需要駆動型資材所要計画(DDMRP)
需要駆動型資材所要計画(DDMRP)は、多階層製造業のsupply chain performanceを最適化するための定量的手法です。この手法は、『デカップリングポイント』と『在庫バッファー』の概念を中心に据え、ほとんどのMRP(資材所要計画)システムで実施されている旧来の手法の欠点を緩和することを目的としています。この手法は、多階層のSKU(ストックキーピングユニット)の任意のBOM(部品表)に対して、購入または製造すべき数量を提供します.
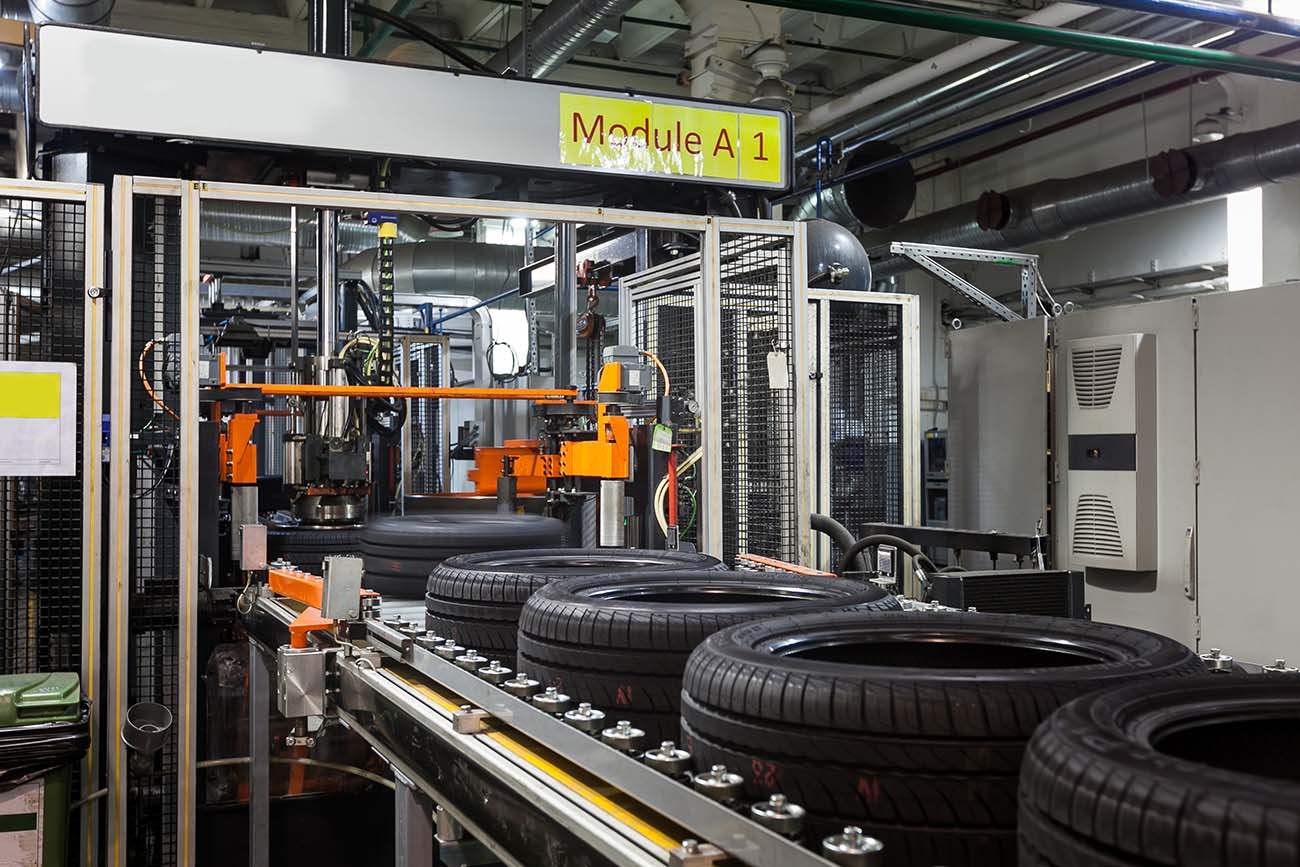
2024年11月更新: Joannes Vermorel氏とCarol Ptak氏は、最近のsupply chain debateでDDMRPについて議論しました.
多階層BOMフロー最適化の問題
BOM(部品表)は、最終製品の製造に必要な組立、コンポーネントおよび部品、ならびに各々の数量を表します。多階層BOMは、元のBOMを再帰的かつ階層的に捉えたもので、特定の部品がさらに独自のBOMによって分解されます。形式的には、多階層BOMは頂点がSKU、辺が包含(すなわち一部であること)を示し、重みが組立に必要な数量(最終製品または中間製品)を表す重み付き有向非巡回グラフ1です.
DDMRPが対処する問題は、多階層BOM内でのフロー最適化であり、任意の時点において、(a)追加の原材料を調達すべきかその量はどれほどか、(b)任意のSKUの生産ユニット数を増やすべきかその数はどれほどかを決定することにあります.
直感的には、この問題は、通常service levelsで測定される中間SKUのサービス品質と最終製品のサービス品質との間に直接的な相関関係が存在しないため、困難です。あるSKUに在庫を追加しても、そのSKUが製造フローにおいてボトルネックであった場合にのみ、最終製品のサービス品質が向上します.
実際には、このフロー最適化問題を解決するために、通常以下のような追加情報が必要となります:
- クライアントからの注文履歴
- 供給業者のリードタイム
- 手元在庫、水中在庫、または発注中の在庫レベル
- 製造リード-タイムおよび/または生産スループット
- その他
さらに、実世界のサプライチェーンでは、バッチサイズ(供給業者や製造プロセス自体によって課される望ましい乗数)、賞味期限(perishableな製品に限らず、化学物質や精密機器にも適用される)、不完全な代替品(例:安価な部品が入手できない場合に、より高価な部品が代替として使用される場合)などの複雑な要素が存在します。これらの複雑さは、モデルにさらなるデータを反映させる必要があります.
クラシックMRPの限界
DDMRPの誕生は、主に1980年代に開発されたクラシックMRPの視点(以下、単にMRPの視点と呼ぶ)に関連する限界に起因しています。MRPの視点はリードタイムの分析に重きを置き、BOMグラフ上で最も長いパス(時間的)を最終製品の製造プロセスにおけるボトルネックとして特定します.
このボトルネックを特定するために、MRPはBOMグラフのすべての辺に静的なリードタイムを割り当てるための2つの異なる数値的方法を提供します:
- manufacturing lead times:最も楽観的な手法で、在庫が常に各SKUにおいて利用可能であると仮定し、リードタイムが製造プロセスのスループットのみに依存すると見なします.
- cumulative lead times:最も悲観的な手法で、在庫が常に利用できないと仮定し、リードタイムが在庫ゼロの状態から最初のユニットを生産するための時間のみに依存すると見なします.
これら二つの手法には共通の主要な利点があり、それは1980年代から2010年代にかけて設計されたほぼすべてのMRPの中心技術であるリレーショナルデータベース上で比較的容易に実装できるという点です.
しかし、これら二つの手法は過度に単純化されており、通常は意味をなさないリードタイムを算出してしまいます。DDMRPの著者らは、極端に誤ったリードタイム見積もりに基づき購買や製造注文を計算すると、リードタイムが大幅に過大評価または過小評価されるかに応じて、過剰在庫とstockoutsが混在する結果となると指摘しています.
DDMRPの数値レシピ
DDMRPのnumerical recipeは、数値的ヒューリスティックと人的判断(すなわちサプライチェーンの専門家)が組み合わさったものであり、このレシピは「高度な」数値アルゴリズムに頼ることなく、クラシックMRPに関連する欠陥を克服することを目的としています。このレシピは主に以下の4つの要素から構成されます:
- リードタイムの分離
- ネットフロー方程式
- 分離されたエクスプロージョン
- 相対的優先順位
これら4つの要素を組み合わせることで、サプライチェーン担当者は多階層BOMの状況において、購入および製造すべき数量を計算することができます。DDMRPの著者らは、この手法がMRPと比較して、inventory turnsやサービスレベルで測定される優れたサプライチェーンパフォーマンスを提供すると主張しています.
リードタイムの分離
MRPのリードタイムに対する極端な楽観主義/悲観主義を是正するために、DDMRPは、グラフ(すなわちBOM)の特定の頂点(すなわちSKU)をデカップリングポイントとして指定するバイナリのグラフ着色2方式を導入します。これらの頂点は常にサービス可能な在庫を保持していると仮定され、DDMRPの手法はそれが実際に実現されることを保証します.
デカップリングポイントの選定は基本的にサプライチェーン担当者に委ねられます。デカップリングポイントは在庫があるSKUであることが意図されているため、戦略的に意味のある、例えば複数の最終製品に消費され安定した消費パターンを持つSKUが好まれます.
一度デカップリングポイントが選ばれると、任意の頂点に関連するDDMRPリードタイムは、その頂点から開始して下方向に到達する最長パス(時間的)として計算され、デカップリングポイントに到達した時点でそのパスは切り捨てられます.
デカップリングポイントを慎重に選定することで、DDMRPの著者らは、DDMRP手法が短いリードタイムを実現すると主張しています。これはリードタイムそのものが短いからではなく、DDMRPがそもそもリードタイムと呼ばれる概念の新たな定義を提案しているためです.
ネットフロー方程式
購買注文または製造注文に関連する数量を計算するために、DDMRPの著者らは以下のように定義されるネットフローという概念を導入します:
手持在庫 + 発注中 - 適格な受注需要 = ネットフローポジション
この方程式はSKUレベルで定義され、ネットフロー数量は需要の不確実な部分に対応可能な在庫量として解釈されます.
その後、ネットフローポジションはバッファーサイズと比較され、目標バッファーより著しく低下した場合に注文が発行されます。この仕組みについては後述の注文優先順位付けのセクションで再度取り上げます.
DDMRP手法は、通常需要日数で表されるバッファーのサイズ設定に関する高レベルの指針を提供し、安全マージンを確保しながら先述のDDMRPリードタイムを尊重します。実際、バッファーのサイズ設定はサプライチェーン担当者の判断に依存します.
ネットフローを通じて、DDMRPの著者らは、実際に統計分析を必要とするのは需要の不確実な部分のみであると強調しています。既に分かっているfuture demandへの対応は、決定論的な実行計画に従うだけの問題です.
分離されたエクスプロージョン
DDMRPの手法は、在庫が常にいかなるデカップリングポイントからもサービス可能であるという仮定に依拠し、またそれを強制します。この仮定により、デカップリングポイント(すなわち頂点のサブセット)をパーティションの境界として利用して辺を分割する可能性が生まれ、この分割方式は分離されたエクスプロージョンと呼ばれます.
DDMRPの視点では、最終製品に対するクライアント注文が出されると、その需要は最も内側の構成要素まで再帰的に分解されるのではなく、最初に遭遇するデカップリングポイントまでのみ分解されます.
分離されたエクスプロージョンのグラフ分割方式は、DDMRP手法において分割統治3戦略として活用されます。特に、サブグラフのサイズを小さく保つことが可能なため、これらのシステムがグラフ解析に適していなくとも、MRPと同様にDDMRPはリレーショナルデータベースシステム上に実装できます.
注文優先順位付け
DDMRP数値レシピの最終的な数値的ステップは、購買注文または製造注文そのものを計算することにあります。DDMRP手法は、すべてのSKUをそれぞれのバッファー - ネットフローの差で優先順位付けし、最も大きな値を優先します。その後、リストを指定された順に処理し、正の値であり、かつ場合によってはMOQ以上のものを選定して注文を生成します.
DDMRPの優先順位付けは一元的(スコア的に)であり、すべてのデカップリングポイントにサービス可能な在庫を維持するという、独自の手法への内部的準拠によって推進されます。前述のセクションでは、このデカップリングポイントの重要な特性がいかに活用されたかが示されており、注文優先順位付けはその特性の強制方法を明確にします.
DDMRPの著者らが提案する注文優先順位付けは、ABC analysisなどのMRPで一般的に見られるレシピよりも細分化されており、少なくともDDMRPの緊急性基準に基づけば、サプライチェーン担当者が最も注視すべきSKUに注意を向ける仕組みを提供します.
DDMRPへの批判
DDMRPの著者らは4、この手法の利点5を最先端のサプライチェーンパフォーマンス最大化の実践として推進しています。一方で、以下に詳細に述べるいくつかの「隠れた」利点はあるものの、この手法には、新規性とパフォーマンスの両面を評価するための誤った基準および実世界の複雑さを捉えきれていないという、複数の批判が存在します.
隠れた利点
一見すると逆説的に思えるかもしれませんが、DDMRPに賛成する最も強力な議論は、少なくとも2019年の出版物においては著者自身によって適切に特定されなかった可能性があります。この一見明白な逆説は、おそらく以下で詳述するDDMRPの限定的な形式主義の意図しない結果です.
製造サプライチェーンに関しては、frequential moving averagesは通常temporal moving averagesよりも優れていることが多いです。実際、DDMRPが需要予測なしで機能すると述べるのは誤りです。バッファーは予測であり、日別の需要ではなく、需要日数として表される頻度ベースの予測です。一般に、需要が不規則または断続的である場合、頻度ベースの予測はより堅牢です。この発見は、1972年に「Forecasting and Stock Control for Intermittent Demands」を発表したJ.D. Crostonにまで遡ることができます。しかし、Crostonの手法がやや不透明である一方、DDMRPはこの視点をサプライチェーンの世界全体に普及させました.
Approximate prioritizationは、サプライチェーンにおける堅牢な意思決定メカニズムであり、特に体系的なバイアスなどの一連の問題を防ぐ役割を果たします。実際、局所的なサプライチェーンの要因(例:ストックアウト)により数値が歪められやすい安全在庫のようなSKUごとのアプローチとは異なり、緩やかなサプライチェーン全体の優先順位付けであっても、資源がまず明白なボトルネックに向けられることを保証します。DDMRPの著者らは、優先順位付けが注意喚起の手段として有益であることを十分に理解しているものの、その洞察は論理的結論に至っておらず、優先順位付けは経済的、すなわちパーセンテージではなくドルで測定されるべきだと考えています.
誤ったベースライン
DDMRPに対する最も大きな批判は、その誤ったベースラインにあります。1980年代初頭から2010年代後半にかけて実装・販売されたMRPは、実際には何かを計画、予測、または最適化するようには6設計されていませんでした。MRP(資材所要計画)という名称自体が誤称であり、MRM(資材要求管理)とすべきでした。これらのソフトウェア製品はリレーショナルデータベース(すなわちSQLデータベース)を中核に構築され、主に企業の資産管理や、ユニットピッキング時の在庫レベルの減少など、最も日常的な業務に伴う事務作業を行うことを目的としています.
リレーショナルコアは、ほとんどの種類のグラフアルゴリズムのような数値集約的な処理と本質的に相容れないため、上記で示した2種類のリードタイム推定に見られるように、そのような製品が提供する数値レシピが単純で機能不全に陥るのは驚くべきことではありません。にもかかわらず、サプライチェーンの予測的数値最適化に関するコンピューターサイエンスの文献は膨大なカタログとして存在します。この文献は1950年代に「オペレーションズリサーチ」として先駆けられ、その後、供給チェーン-管理-定義における定量的な手法や単なるサプライチェーン最適化など、さまざまな名称で追求されてきました。
DDMRPに対する新規性および優位性の主張は、MRPがサプライチェーン最適化のための適切なベースラインであるという誤った前提に基づいているため、誤っています。すなわち、MRPの改善がサプライチェーン最適化の向上を意味するという主張ですが、リレーショナルデータベースを中心に設計されたすべてのソフトウェアシステムと同様に、MRPは数値最適化の課題に対して単に不向きなのです。
MRPの制約に縛られた製造業者は、MRP自体の漸進的な改良を求めるべきではありません。なぜなら、数値最適化は根本的にMRPの設計と相容れないからです。むしろ、初めから数値性能向上のために設計されたすべてのソフトウェアツールや技術を活用すべきです。
限定的な形式性
DDMRPの視点は、単純な数式と判断による決定の奇妙な混合です。DDMRPは明らかに、加重有向非巡回グラフという特定の数学的枠組み内で動作しており、そのメカニズムにはグラフの彩色やグラフの分割といったよく知られた名称がありますが、これらの用語はDDMRPの資料には一切登場しません。グラフ理論が一般的なサプライチェーン担当者には複雑すぎるという主張もできるものの、形式性の欠如は著者らに、もっと正確かつ簡潔に記述できる数値挙動について冗長な説明を強いる結果となっています。
さらに懸念すべきは、形式性の欠如がDDMRPをコンピューターサイエンスの膨大な文献から孤立させてしまっている点です。その文献は、グラフ理論、確率的最適化、統計的学習といった、サプライチェーン管理の要件をはるかに超えて広範に研究された複数のコンピューターサイエンス分野の既知のアルゴリズムによって可能なことについて数多くの示唆を提供しています。その結果、DDMRPはしばしば単純化された視点を採用しており(この点については以下で再度触れますが)、既知のアルゴリズムや現在のコンピューターのハードウェア能力を考慮すれば正当化されないのです。
そして、DDMRPの限定的な形式性は、リードタイムが短縮されるといった誤った主張につながります。実際、数値的には、DDMRPによって計算されるリードタイムは、構造上、デカップリングポイントに遭遇するたびにリードタイムの経路が切り捨てられるため、ほとんどの代替手段よりも確かに短くなっています。しかし、DDMRPにおいてリードタイムが短くなると断定するのは方法論上の誤りです。正しい命題は、DDMRPではリードタイムが異なる方法で測定されるということです。DDMRPのリードタイム面での利点を定量的に適切に評価するには、市場環境の変化に直面した際、正式な方針によって管理されるサプライチェーンがいかに速やかに追いつくかを評価するための、全体システムの慣性という明確な概念が必要となります。
また、DDMRPでは判断に基づく決定が多用されており、つまり、デカップリングポイントの選択などの重要な数値判断を人間の専門家に委ねています。その結果、どの程度大規模なサプライチェーン(たとえば数千以上のSKUを持つような場合)であっても、DDMRPの実践を競合する適切に形式化された方法論とベンチマークするのは、実務上、もしくはほぼ不可能であるといえます。
最後に、現代のコンピューティングリソースの価格を考慮すれば、数値最適化プロセスの調整に人間の入力に依存するのは合理的な命題ではありません。メタパラメータの調整は許容されるかもしれませんが、グラフの各頂点での細かな介入は認められません。特に、現在のサプライチェーンをざっと観察すると、人間の入力の必要性がシステム全体の慣性を引き起こす最大の要因の一つであることが分かります。さらに、手動の調整層、すなわちデカップリングポイントの選択を追加することは、この点で改善とはならないでしょう。
現実世界の複雑性を軽視する
サプライチェーンのモデリングは本質的に現実世界の近似であるため、すべてのモデルは精度、関連性、計算可能性との間でトレードオフを強いられます。それにもかかわらず、DDMRPは、今日のテクノロジーを考慮した場合、もはや合理的に無視できない多くの要因に関して、過度に単純化されています。
サプライチェーンは企業の経済的利益に奉仕するために存在します。率直に言えば、企業は経済全体との相互作用を通じて生み出される収益を最大化するのです。しかし、DDMRPは、いわば恣意的とも言える目標―つまりそのバッファー―に対してエラーの割合を最適化します。DDMRPによって定義された優先順位付けは内向きであり、サプライチェーンシステムを、すなわちデカップリングポイントでの在庫利用可能性というDDMRPモデル自体の前提に一致する状態へと誘導します。しかし、この状態が企業の財務的利益と一致している保証はなく、場合によっては企業の財務利益に反する可能性さえあります。たとえば、互いに近い代替品となる多くの低利益率製品を生産するブランドの場合、競合するSKU(準代替品)に既に在庫過多があるなら、特定のSKUに対して高いサービスレベルを維持することは利益を生む選択肢とはならないかもしれません。
さらに、DDMRPが提案する優先順位付けスキームは本質的に一面的であり、すなわち自身の在庫目標(バッファー)の遵守に依拠しています。しかし、実際のサプライチェーンにおける意思決定はほぼ常に多次元的な問題です。例えば、メーカーが1000ユニットのバッチを生産した後、通常はその1000ユニットを海上輸送用コンテナに梱包しますが、サプライチェーン先端で品切れが差し迫っている場合、1000ユニットのうち100ユニットを航空輸送することが、事前に差し迫った品切れを軽減する上で利益につながるかもしれません。ここで、輸送手段の選択はサプライチェーンの優先順位付け課題における追加次元となります。この課題に対処するためには、優先順位付けの手法が、企業にとって利用可能な多様な選択肢に関連する経済的推進力を統合する能力を持たなければなりません。
優先順位付けの一部として考慮すべき他の次元には、以下が含まれる場合があります:
- 需要を増減させるための価格調整(場合によっては二次販売チャネルを通じて)
- 市場で代替品が見つかる場合における自社製造か外部調達かの選択(通常、プレミアム価格で)
- 在庫の有効期限(在庫構成に関する詳細な洞察が必要)
- 返品リスク(流通パートナーが未販売品を返品する選択肢を持つ場合)
したがって、DDMRPがMRPによる二元的な全か無かのアプローチと比較して優先順位付けがより柔軟な手法であると述べる点は正しいものの、DDMRP自体が提案する優先順位付けスキームは、全体としてはかなり不完全です。
Lokadの見解
DDMRPのモットーは「完璧さではなく、人のために作る」であり、Lokadでは量的-供給-チェーン-マニフェスト(QSCM)の視点を通して、クラシックなIBMのビジョン「機械は動作すべきで、人は考えるべき」という考え方を支持しています。
QSCMは、すべての平凡なサプライチェーンの意思決定は自動化されるべきだという仮説から始まります。この視点は、有能なサプライチェーン担当者が在庫管理、購買、価格設定といった日常的な意思決定に時間を費やすにはあまりにも希少かつ高価であると考えられていることを強調します。これらのすべての意思決定は自動化されるべきであり、自動化することで担当者は数値レシピ自体の改善に注力できるのです。財務的観点から見ると、QSCMはシステムを維持するために消費されるOPEXとしての労働日数を、システムの継続的な改善に投資されるCAPEXへと転換します。
DDMRPの観点は、有能なサプライチェーン担当者が大量に訓練可能であるという仮説に基づいており、その結果、雇用者のコストを低減するとともに、従業員の離職に伴うサード-パーティー-物流の要因も軽減できると考えています。DDMRPは平凡なサプライチェーンの意思決定を生み出すプロセスを確立しますが、完全な自動化を達成することは主な目標ではなく、機会があれば自動化を取り入れるに留まります。
興味深いことに、業界がQSCMの視点に舵を切るのかDDMRPの視点に舵を切るのかは、ある程度観察可能なはずです。もしQSCMの視点がより広範に採用されれば、サプライチェーン管理チームは、数名の非常に才能ある個人が大企業のパフォーマンスを左右する金融業界の定量的トレーダーのような、いわゆる「タレント」産業に近い形へと進化するでしょう。逆に、DDMRPの視点が広く採用されれば、サプライチェーン管理チームは、個々の卓越した人材がシステムに与える影響がごく僅かである一方、チーム全体が豊富で十分に訓練され、優れた企業文化が企業間の差を生むような、成功したフランチャイズ、たとえばスターバックスの店舗マネージャーのような形へと進化するでしょう。
資料
- Demand Driven Material Requirements Planning (DDMRP)、バージョン3、PtakとSmith著、2019年
- Orlicky’s Material Requirements Planning, 3rd edition、Carol A. PtakとChad J. Smith著、2011年
注釈
-
離散数学において、グラフとは頂点(ノードまたは点とも呼ばれる)と辺(リンクまたは線とも呼ばれる)の集合です。辺に向きがある場合、そのグラフは有向とされ、辺に数値―すなわち重み―が割り当てられている場合、そのグラフは加重されていると言います。また、辺をそれぞれの向きに従って辿ったときに循環が存在しなければ、そのグラフは非巡回であると言います。 ↩︎
-
彩色スキームとは、グラフの各頂点にカテゴリ的な特性を割り当てることです。DDMRPの場合、選択肢はデカップリングポイントであるか否かの2つ、すなわち2色のみとなります。 ↩︎
-
コンピューターサイエンスにおいて、分割統治法とは、問題を2つ以上の関連する部分問題に再帰的に分割し、それらが直接解決できるほど単純になるまで続けるアルゴリズムです。このアプローチは1945年にジョン・フォン・ノイマンによって先駆けられました。 ↩︎
-
2020年2月24日時点で、Demand Driven Institute™は営利団体であり、自らをDemand Driven Education, Training, Certification & Complianceに関する世界的権威(sic)と定義しています。そのビジネスモデルは、DDMRPに特化したトレーニングセッションや教材の販売を中心としています。 ↩︎
-
2020年2月24日時点で、Demand Driving Institute™(demanddriveninstitute.com)のホームページには、典型的な改善例として以下の数値が示されています:ユーザーは常に97~100%の定時充填率を達成し、複数の業界セグメントで80%以上のリードタイム短縮が実現され、顧客サービスを向上させながら通常30~45%の在庫削減が達成されています。 ↩︎
-
MRPベンダーは、製品の計画、予測、最適化能力について確かに大胆な主張をしました。しかし、ガイド・ミシュランが、魔法のように美味しいキャッチコピーを掲げたコーンフレークブランドが料理界の星評価の対象となり得るかどうかを評価することを気にしないのと同様に、我々の評価は主に最先端のサプライチェーンパフォーマンスの提供に注力していた関係者に向けられるべきなのです。 ↩︎