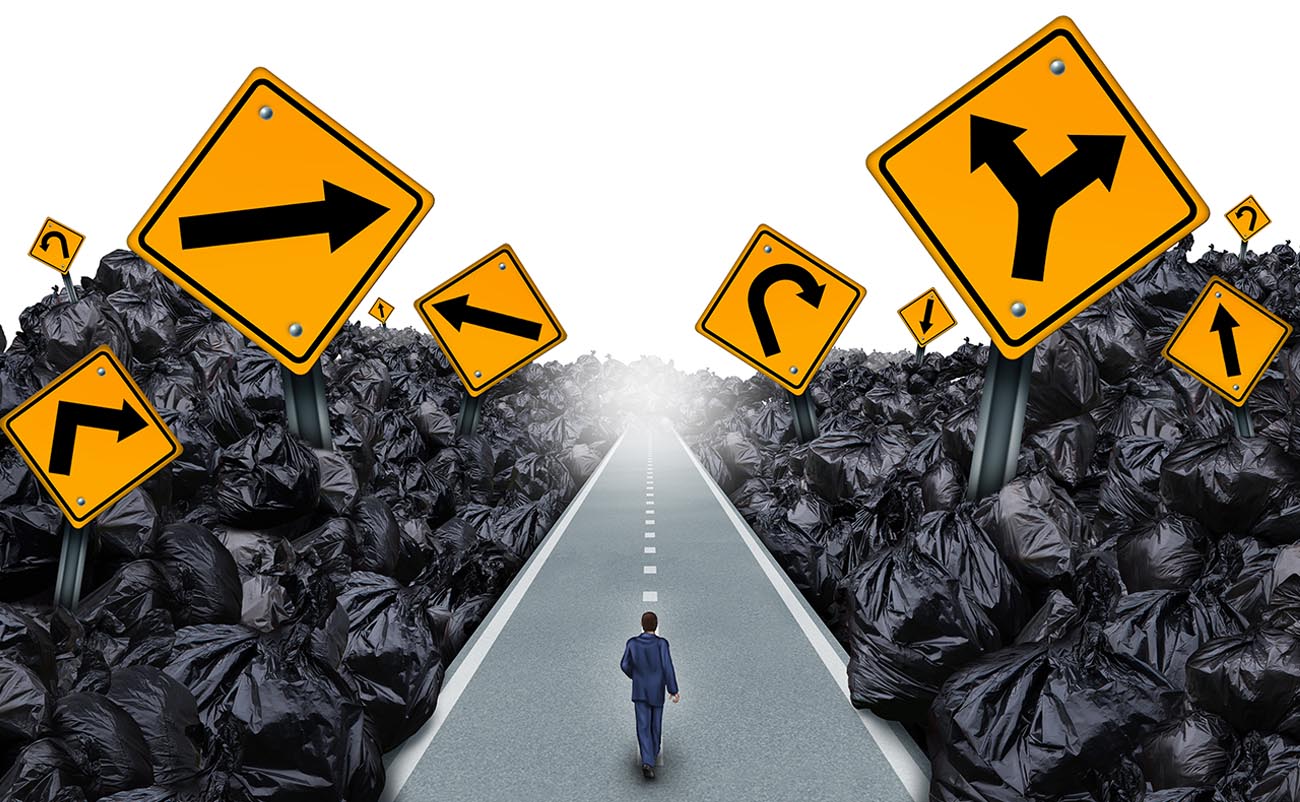
90年代から、「リーン」は最初に製造業界で重要な概念として登場し、そこからサプライチェーンマネジメント(SCM)など他の分野にも広がりました。サプライチェーンがリーンであるとはどういう意味でしょうか?無駄を継続的に削減する努力はどのような結果をもたらすのでしょうか?SCMの複雑で多面的な性質、サプライチェーンネットワークにおける多数の選択肢への妥協、さらには需要やリードタイムの変動を考慮すると、リーンSCMは実現不可能なユートピアのように思われるかもしれません。しかし、この視点は、元のリーン製造のビジョンといくつか顕著な違いはあるものの、より効率的で競争力のあるサプライチェーン再構築の鍵となり得ます。
リーン製造からリーン・サプライチェーンマネジメントへ
リーン製造を詳細に解説することは避けますが、その基本的な要点を簡単におさらいしましょう。リーン製造とは、無駄を最小限にし、コストと生産時間を削減するための手法であり、日本の自動車メーカーであるトヨタに触発され、90年代に「リーン」という言葉で広く知られるようになりました。特に、これは日本語で muda、mura、muri と呼ばれる、1) 価値を生まないプロセス(例: 過剰生産や不必要な移動)、2) 不均一(例: 不規則なスケジュール、アイドル時間と急な作業の繰り返し)、3) 過負荷(例: 重すぎる荷物や不適切な道具を使わせられる労働者、または限度を超えた要求をされるチームや機械)の3種類の無駄の削減を意味します。また、リーン製造のアプローチは、生産のスムーズな流れの構築やボトルネックの削減も含意します。
ツール以上に、リーン製造は文化的かつマネジメント的なアプローチに基づいており、戦略、手順、標準化、簡素化を、常に改善を追求しながら人々への敬意を忘れないリーダーシップによって設計・実施します。したがって、従業員との長期的な関係構築、労働者へのリーン哲学の伝達、そしてベテランと新人(日本語では 先輩 と 後輩)との本質的な連携に大きな重点が置かれます。従業員が無駄削減と継続的改善に賛同し、実際に信じることがリーン製造の成功の鍵であり、それが西洋文化での実施が難しかった理由の一つとも言えます。これが、リーン製造が時に科学ではなく宗教と評される理由でもあります。
初期の概念はサプライチェーンやサプライチェーンマネジメントへと転用されました。『リーン』なSCMは、製造だけでなく、倉庫管理、輸送、返品などサプライチェーンのすべての段階において、無駄を排除し、より良い在庫管理と流れの合理化を目指して継続的な努力を行います。ここに問題があります。SCMは本質的に非常に複雑であり、さまざまな活動、チーム、フロー、あらゆる局面での終わりなき選択肢が存在し、非常に変動し予測が困難な需要に適応する必要があります(詳細はSupply Chain Management (SCM)を参照)。それにもかかわらず、無駄削減のための継続的な改善目標は有効ですが、その複雑性に合わせた対策が求められ、単に文化的・マネジメント的な手法に依存することはできません。
リーン・サプライチェーンマネジメントにおける無駄の排除:全体的視点対局所的アプローチ
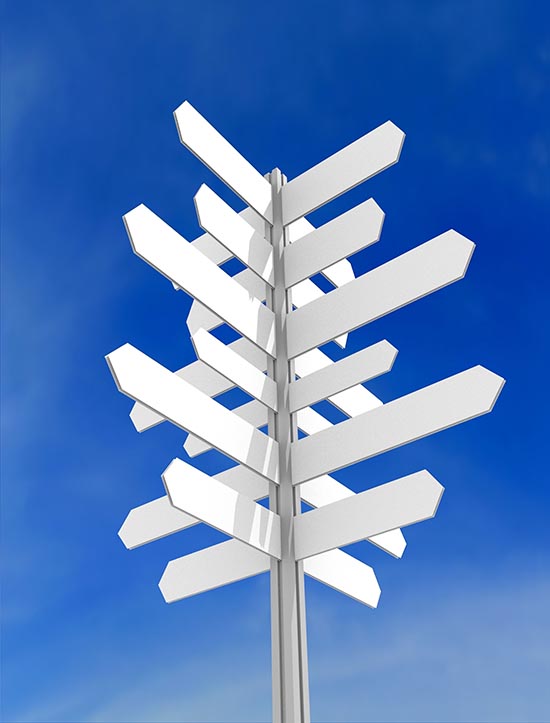
サプライチェーンマネジメントの複雑性は、その包括性に由来します。さらに、サプライチェーンは対立する見解、プロセス、インセンティブ、そして矛盾する電子記録に溢れているため、包括的な視点があらゆる改善の取り組みにおいて不可欠です。
例えば、小売ネットワークを持つ企業を考えてみましょう。中央の倉庫を担当する調達チームの目標―おそらく金銭的なインセンティブも―は、必ずしも店舗マネージャーやオーナーの目標と一致していません。中央調達部門は在庫を削減しようとする一方で、各店舗のマネージャーは在庫切れがなく、店舗が製品で満たされていることを望みます。特に、未販売の商品が中央倉庫に返品可能であり、店舗自体が過剰在庫にかかる費用を負担しない場合はなおさらです。店舗マネージャーは、もしある製品の売れ行きが良くなれば、倉庫レベルで在庫切れになると見込み、大量発注に踏み切る傾向があります。こうすることで、過剰在庫のリスクを冒すだけでなく、他店舗でより早く売れる製品の独占や、他の場所での在庫切れを引き起こす可能性もあります。さらに、ネットワーク内で電子記録のズレが生じると、在庫切れの誤った印象を与え、状況は悪化します。これにどう対処すべきか?このような状況での「リーン」とは何を意味するのでしょうか?店舗マネージャーにとっては、在庫切れがなく、製品を簡単に返品できることがスムーズさを意味しますが、倉庫レベルでのスムーズさは、むしろ回転の速い店舗のために他の店舗のパフォーマンスを犠牲にすることを意味する場合もあります。同時に、回転の速い店舗だけを推進することは、長期的には小売ネットワーク全体にとって有害となり、一部の店舗の業績が急落する可能性があります。
リーン製造では、課題はより二元的な性質を持つ傾向があります。製造は物理法則に従うため、非常に困難ですが、少なくとも「機能するか否か」という二極性があります。もちろんバランスや微調整も必要ですが、一般的に製造プロセスのステップA、その後のB、Cをそれぞれリーン化することで、生産全体がリーンになる傾向があります。しかしサプライチェーンではそう単純ではありません。ステップBをリーン化すると、実際にはステップCに問題が生じる可能性があります。リーンSCMは局所的な改善の積み重ねではなく、常に包括的な視点を採用すべきです。 一つの側面として、可能な限りインセンティブの整合を図る必要があります―しかしこれは必ずしも容易ではありません。もう一つはITシステムの整合(後述)が挙げられますが、何よりも重要で(かつ厄介な)KPIsの問題が存在します。もしリーンSCMが無駄削減を目的とするならば、どのように測定すべきでしょうか?さらに包括的な視点で測定するためには、各タスクのあらゆる側面に特化したKPIで溢れるダッシュボードを作成することが可能ですが、いかにしてあらゆるレベルで意味を持つKPIや指標を選定できるのでしょうか?
実は答えは非常にシンプルで、実務ではほとんど適用されていません。企業にとって意味のある通貨(ドル、ユーロなど)は、無駄削減の最も良い指標となります。つまり、リーン・サプライチェーンの取り組みにおけるすべての行動は、その財務的影響と投資回収率の観点から評価されるべきであり、行動は比較・検討・優先順位付けされる必要があります。もし、中央倉庫で製品Aを保持することが100€の在庫コストと、店舗A・Bでの潜在的な1000€の売上損失を生み出し、しかし店舗Cでの潜在的な利益が2000€あるとするなら、答えは明白です。すなわち、製品を店舗AとBに移動させるのは無駄であるということです。もちろん、これは非常に単純化した説明です。一方では、連鎖販売による売上損失や、製品Aによって他の製品の売上が減少すること、さらには時間の経過によるロイヤルティの損失も考慮すべきです。また、店舗AとB向けにトラックが満杯にならない場合、製品BとCの配送コストが増加することや、店舗Cで在庫切れとならずに製品Aが他製品を食い合う可能性など、あらゆる要因を勘案する必要があります。最後に、これらはすべて本質的に不確実な潜在的売上に基づいている点も考慮しなければなりません…
その複雑性は急速に途方もなくなる可能性がありますが、SCMの性質上、避けられないものです。これが、リーンSCMがリーン製造と異なる点でもあります。サプライチェーン内の無駄削減の問題は、単に労働力との関係に着目したマネジメント的アプローチだけでは解決し得ません。なぜなら、その問題は人間の頭脳だけでは到底処理しきれないほど大規模だからです。SCMは多次元的であり、リーンSCMへの道も、IT、ツール、チームのチェンジマネジメント、そして必ずしも単純さが望ましいとは限らない現実の受容を伴います。
リーン・サプライチェーンマネジメントがもたらす変化とは?
シンプル vs. 単純過ぎる
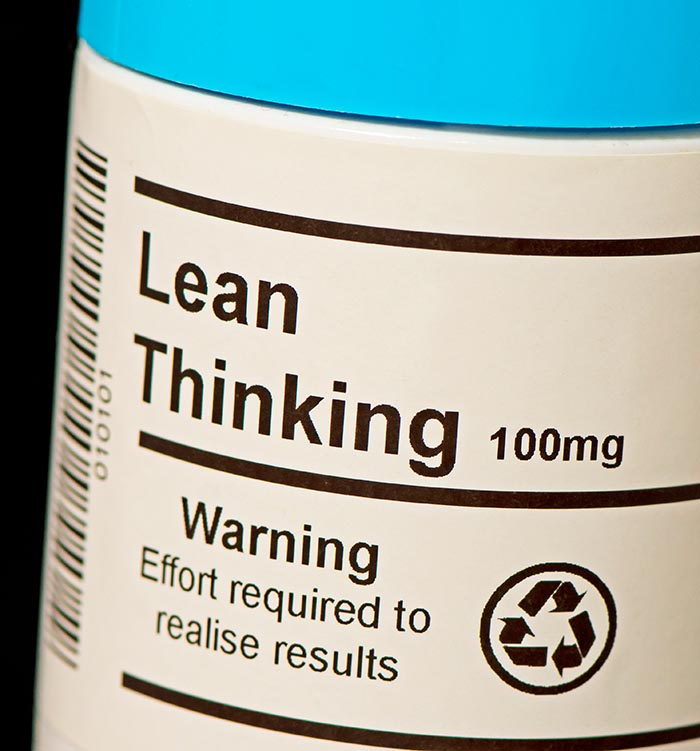
リーン・サプライチェーンマネジメントの取り組みは、多層的な変化をもたらすことが期待され、決して容易なものではありません。そのような取り組みには、強力なリーダーシップと最高レベルでの戦略的思考が求められます―これはリーン製造の場合も同様です。しかし、リーン製造との明確な違いは、こうした取り組みのリーダーが、単純化されたモデルがリーンSCMにおいてしばしば逆効果であることを受け入れ、常に念頭に置かなければならない点にあります。単純さの追求―それ自体は常に良いことですが―現実世界に存在する解消不可能な複雑性を無視してはならないのです。
例えば、顧客に供給される製品の調達方法は多岐にわたり、同じ製品でも、ある者は定期的に小~中ロットで発注し、別の者は非常に低コストの大口注文の機会を稀に得るため、結果として在庫バランスが崩れ、他の製品を食い合ってしまう可能性すらあります。均一性を高める簡単な解決策は、サプライヤーの数、契約形態、価格条件などを削減することですが、その結果、柔軟性が失われ、海外と国内のサプライヤーのバランス調整や、サプライヤーのリードタイムと価格条件の相互活用、さらには全体としてのコストや顧客満足度に寄与する「バックアップ」サプライヤーの維持が困難になる可能性もあります。
改めて、SCMはトレードオフのゲームであり、各選択肢を互いに天秤にかけ、理想的には最後の瞬間に不確実性を軽減するための最適な選択を行うことを意味します。これは、予想以上に売れている製品に対して迅速な在庫補充が可能となることを意味する場合もあります。
孤立を減らし、連携を強化する
サプライチェーンの複雑性は避けがたい側面であり、よりリーンなサプライチェーンを実現するためには、強固な連携が必要です。サプライチェーン各段階―さらには各チーム間―で長年にわたり形成された障壁は、全体像の理解を深めるために、少なくとも部分的には取り除かれるべきです。ここで重要なのはチームの関与です。適切なリーンSCMの取り組みを実施するためには、業務プロセス、使用されるツールやITシステムが理解され、議論され、文書化される必要があります。組織全体の全メンバーに対して最高レベルの詳細まで透明化することは不可能ですが、プロジェクトを担当し各部門を代表する少なくとも数名の主要なコーディネーターには、できる限りの理解と透明性が確保されるべきです。これらの人物は、自らのチームにこの取り組みを伝える責任を担います。文書化こそが成功の鍵です。一般に、チェンジマネジメントは、労働力の再編成を伴うことが多いため、リーンの取り組みを成功させる上で重要なステップとなります。
孤立の解消はITにも影響を与える可能性があります―すべてを一つの汎用プログラムに統合すべきという意味ではなく、単にシステム同士がより効率的に連携すべきということです。また、これは組織の財務運営にも影響を及ぼします。局所的な改善はリーンSCMの落とし穴であり、その典型例が局所的な予算の最適化です。予算が完全になくなるべきではなく、より柔軟性が認められ、不必要な障壁が取り除かれるべきです。特に調達部門においては、分割された予算は管理しやすいものの、使用される資金は常に会社のものであるため、全体最適のために支出すべきであり、一部の製品カテゴリに過剰支出して他でのROIが低下するリスクを冒すべきではありません。無駄削減は、組織全体のカタログレベルで実施されるべきであり、カテゴリごとやチーム間だけの問題ではありません。
ホワイトカラーの生産性向上
特に、リーンSCMイニシアチブの目標は、ブルーカラー労働者向けのリーン製造で得られたのと同様の効率性と生産性向上を実現することであるべきです。これらの成果は、ホワイトカラー向けサプライチェーンの大部分でまだ達成されていません。ますます多くの人々がExcelのスプレッドシートなどを用い、時間のかかる反復的な作業を非常に非構造的な方法で行っており、これに伴うシャドウITは言うまでもありません。これは、より複雑なプロセスを伴う内部官僚制の発展、複数段階の検証(通常はウォーターフォール型プラン構造に関連)やレガシーITシステムから生じる可能性があります。その結果、通常、過度に業務負担がかかる労働力、透明性の欠如(シャドウITや文書化されていないルールを持つ個別にカスタマイズされたExcelスプレッドシートが典型例)、構造と標準化の欠如、さらには全体を見渡す視点や適切なKPIがないために短期的な視野に陥る状況が生まれます。常にサプライチェーンにおいて、市場がより多くのオプション(製品のカスタマイズ、直前の配送など)を求めるほど、これらのホワイトカラーにとっての負担は増大し、すべてが柔軟性や最適なトレードオフを容易に選択する能力の妨げとなります。
生産は高い生産性と低コストを追求するために多大な注目と改良の対象となってきましたが、計画、価格設定、スケジューリングの改善余地は非常に大きいです。リーンSCMの効果の一つは、これらの業務を担う人員の効率性を高め、組織全体のためにより迅速かつ適切な意思決定を行えるよう必要な構造を提供し、場合によっては付加価値のない日常業務の一部を自動化することにあります。しばしば、これはチームの縮小や、より高い価値を生む自動化不可能な作業への業務再配置を意味します。
また、古い習慣やレガシープロセスを排除することも意味します。たとえば、安全在庫のような典型的なバッファや、最小/最大発注のような過度に単純化された思考方法は、まず取り除くべき無駄の一つです。これらはすべて、自然と変革マネジメントを伴い、再び上層部で主導されエンドユーザーに浸透される必要があります。なぜなら、新しいプロセスに対する彼らの順応が、この種のイニシアチブの成功の鍵となるからです。
専用投資
先に述べたように、SCMは非常に複雑であり、あらゆる無駄を削減する努力は、あらゆる選択肢の対策や財務評価を必要とします。業務プロセスの理解は、需要、トレンド、および戦略の影響を測定・定量化するために、適切なデータ分析に裏打ちされるべきです。したがって、ツールは必要不可欠であり、回避できないものです。ここにLean Manufacturingとの違いが存在します。もしSCMがトレードオフの科学であるなら、Lean SCMは主に信念に頼るのではなく、事実に強く根ざしているべきです。
しかしながら、各サプライチェーンは固有の制約、プロセス、特性―そしてレガシー―を持つため、Lean SCMを目指すことは通常、市場に既製のツールが存在しないという理由から専用投資を伴います。そのようなツールは、特定のサプライチェーン固有の制約に適応し、できるだけ広い視野でパフォーマンスを評価できるものでなければならず、必要に応じて異なるITシステムからの入力を取り込むことができる必要があります。理想的には、Leanイニシアチブはすべてのデータを集約するシステム、すなわちデータレイクの構築をも伴い、これがサプライチェーン最適化のさらなるイニシアチブの基盤となります。あるいは、IT自体をよりリーンな形に再構築することも可能です。
この点において、シンプルとイージーは全く異なるものであることを強調しておく必要があります。レガシーは、チーム内の古い習慣やプロセスと同様に、ITにも存在します。サプライチェーンのITシステムには、多くの偶発的な複雑性が伴います。多くの場合、サプライチェーンの一端と他端で計測単位に一貫性がなかったり、システム間で命名規則が異なり意味が異なることがあります。例として、日付を含むフィールドは通常悪夢のようなものです。同じテーブル、さらには同じ列内でも、行によって日付が注文日であったり返却日であったりする場合があります。企業で一般的に採用される簡単な方法は、システムに漸進的な修正を加え、ここそこに新たな列を追加したり、既存の列を別の用途で再利用したりすることですが(これがおそらく、返却が注文と同じ列に混在する理由です)、システムをリーンに保つためには、構造上シンプルである必要があります。すなわち、一種類のイベントは一つのテーブルに対応し、適切かつ明示的な名称が付けられ、理想的にはそのテーブルの内容がどこかに適切に文書化されているべきです。これは、サプライチェーンが進化する際にITの徹底的な見直しが求められ、レガシーを回避するために必要な措置です。改めて三種類の無駄に戻ると、ITの構造上の問題は、不均一性(例:テーブル間またはシステム内での一貫性の欠如)、付加価値のない作業(例:問題を補うためにスタッフが行う回避策)、そして最終的には過負荷(例:これら意味のない作業によって過剰に業務が詰まり、生産性が著しく低下する)を引き起こす可能性があります。 現代のサプライチェーンに関しては、ITは―あるいはあるべき―あらゆるリーンの取り組みの中心に位置しています。
Lokadのリーン・サプライチェーン・マネジメントに対する見解
Lokadの量的供給チェーンマニフェストは、リーンの哲学と多くの共通点を持っています。確かに、無駄の削減―特により良い在庫管理を通じた削減―は、我々が共有する目標です。我々はまた、適切なKPIに基づいた全体的なビジョンを常に念頭に置くよう努めています。Lokadにとって、量的供給チェーンのイニシアチブは、業務プロセスの深い理解を得るためにプロジェクトコーディネーターの支援を受けつつ、先進的なデータ分析による定量的評価を通して横断的にリードされるべきです。
Muda(付加価値のない行動)は自動化につながるべきであり、調達、計画、または価格設定チームを支援するシステムの提供により、より効率的かつ迅速な意思決定を可能にします。予測においては、従来の集約や不要な高精度(例:月に一度の注文なのに日ごとの予測を行うなど)に頼るのではなく、ビジネス上意味のあるレベルで直接予測を行うこと、または主にレガシーな慣習であるバッファ(例えば安全在庫)の充足を目的とした予測を意味します。Mura(不均一)は、実装の初期段階で詳細なマッピングを伴うデータ分析を通じて取り組むべきであり、これにより今後のさらなる分析のための強固な基盤が提供されます。最後に、Muri(過負荷)は、自動化および専門のサプライチェーン・サイエンティストによるチーム支援と密接に関連しており、その結果、数千もしくは数十万にも及ぶカタログを手作業で処理する負担をチームに強いることがなくなります。また、在庫が適切に管理され、倉庫や店舗が過剰在庫であふれ出すことがないようにすることも意味します。
Envisionを通じて、我々は利用可能なすべてのオプションに対して確率的分析を柔軟に実施し、その財務的影響を評価します。そして、ダッシュボード、優先順位リスト(発注リスト、配送リスト、割引、…)およびKPIを通じて、エンドユーザーに一部の作業の自動化、シミュレーションの実施、市場への迅速な対応の可能性を提供します。